verdaera
Active Member
Hello!
I hope someone can give me some advice. I've been reading up on mold making, and made a couple simple one-part molds. I need to cast a couple more complicated shapes and I have *no clue* on how to divide these in a mold, I can't seem to find info about that in my research.
I am making Leia's Ceremonial gown from the end of A New Hope. I am going to start by making Worbla versions of her jewelry to start, but I want to take my time making a clay sculpt of her necklace and bracelet, and possibly make the final version out of silver metal clay. However, when casting I am not sure how to divide up the mold; won't it leave a seam I have to deal with wherever the divide is?
I also want to... evil word here... recast a prop I have because I haven't the skill to make the Yavin medal. Not for resale obviously, just because I'd like a resin copy that I won't worry about getting ruined or lost at events, and if I have a Han, Luke and Chewie at an event I'd like multiple medals. However, this one has a slot for the ribbons so, same problem. Does anyone have any advice? I was also planning on using the oomoo silicone rubber from Smooth On as I can get that locally at Dick Blick, unless it's not advised.

I hope someone can give me some advice. I've been reading up on mold making, and made a couple simple one-part molds. I need to cast a couple more complicated shapes and I have *no clue* on how to divide these in a mold, I can't seem to find info about that in my research.
I am making Leia's Ceremonial gown from the end of A New Hope. I am going to start by making Worbla versions of her jewelry to start, but I want to take my time making a clay sculpt of her necklace and bracelet, and possibly make the final version out of silver metal clay. However, when casting I am not sure how to divide up the mold; won't it leave a seam I have to deal with wherever the divide is?
I also want to... evil word here... recast a prop I have because I haven't the skill to make the Yavin medal. Not for resale obviously, just because I'd like a resin copy that I won't worry about getting ruined or lost at events, and if I have a Han, Luke and Chewie at an event I'd like multiple medals. However, this one has a slot for the ribbons so, same problem. Does anyone have any advice? I was also planning on using the oomoo silicone rubber from Smooth On as I can get that locally at Dick Blick, unless it's not advised.
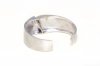
