Doctor Octoroc
Sr Member
Yes. Both?
That's doable. The advantage to having the insert for the dial is that the bottom of the sonic rests beneath the main surface of the console so since the dial has stepped tiers, the sonic can rest at its proper position in relation to the port and the port rests on a higher tier in the dial at a position that looks right as far as the height and proportions are concerned. For a stand alone version, I would need to add height and it wouldn't look right.
Here's a section view of the add on for the dial thus far - I'm still working out the way the clear bits for the light will fit in.
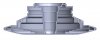
You can see where the outside of the port ends is much higher than the depth below it to which the butt of the sonic would need to go to be a the proper position. If this was a stand along port stand, the but would need to be much higher and the sonic would either sit too high in the stand or the port would need to be elongated to accommodate the extra height.