I wanted to show you guys how I handled my MK42 Pep build. Maybe that helps some of you out. Since I had no experience working with Epoxy Resin and wanted a non-toxic way of building a MK42 Pep Helmet INDOORS I went ahead and experienced a little. Here are my fails and maybe... wins. This is still a kind of WIP so I will update every time I learn something new. I used gimpee's file for the Helmet.
The first try:
- traditional Pep on 160gr paper.
- used 3mm foamies to help with the details.
- hotglue
So my first MK42 was done with paper in a medium thickness. I put the pep-file together using hot glue. My idea for the little greases on the forehead: using 3mm foamies to ensure the exact space in between them. A picture might help understanding:
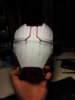
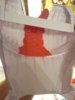
as you can see the greases are pretty accurate this way and you save yourself the trouble with the tiny folds on this thing. The only downside: sanding this area is tricky. You don't want to sand on the foam. On the other hand: since you can get this accurate on the first try, you don't need to sand a lot. I used this trick in other places too.
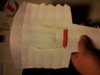
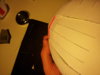
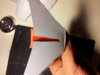
After finishing the pep work i had to harden it. This would be the step where you use Epoxy Resin. I wanted to try something else. Acrylic Resin. It kinda looks like plaster but it isn't. Look it up, it's pretty cool stuff. Also works really great of bond work later. But first... my fail: Since i used medium thickness in my paper... it warped like hell:
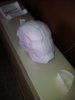
I tried to save it but in the end the warping destroyed the symmetry and it was just frustrating... so...
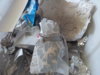
First try - first fail. But I'm not one to give up. the problem was: the paper soaked the moisture from the Acrylic Resin and warped. So i had to make the paper waterproof at least from one side. I could either use non-water-based glue... or laminate the paper.
Second try
- Normal 80gr paper
- laminating sheets
- again 3mm foamies and 5mm foamies for the edges.
I went with the laminated paper option. That means I printed out the pep-pages and laminated it afterwards... but before cutting. The laminating foil bonds with the paper so don't worry about it peeling off. There are different thicknesses too. Choose one that is not too thick.
The result looked like this:
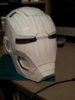
using laminating foil on the pep project had proven some pretty cool advantages: you have very good stability without having to use the thick paper that can be hard to work with. Also: due to the tension it holds its shape even when you deform it temporarily (my helmet fell down). All of that ensures for a clean pep-build. Note that the picture was taken after the first acrylic resin treatment, that is why there are white specks on the front. That being said. This way there was no warping! Awesome! Here are some pictures from the inside:
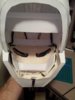
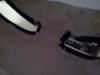
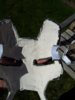
Now, that was something i could work with! Even though this time the scaling went wrong and the helmet was way too big for me. But that didn't matter. So I started working on it. Then there was the disadvantage i noticed: When you sand through the laminating foil you rip off more than you want. So sometimes you have to remove whole pieces from the original paper model... looking like this:
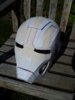
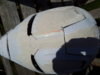
That was a little setback but nothing that some bondowork couldn't fix. Since the paper was very thin that wasn't such a big problem. Note to self: next time laminate only one side of paper and use a medium thick paper again.
I had to deal with that problem in some places so I had to to some bondo-work. Speaking of which, since that stuff is not good for your health and I was looking for alternatives. I found some woodfiller. Like the name says: It is used to fill holes in wood. It has very small grains and has a very fine consistency. It's also pretty hard once it hardened (doesn't take long... 20 minutes for 3mm thickness). It is not toxic and can be sanded pretty easily. Awesome stuff. I stocked up on that instantly.

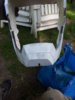
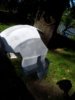
After sanding on the laminating foil proved to be a bigger pain in the A** than I thought: I called it a day and went ahead and painted it:
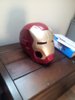
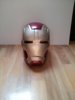
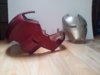
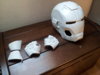
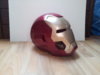
It looks okay but not perfect. It still has some small bumps and imperfections but I am done with this helmet. I might consider doing a run for people who are interested and wanting to work on it a little themselves. It is for pretty big heads. I will post some more information on that later.
