guitarpirate
Active Member
I am super-excited about building my own Elysium exo suit because I love cyber-punk and sci-fi. Hoping to wear it on stage when playing electronic metal 
Started about three months ago, my plan is to solid-model all parts in AutoCAD using photo references, prototype using paper and cardboard to make sure scale is right, then submit for manufacturing to a CNC shop. Last step is finishing, which will involve tapping all connections with metric threads (both male and female), painting, stamps, decals, and final assembly. I am planning to use aluminum for most parts, and SS316 for certain connectors that are most likely to get bent or break. Hard rubber and poly will be used for soft under-lays (such as soft plates underneath the shirt where spine and hips connect) as well as some inside parts of pistons. Really hoping that mfg. will not run over $4000, otherwise I will have to prioritize the parts and leave easier ones for myself to forge and polish.
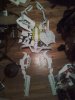
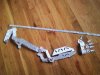

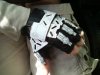
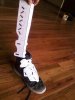
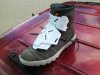
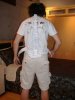
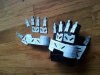
The 2D drawings are almost done, and prototyping is close to completed. I have maybe 3-4 drawings left to do before I create another branch and get busy projecting geometry, revolving and extruding
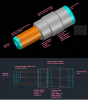
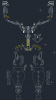
Started about three months ago, my plan is to solid-model all parts in AutoCAD using photo references, prototype using paper and cardboard to make sure scale is right, then submit for manufacturing to a CNC shop. Last step is finishing, which will involve tapping all connections with metric threads (both male and female), painting, stamps, decals, and final assembly. I am planning to use aluminum for most parts, and SS316 for certain connectors that are most likely to get bent or break. Hard rubber and poly will be used for soft under-lays (such as soft plates underneath the shirt where spine and hips connect) as well as some inside parts of pistons. Really hoping that mfg. will not run over $4000, otherwise I will have to prioritize the parts and leave easier ones for myself to forge and polish.
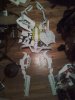
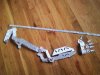

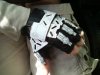
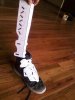
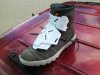
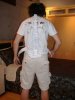
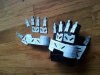
The 2D drawings are almost done, and prototyping is close to completed. I have maybe 3-4 drawings left to do before I create another branch and get busy projecting geometry, revolving and extruding
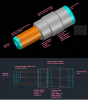
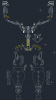
Last edited: