Hello again, all, it's nice to be back and to share my latest build.
This thread will cover my version of the 5' ANH filming model's round topside quad laser turret, built at twice studio scale. The project was inspired by the many fantastic photographs that so many other fans have taken of ILM's original model. The sheer number of close-up detailed shots made me think "gee, I'd like to build just one of the recessed maintenance bays on the Falcon", or maybe a 'pie-slice' section of hull as a large, individual piece. I finally settled on the gun turret as something I thought was within a reasonable scope.
Another reason for the double studio scale is that I plan to more or less scratch build the entire piece so I won't have to spend time trying to find 1/16 or 1/8 scaled versions of model kits that probably don't exist anyway. The research of the details, scales, and proportions is enough work for me. Not that there won't be various geegaws (excuse me, greeblies) used in the build, but I intend to make a replica, not a duplicate, so please, no rivet-counting.
And as to research, this whole thing would be impossible without the serious scholarship and generous sharing of knowledge by members of the RPF. In particular I must acknowledge Andre vfxsup64, whose thread "SW – ANH (5 Foot) - Studio Scale Millennium Falcon Build" provided the crucial dimensions I needed to get started. I simply doubled all the figures.
So, here goes.
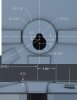
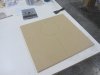
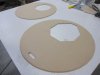
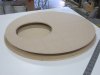
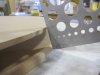
The main top and bottom surfaces are 1/4" MDF with a 1" rib inside to bring it to 1 3/4" thick (or tall). I routed a nice bevel on the bottom panel so I would have a clean taper when I built up the side walls.
This thread will cover my version of the 5' ANH filming model's round topside quad laser turret, built at twice studio scale. The project was inspired by the many fantastic photographs that so many other fans have taken of ILM's original model. The sheer number of close-up detailed shots made me think "gee, I'd like to build just one of the recessed maintenance bays on the Falcon", or maybe a 'pie-slice' section of hull as a large, individual piece. I finally settled on the gun turret as something I thought was within a reasonable scope.
Another reason for the double studio scale is that I plan to more or less scratch build the entire piece so I won't have to spend time trying to find 1/16 or 1/8 scaled versions of model kits that probably don't exist anyway. The research of the details, scales, and proportions is enough work for me. Not that there won't be various geegaws (excuse me, greeblies) used in the build, but I intend to make a replica, not a duplicate, so please, no rivet-counting.
And as to research, this whole thing would be impossible without the serious scholarship and generous sharing of knowledge by members of the RPF. In particular I must acknowledge Andre vfxsup64, whose thread "SW – ANH (5 Foot) - Studio Scale Millennium Falcon Build" provided the crucial dimensions I needed to get started. I simply doubled all the figures.
So, here goes.
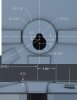
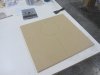
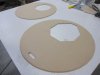
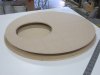
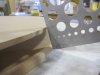
The main top and bottom surfaces are 1/4" MDF with a 1" rib inside to bring it to 1 3/4" thick (or tall). I routed a nice bevel on the bottom panel so I would have a clean taper when I built up the side walls.