Some progress on the ingots!
I've played around a lot with different types of resin and variations of coloring and finishing:
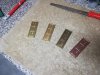
While those look okay on first glance, they were all still a little dissapointing on close inspection. (I put quite some effort into getting a nice smooth surface for the casting-master. But any kind of treatment on the cast resin-parts - no matter if with or without sanding or priming - always messes up the surface a bit.)
But then I went for cold-metal-casting. And this finally brought the look and haptics I was hoping for!
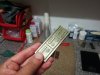
For this one I used brass-powder mixed into the resin.
While the parts look a little dull coming freshly out of the mold, polishing them with steel wool brings out the metallic shine. They got a nice heavy metal-feel to them and there is no color which could rub off! (Actually the opposite. Handling them around will intensify the weathered metallic look).
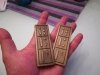
While I'm pretty sure that this is NOT what the prop guys did for the movie, I still found this to be my perfect approach for this task!
I wanted something that looks and feels authentic- and this is it! (The parts actually also smell like metal! Yeah, I know I'm crazy...:lol)
Now testing out pewter- and bronze-powder for the other color-shadings.
Stay tuned!
I've played around a lot with different types of resin and variations of coloring and finishing:
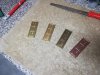
While those look okay on first glance, they were all still a little dissapointing on close inspection. (I put quite some effort into getting a nice smooth surface for the casting-master. But any kind of treatment on the cast resin-parts - no matter if with or without sanding or priming - always messes up the surface a bit.)
But then I went for cold-metal-casting. And this finally brought the look and haptics I was hoping for!
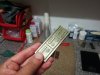
For this one I used brass-powder mixed into the resin.
While the parts look a little dull coming freshly out of the mold, polishing them with steel wool brings out the metallic shine. They got a nice heavy metal-feel to them and there is no color which could rub off! (Actually the opposite. Handling them around will intensify the weathered metallic look).
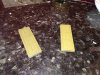
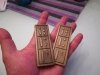
While I'm pretty sure that this is NOT what the prop guys did for the movie, I still found this to be my perfect approach for this task!
I wanted something that looks and feels authentic- and this is it! (The parts actually also smell like metal! Yeah, I know I'm crazy...:lol)
Now testing out pewter- and bronze-powder for the other color-shadings.
Stay tuned!
Last edited: