lilwolf555
New Member
Evening!
So, I'm somewhat new to prop-making (made an old Mando I never finished) but I'm looking to start a few projects in the coming months, hopefully, depending on moving and other fun life things depending on job.. anyway.
Guts from Berserk
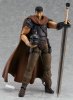
2nd is Gordon's HEV suit from Half Life 2
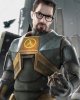
My question is on materials.
Debating on Worbla and Sintra. I have worked a little with Sintra so know some basics to it.
Sintra..
1. How complex of curves can it take? I don't have any left to test myself so rather ask before ordering. Can it do something as complex as the area directly below the Lambda symbol on Gordon's chestplate? Or is that too complex of a curve for it and would need to use worbla to fill in that part?
Worbla..
1. Would making the entire thing of worbla and using EVA foam to thicken/back it be cheaper ultimately than using all sintra for these?
2. Would it be worth it to use worbla over Sintra due to the fact I can re-form what I need easier and scraps can be remolded to use yet again, or would average cost outweigh these benefits?
3. I DO have some parts of an HEV suit (from an old build that need a LOT of work and some parts re-made completely).. I could use worbla to copy its shape entirely, couldn't I? Then trim/mod it to fit better and thicken it with Foam? Pic of old parts below.
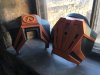
Just wanting to get some more experienced opinions than random results I find online basically parroting the same info over and over and it being hard to find specifics.
What would you guys recommend for this - worbla or sintra and why? And is using worbla to copy the non-broken parts of my old suit feasible ? (just placing worbla over it and heating to get the shape)
(I did not make the old suit in the pic - it was a paid commission that I regret getting - they did shapes right, but other parts are.. yeah and the fiberglass was terrible, breaking apart on some parts etc. I just want to start from scratch on my own instead of gambling on a commission again)
So, I'm somewhat new to prop-making (made an old Mando I never finished) but I'm looking to start a few projects in the coming months, hopefully, depending on moving and other fun life things depending on job.. anyway.
Guts from Berserk
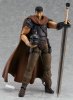
2nd is Gordon's HEV suit from Half Life 2
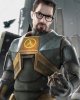
My question is on materials.
Debating on Worbla and Sintra. I have worked a little with Sintra so know some basics to it.
Sintra..
1. How complex of curves can it take? I don't have any left to test myself so rather ask before ordering. Can it do something as complex as the area directly below the Lambda symbol on Gordon's chestplate? Or is that too complex of a curve for it and would need to use worbla to fill in that part?
Worbla..
1. Would making the entire thing of worbla and using EVA foam to thicken/back it be cheaper ultimately than using all sintra for these?
2. Would it be worth it to use worbla over Sintra due to the fact I can re-form what I need easier and scraps can be remolded to use yet again, or would average cost outweigh these benefits?
3. I DO have some parts of an HEV suit (from an old build that need a LOT of work and some parts re-made completely).. I could use worbla to copy its shape entirely, couldn't I? Then trim/mod it to fit better and thicken it with Foam? Pic of old parts below.
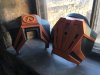
Just wanting to get some more experienced opinions than random results I find online basically parroting the same info over and over and it being hard to find specifics.
What would you guys recommend for this - worbla or sintra and why? And is using worbla to copy the non-broken parts of my old suit feasible ? (just placing worbla over it and heating to get the shape)
(I did not make the old suit in the pic - it was a paid commission that I regret getting - they did shapes right, but other parts are.. yeah and the fiberglass was terrible, breaking apart on some parts etc. I just want to start from scratch on my own instead of gambling on a commission again)