zachsbanks547
Active Member
I’m embarking on making my own Apollo A7L Spacesuit replica.
I certainly don’t expect to be up to Mr. Nagata level (it’s a holy grail for me to own one of his replicas someday), but hopefully I can make something reasonably accurate that can be made with what what I have available.
I started by gathering several hundred reference pictures, reading every A7L build I could find, and reading “Spacesuit: Fashioning Apollo” by Nicholas de Monchaux (which honestly didn’t give a ton of information that would be useful to a replica maker, but was super interesting nonetheless and should be required reading for any Apollo aficionado).
I’ve pulled fabric patterns for a couple pieces from Mr. Nagata's post to get me started, but I haven’t done much with them other than a couple test pieces with scrap fabric.
I’ve done a couple test pieces of the shoulder to try and get the sizing right for me, and I did some tests of the snoopy cap, using scrap nylon and power mesh (which I’ll also use in the final). And I cut out the shapes for the ears out of foam, which will eventually sit in pockets on the cap.
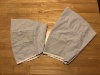
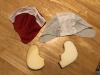
I’ve got a good amount of the hardware done as of right now. I could go the route of 3D printing the pieces, but then I’d have to buy the files for them, which as of right now is prohibitively expensive (unless anyone here knows of a cheaper way to get super accurate 3D files).
So because of the that, I decided to go the route of trying to replicate the hardware of the suit using PVC plumbing parts from the hardware store as much as I possibly could.
For the chest connectors, I started with a 3/4” PNC union.
I screwed it apart and removed one of the connectors and ended up with this.
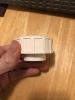
Than I used my Dremel to widen the hole on the front side.
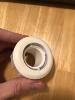
For the flange with the screws, I started with a 3” PVC test cap, and used a 3” hole saw to cut out a disk, a smaller hole saw to cut a hole just big enough for the back connector of the union, and then drilled and countersunk screw holes around the edges.
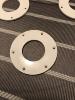
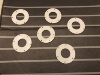
The electrical connector was the same deal, but I used a 3/4” threaded adapter instead of the union.
I then painted everything with Dupli-Color Metalcast (ground coat and then red or blue where appropriate). It worked really well and came out looking great IMO.
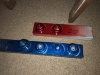
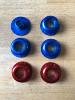
The glove construction I used is very similar to what Mr. Nagata did in his post. I used 4” white vinyl duct as the convolute and stapled polyurethane-coated work gloves from Harbor Freight onto one end.
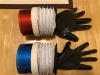
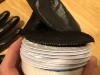
The wrist rings are also PVC parts. The glove side is a 3" spigot female PVC adapter. I trimmed the smaller-diameter side to length and sanded off the bumps on the other half.
The suit side is a 3” coupler that I cut right in half and used the two halves for each side. The narrow side of the spigot adaptor fits right into the coupler. I also drilled holes for magnets to hold them together. And then painted with Metalcast, same as the chest connectors. I added velcro to each side which will be the connection to the fabric, once I get there.
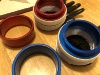
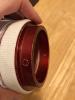
I started working on test pieces for the glove fabric. The transition from the White Beta cloth to the black fabric (Vinyl? Pleather? Not sure what was used originally) was really doing my head in. The black fabric always looked too wide compared to my reference. But after some help from my sewing wizard mother, I think I got a test piece that’s looking pretty good.
The test piece uses ribbed jersey fabric, but I got some stretchy, black pleather to use for the final piece.

I kept going back and forth on what to do for the neck ring. But I ended up finding a website where I could buy Schedule 80 PVC by the inch and I got three inches of 10”, Sch 80 PVC. It’s a tad bit thicker than the real neck rings were, which I may try to correct at some point. But otherwise, I think it’ll work well for my purposes.
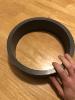
Hopefully I can move onto the soft parts soon. I have a bunch of scrap to do tests with, which I plan on doing. And then I need to get around to buying my final fabric.
I’m planning on using Joann white sport nylon as the Beta cloth, and ironing board fabric as the Chromel-R.
Construction-wise, I plan to go the route Nagata did in his post. Meaning lining it in velour and velcroing boning on the inside to give it structure.
Any help, tips or tricks, or anything else anyone can give me would be appreciated.
I certainly don’t expect to be up to Mr. Nagata level (it’s a holy grail for me to own one of his replicas someday), but hopefully I can make something reasonably accurate that can be made with what what I have available.
I started by gathering several hundred reference pictures, reading every A7L build I could find, and reading “Spacesuit: Fashioning Apollo” by Nicholas de Monchaux (which honestly didn’t give a ton of information that would be useful to a replica maker, but was super interesting nonetheless and should be required reading for any Apollo aficionado).
I’ve pulled fabric patterns for a couple pieces from Mr. Nagata's post to get me started, but I haven’t done much with them other than a couple test pieces with scrap fabric.
I’ve done a couple test pieces of the shoulder to try and get the sizing right for me, and I did some tests of the snoopy cap, using scrap nylon and power mesh (which I’ll also use in the final). And I cut out the shapes for the ears out of foam, which will eventually sit in pockets on the cap.
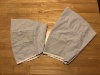
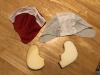
I’ve got a good amount of the hardware done as of right now. I could go the route of 3D printing the pieces, but then I’d have to buy the files for them, which as of right now is prohibitively expensive (unless anyone here knows of a cheaper way to get super accurate 3D files).
So because of the that, I decided to go the route of trying to replicate the hardware of the suit using PVC plumbing parts from the hardware store as much as I possibly could.
For the chest connectors, I started with a 3/4” PNC union.
I screwed it apart and removed one of the connectors and ended up with this.
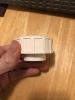
Than I used my Dremel to widen the hole on the front side.
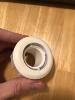
For the flange with the screws, I started with a 3” PVC test cap, and used a 3” hole saw to cut out a disk, a smaller hole saw to cut a hole just big enough for the back connector of the union, and then drilled and countersunk screw holes around the edges.
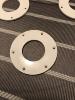
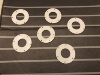
The electrical connector was the same deal, but I used a 3/4” threaded adapter instead of the union.
I then painted everything with Dupli-Color Metalcast (ground coat and then red or blue where appropriate). It worked really well and came out looking great IMO.
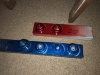
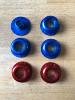
The glove construction I used is very similar to what Mr. Nagata did in his post. I used 4” white vinyl duct as the convolute and stapled polyurethane-coated work gloves from Harbor Freight onto one end.
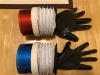
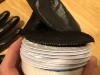
The wrist rings are also PVC parts. The glove side is a 3" spigot female PVC adapter. I trimmed the smaller-diameter side to length and sanded off the bumps on the other half.
The suit side is a 3” coupler that I cut right in half and used the two halves for each side. The narrow side of the spigot adaptor fits right into the coupler. I also drilled holes for magnets to hold them together. And then painted with Metalcast, same as the chest connectors. I added velcro to each side which will be the connection to the fabric, once I get there.
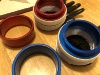
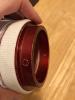
I started working on test pieces for the glove fabric. The transition from the White Beta cloth to the black fabric (Vinyl? Pleather? Not sure what was used originally) was really doing my head in. The black fabric always looked too wide compared to my reference. But after some help from my sewing wizard mother, I think I got a test piece that’s looking pretty good.
The test piece uses ribbed jersey fabric, but I got some stretchy, black pleather to use for the final piece.

I kept going back and forth on what to do for the neck ring. But I ended up finding a website where I could buy Schedule 80 PVC by the inch and I got three inches of 10”, Sch 80 PVC. It’s a tad bit thicker than the real neck rings were, which I may try to correct at some point. But otherwise, I think it’ll work well for my purposes.
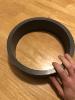
Hopefully I can move onto the soft parts soon. I have a bunch of scrap to do tests with, which I plan on doing. And then I need to get around to buying my final fabric.
I’m planning on using Joann white sport nylon as the Beta cloth, and ironing board fabric as the Chromel-R.
Construction-wise, I plan to go the route Nagata did in his post. Meaning lining it in velour and velcroing boning on the inside to give it structure.
Any help, tips or tricks, or anything else anyone can give me would be appreciated.
Last edited: