I continue to be blown away by your design revisions! I have only two comments: when I did some scaling of my own, I did get 3" for the housing length/diameter, but the threaded stud seemed more correct at the 5.5" over-all length stud from McMaster (link). Note that the threads on the stud extend internally past the "equator" of the ball. (though perhaps the thread adapter you're using will change this). The ball also scaled out closer to 1.35-1.375" in my estimation; I see some space left between your 1.45" circle and the actual edges of the ball in the screencap... Totally agreed on the room for some idealization here, though.
My Sideshow Grogu arrived a couple of days ago so I wanted to mention that the diameter of their shifter ball is exactly that of the 1-3/8" McMaster-Carr ball knob (link) (measured 1.36" Ss vs 1.362" M-C). In the photos below, the Sideshow one looks a little taller, only because the "south pole" has less cut off due to it having a magnet rather than a large threaded hole; diameters measured on the silver portion match within two thou.
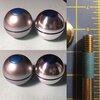
Also, the McMaster dimensioned drawing is not entirely correct. Here it is with the actual dimensions of the ball and depth of functional threading. The tape in the photo above shows how much of the threaded stud is within the ball when fully tightened down (0.71").
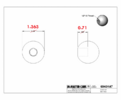
One final note -- five full threads of the 4" partially threaded stud remain visible when the ball is tightened down, which matches the screencap. However, the McMaster drawing for the 5" and 5.5" threaded stud list the threaded length as 1.25" vs the 1" threaded length on the 4" threaded stud. So that detail may not work out as well.
My Sideshow Grogu arrived a couple of days ago so I wanted to mention that the diameter of their shifter ball is exactly that of the 1-3/8" McMaster-Carr ball knob (link) (measured 1.36" Ss vs 1.362" M-C). In the photos below, the Sideshow one looks a little taller, only because the "south pole" has less cut off due to it having a magnet rather than a large threaded hole; diameters measured on the silver portion match within two thou.
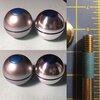
Also, the McMaster dimensioned drawing is not entirely correct. Here it is with the actual dimensions of the ball and depth of functional threading. The tape in the photo above shows how much of the threaded stud is within the ball when fully tightened down (0.71").
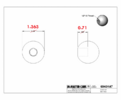
One final note -- five full threads of the 4" partially threaded stud remain visible when the ball is tightened down, which matches the screencap. However, the McMaster drawing for the 5" and 5.5" threaded stud list the threaded length as 1.25" vs the 1" threaded length on the 4" threaded stud. So that detail may not work out as well.