zachfejes
New Member
Hey there everybody - this is my first thread on RPF, and I'm looking forward to sharing!
Like a lot of you, I loved the Mandalorian. It's well written, fun, and feels like a great addition to the Star Wars universe. I also fell in love with the Beskar armour. As soon as I saw it, I knew I wanted to recreate it. I've been interested in prop-making for a long while (I'm a big fan of Adam Savage & Bill Duran, and I've been looking for a good project to get into it for a while).
A bit about me: I'm an electrical engineering graduate, maker, and problem-solver. I have a lot of CAD and 3D printing experience, and I'm going to be using a lot of that for this project. I'm also a competent sewer, which will definitely come in handy for the flight suit.
What I'm NOT great at yet: Painting, weathering, scaling prints to be wearable.
So here's the plan: I'm going to work through this project over the next several months (quarantine has made this a lot more accessible), and I'll be maintaining a record of the design and build on this thread. If you have any suggestions, comments, criticisms, or advice, please give me a shout - I'm always looking to learn, and there are probably a WHOLE lot of techniques and tools I don't know about yet.
I decided to start on the Pauldrons, which I've modeled and rendered. I still need to find the right scale for them on my shoulders, so I'm going to be building a scale rig out of paper/cardboard, and get an idea of what size feels right.
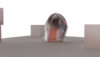
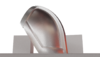
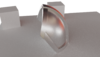
Like a lot of you, I loved the Mandalorian. It's well written, fun, and feels like a great addition to the Star Wars universe. I also fell in love with the Beskar armour. As soon as I saw it, I knew I wanted to recreate it. I've been interested in prop-making for a long while (I'm a big fan of Adam Savage & Bill Duran, and I've been looking for a good project to get into it for a while).
A bit about me: I'm an electrical engineering graduate, maker, and problem-solver. I have a lot of CAD and 3D printing experience, and I'm going to be using a lot of that for this project. I'm also a competent sewer, which will definitely come in handy for the flight suit.
What I'm NOT great at yet: Painting, weathering, scaling prints to be wearable.
So here's the plan: I'm going to work through this project over the next several months (quarantine has made this a lot more accessible), and I'll be maintaining a record of the design and build on this thread. If you have any suggestions, comments, criticisms, or advice, please give me a shout - I'm always looking to learn, and there are probably a WHOLE lot of techniques and tools I don't know about yet.
I decided to start on the Pauldrons, which I've modeled and rendered. I still need to find the right scale for them on my shoulders, so I'm going to be building a scale rig out of paper/cardboard, and get an idea of what size feels right.
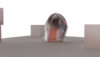
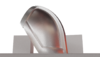
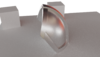