Well, it's been a very interesting evening. On the one hand, I've got my recipe for the hero emitter down.
On the other hand, this thing isn't gonna work in acrylic. So after my little work break, I'm switching to polycarbonate (Lexan).
So here's how things shaped up tonight:
I started by cutting down one of my 1/16" bits with an angle grinder (the bandsaw was in full butterknife mode). Then I chucked it WAY back, and commenced to drillin'. I pulled the bit out a couple of millimeters after every plunge, went really slow, and dumped OPEC's entire supply of oil on it as I went. Got a pretty good result. Yay!!
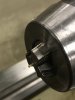
Sadly, this result was not to be repeated.
Yup. That ain't just a little wobble. That's a frakkin'
helix. TF?
WT actual F??
But I really wanted to get at least a finished prototype -- helix or no, I needed to get these measurements figured out. Holes, taper, the whole... uh... the whole... uh...
Ball of wax. That was it.
So as you can see, I repeated my drill-taper-drill-taper thing, except this time I only had to do it once. This definitely looks right to my eye (except for the whole wobble thing), so my finished pieces will use these measurements.
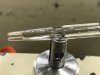
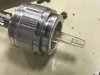
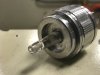
So without further Apu...
Cuz he's off to vote early for Trump...
Here's the final taper specs I'm gonna go with (until I get better measurements of the original):
Taper: 4º
Taper length: 1" (ish)
Front hole: 1/16"
Back hole: 9/64"
Tip divot: 5/64"
Tip diameter: 0.2" (ish)
Shaft diameter: 5/16"
Trust me, baby, it's 5/16" of pure awesome.
The final length and rear profile are still TBD. I have to basically make that up out of whole cloth, since nobody's ever X-rayed the inside of the nozzle (that I'm aware of). So I'm going to play with the prototype emitter and the 3D-printed prototype brass piece till I figure it out.
So, now...
What's all this about doing these in polycarbonate?
It just so happens that tonight I ran into Adam, the nice mechanical engineer
from Post #366 on Page 15.
And here I had this amazing, accidental pile of helical art in acrylic. So I thought,
hell, why not walk the ten feet or so to the nearest mechanical engineer and ask him, like, WTF, dude?
He took one look and asked first if that was acrylic. I said yes, and his opinion was that it was a thermal problem. In other words, the plastic is overheating and pulling the bit out of whack.
Adam had an interesting solution:
"I avoid acrylic whenever possible."
My whole life has been a lie!!
Lexan, he explained, is WAY better to machine, and doesn't get these problems at all. Also, it's generally much stronger, and way more scratch-resistant than acrylic.
He also told me about vapor polishing, which is apparently really easy with acrylic -- maybe its only advantage over Lexan. You suspend the workpiece in a closed container over a small amount of acetone. The vapors liquefy the outer layer of the acrylic, causing it to re-flow. When it re-solidifies, you've got a smooth, clear finish again. Great way to take out machining marks (yup, that would've saved me a ton of work a year ago).
But after our talk, it was clear the vapor polishing wasn't going to smooth out that frakkin' barber pole inside my emitter, so... Lexan it is!!
So that's how this is gonna go. I have my dimensions now, so all I have to do is lay in some 5/16" polycarbonate stock and get back to work. I think this is where I finally see the light at the end of the tunnel with this piece...
Why does this view look so familiar?
See you guys on the other side!