Also coming up: Third try with only on laminated side (inside) of the paper. This one turned out pretty good so far.
The first try:
- traditional Pep on 160gr paper.
- used 3mm foamies to help with the details.
- hotglue
So my first MK42 was done with paper in a medium thickness. I put the pep-file together using hot glue. My idea for the little greases on the forehead: using 3mm foamies to ensure the exact space in between them. A picture might help understanding:
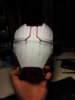
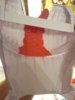
as you can see the greases are pretty accurate this way and you save yourself the trouble with the tiny folds on this thing. The only downside: sanding this area is tricky. You don't want to sand on the foam. On the other hand: since you can get this accurate on the first try, you don't need to sand a lot. I used this trick in other places too.
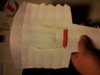
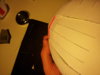
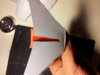
After finishing the pep work i had to harden it. This would be the step where you use Epoxy Resin. I wanted to try something else. Acrylic Resin. It kinda looks like plaster but it isn't. Look it up, it's pretty cool stuff. Also works really great of bond work later. But first... my fail: Since i used medium thickness in my paper... it warped like hell:
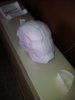
I tried to save it but in the end the warping destroyed the symmetry and it was just frustrating... so...
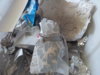
First try - first fail. But I'm not one to give up. the problem was: the paper soaked the moisture from the Acrylic Resin and warped. So i had to make the paper waterproof at least from one side. I could either use non-water-based glue... or laminate the paper.
Second try
- Normal 80gr paper
- laminating sheets
- again 3mm foamies and 5mm foamies for the edges.
I went with the laminated paper option. That means I printed out the pep-pages and laminated it afterwards... but before cutting. The laminating foil bonds with the paper so don't worry about it peeling off. There are different thicknesses too. Choose one that is not too thick.
The result looked like this:
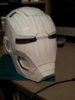
using laminating foil on the pep project had proven some pretty cool advantages: you have very good stability without having to use the thick paper that can be hard to work with. Also: due to the tension it holds its shape even when you deform it temporarily (my helmet fell down). All of that ensures for a clean pep-build. Note that the picture was taken after the first acrylic resin treatment, that is why there are white specks on the front. That being said. This way there was no warping! Awesome! Here are some pictures from the inside:
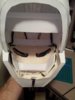
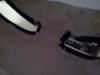
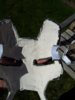
Now, that was something i could work with! Even though this time the scaling went wrong and the helmet was way too big for me. But that didn't matter. So I started working on it. Then there was the disadvantage i noticed: When you sand through the laminating foil you rip off more than you want. So sometimes you have to remove whole pieces from the original paper model... looking like this:
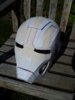
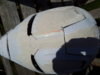
That was a little setback but nothing that some bondowork couldn't fix. Since the paper was very thin that wasn't such a big problem. Note to self: next time laminate only one side of paper and use a medium thick paper again.
I had to deal with that problem in some places so I had to to some bondo-work. Speaking of which, since that stuff is not good for your health and I was looking for alternatives. I found some woodfiller. Like the name says: It is used to fill holes in wood. It has very small grains and has a very fine consistency. It's also pretty hard once it hardened (doesn't take long... 20 minutes for 3mm thickness). It is not toxic and can be sanded pretty easily. Awesome stuff. I stocked up on that instantly.

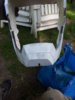
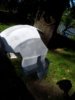
After sanding on the laminating foil proved to be a bigger pain in the A** than I thought: I called it a day and went ahead and painted it:
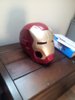
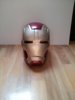
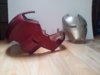
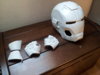
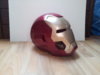
It looks okay but not perfect. It still has some small bumps and imperfections but I am done with this helmet. I might consider doing a run for people who are interested and wanting to work on it a little themselves. It is for pretty big heads. I will post some more information on that later.
Also coming up: Third try with only on laminated side (inside) of the paper. This one turned out pretty good so far.
Attachments
Last edited: