Harliquinn
New Member
So, I guess it's my turn to build and post about my Han in Carbonite. I'd like to thank Zenix in particular for answering a lot of questions and helping me track down others to order from. My build will be using the following parts:
Han Body Kit: King Jawa
Box Kit: Zenix
Panels and Greeblie Kit: Zenix
Hero Panel Light Kit: Modeljag
I'm still hoping to get a Panel #2 Light Kit.
My box kit came in and I started laying things out. I decided to do something similar to QCWolf, and build a lip on my front edge so I could construct Han on a carefully fitted front panel. It will be supported by 3 cross pieces.
Day 1
I started by gluing up the sides and then assembling the box walls. I reinforced the inside corners with metal corner pieces. I ended up with two corner supports per corner, though the picture shows only one. I was surprised that I didn't need to open up the 90 degree corner supports at the top but so far it looks fine.
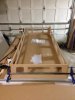
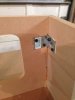
After this was done, I decided I wanted to use biscuit joints on the front borders for extra support and strength. I lined up the edges with each front border panel, marked them, and cut out biscuit holes.
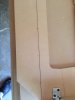
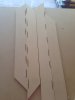
Then, I cut biscuit holes in each front edge corner where they attach to each other and then glued up the front edge. That's drying right now, so I will attach the front border to the box this evening.
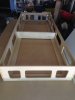
Han Body Kit: King Jawa
Box Kit: Zenix
Panels and Greeblie Kit: Zenix
Hero Panel Light Kit: Modeljag
I'm still hoping to get a Panel #2 Light Kit.
My box kit came in and I started laying things out. I decided to do something similar to QCWolf, and build a lip on my front edge so I could construct Han on a carefully fitted front panel. It will be supported by 3 cross pieces.
Day 1
I started by gluing up the sides and then assembling the box walls. I reinforced the inside corners with metal corner pieces. I ended up with two corner supports per corner, though the picture shows only one. I was surprised that I didn't need to open up the 90 degree corner supports at the top but so far it looks fine.
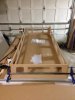
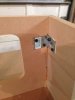
After this was done, I decided I wanted to use biscuit joints on the front borders for extra support and strength. I lined up the edges with each front border panel, marked them, and cut out biscuit holes.
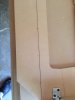
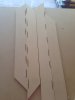
Then, I cut biscuit holes in each front edge corner where they attach to each other and then glued up the front edge. That's drying right now, so I will attach the front border to the box this evening.
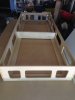
Last edited: