Not be that person (Ok I will be that person haha!), but whenever you complete and are satisfied with your build, are you planning on releasing the files or selling casts? I'd love to get my hands on a snub nose. I also discovered recently that Dave's kits are no longer available. Thanks!
Lol... right now all I'm focused on is seeing if what I spent all this time designing can actually even be built!
One of the pitfalls of programs like Fusion 360 seems to be how easy it is to design something incredibly complex that works in the computer, but that you can't actually produce with the tools at your disposal. Oh, to have a 1/4 million dollar six axis CNC mill of my own some day...
Lately I've mostly been continuing to fail at casting grips while also familiarizing myself with materials and processes I have little to no actual hands-on time with.
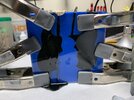
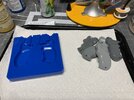
My problems seem to be 3-fold:
1.) The specific angle the grips are at in the mold I've made traps bubbles in a few locations no matter what I do:
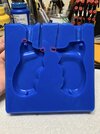
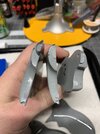
2.) The Smooth-cast 300 sets up too quickly for me to get the whole mess into the pressure chamber to get rid of the bubbles that way. I mean 3 minutes? Really?
3.) The plexiglass "back plate" I'm using to get an ultra flat surface on the side of the grips that face the blaster (you can see it in the pic higher up in this post with the resin curing in it) is only 1/8" thick and distorts under the pressure of my clamps leading to this:
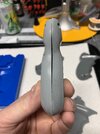
So I've ordered some Smooth-cast 310 which has an extra 18 minutes of pot life which should give me ample time to get the mold in the chamber and up to pressure before the resin begins to set. Unfortunately the trial size is backordered on Amazon for some reason so I won't be getting that until March 9th or so unless I want to pay Smooth-on $25 shipping on a $30 item.
I've also bought some 1/4" polycarbonate that I'm going to use as the backing for the next round of castings. Hopefully it's rigid enough to eliminate the distortion issue.
Finally I've also been exploring another idea Dave used in his original Snub build: 3D printing "metamolds". He did it on a much smaller scale there (with the binding post) but basically you design a multi-part mold in the computer, printing "negative" molds (I know, molds are negatives themselves... I don't know how better to explain it) then casting silicone into those. The end result is you can have really cleanly produced multi-part, interlocking molds that have never contained the actual piece being cast in them.
I'm hoping it'll help with some of the super complex shapes in this build like the receiver and the magazine well:
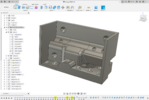
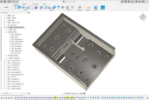
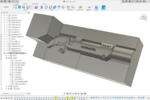