coregeek
Active Member
I recently completed a scratch build of Tauriel's Daggers from The Hobbit films. Thought I'd share the complete build process.
This is a comprehensive build covering the prop master build, molding/casting, and final finishing.
I have 50+ photos so I'll post in sections.
I started with a piece of scrap 5/8" thick MDF that I sawed down to 3/8" thick.
Transferred reference to MDF.
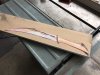
Drilled out spots to make cutouts with scroll saw.
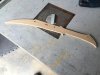
Cutouts made. I decided not to cutout the two small hole on the blade. I didn't want to deal with them during the molding process.
I also decided to cut them in one string so I wouldn't have to fiddle with removing the scroll saw blade a bunch.
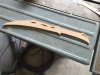
Starting the bevel of the blade. I freehanded this with my bench belt sander.
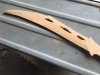
Cleaned up the transition of the blade to handle by hand cutting and sanding.
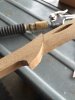
Still rough cuts at this point.
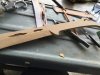
Shaping the blunt edge top.
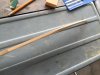
Overall progress.
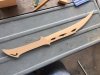
Built up the handle thickness by gluing MDF slats on each side.
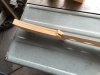
Shaped the handle with combination of belt sander and hand sanding. The handle had several angles that made it a bit of a challenge to get right.
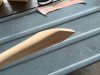
That's it for the MDF.
Next up adding all the detailing.
This is a comprehensive build covering the prop master build, molding/casting, and final finishing.
I have 50+ photos so I'll post in sections.
I started with a piece of scrap 5/8" thick MDF that I sawed down to 3/8" thick.
Transferred reference to MDF.
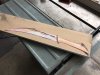
Drilled out spots to make cutouts with scroll saw.
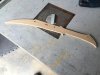
Cutouts made. I decided not to cutout the two small hole on the blade. I didn't want to deal with them during the molding process.
I also decided to cut them in one string so I wouldn't have to fiddle with removing the scroll saw blade a bunch.
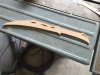
Starting the bevel of the blade. I freehanded this with my bench belt sander.
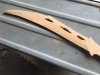
Cleaned up the transition of the blade to handle by hand cutting and sanding.
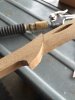
Still rough cuts at this point.
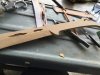
Shaping the blunt edge top.
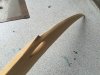
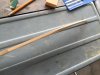
Overall progress.
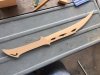
Built up the handle thickness by gluing MDF slats on each side.
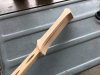
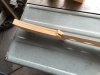
Shaped the handle with combination of belt sander and hand sanding. The handle had several angles that made it a bit of a challenge to get right.
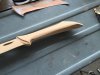
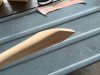
That's it for the MDF.
Next up adding all the detailing.
Last edited: