Newbie questions here on some parts of the PepAkura process. Please forgive me as I am still reading through everything to get an understanding of all that is involved. Not sure where everyone is but I am here in the US.
Scaling- as I understand it I will have to rescale each wearable piece for my size (6'5"). Is there a standard conversion ratio or what is involved with changing from size A to size B?
Foam - what exactly is it? Where does one get it? How much does it usually run and what are he advantages/disadvantages over paper/resin/bondo?
Basic construction- I am a scale modeler and understand that hobby takes time. In general how long does it take to cut, construct and finish a component?
My youngest son will love some of this stuff for playing. If I just make a paper helmet would it hold up at all for him to play with for a while?
I appreciate any help and insight one can offer.
Sent from my iPhone using Tapatalk
Scaling: You can use the point-to-point measurement function in Pepakura Designer to check measurements and approximate fitting sizes. To calculate your estimated scale as a starting point, find the modeler's default scale and size. Take default scale divided by default height in inches, then multiply this number by your height in inches.
So a suit that's a default of 425 scale to measure 81 inches tall, you'd divide 425/81= about 5.25. Multiply 5.25 by your height in inches (77), and you get 404. That would be your approximate scale.
Foam: most people use EVA foam. There are a lot of sources, depending on what country you live in. I buy mine from Sears and from Chair Cushion, Boat Cushions, Replacement Cushions, Patio Cushion. Foam work usually has less detail, but builds faster and is cheaper than resin/bondo paper builds.
Time: everybody builds at different speeds. It usually takes me 3 hours or so for an average component, but it all depends.
Paper helmet: It might hold up for a little while, but even with 110# cardstock it's pretty flimsy. If he steps on it, it's done. A cheap option that can be done indoors, pick up an epoxy resin like this on Amazon: Amazon.com: Environmental Technology 8-Ounce Kit Casting' Craft Casting Epoxy, Clear
This is more than enough to put two coats on 4 helmets, and it'll make the piece A LOT more rigid.
Hey all, just a small question. Does it really matter what kind of chicago/binding post screws I use? Also, is it possible that someone has a diagram of where to place washers and the screws to join two pieces.
Any help is appreciated, thanks.![]()
I use 1/2" chicago screws from amazon (I build with 1/4" foam). For elbow and knee joints, I just add foam tabs so that the joint overlaps on each side, and then approximate the pivot point. You can also make adjustable joints by adding velcro to the inside of each joint. You then make the joint with the Chicago screw connection separately, glue velcro to each strip, and then attach it where it works best and spaces the joint correctly. It gives you a bit of extra adjustment room for length as well. Here's a Mk42 arm I added the velcro too, so the length is adjustable. In this pic, only the forearm-side is adjustable:
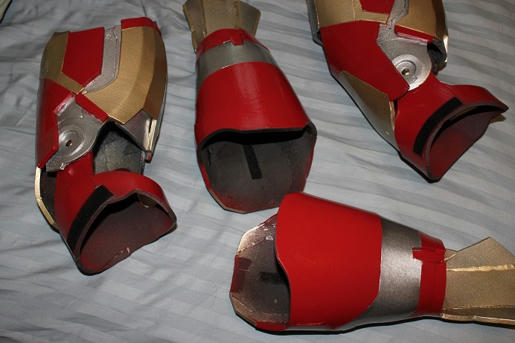