Okay, so here's the wrap-up on the last two days of lathing phaser bits. And there will be more lathing tonight, because they've got Lathe 1 (Latham, as the ladies call him) running
sweeeeeet.
And I want to turn as much as I can before it gets frakked up again.
1. The faux Kilo knob:
I found the best order to turn it is as follows:
- Turn down the top stud, leaving yourself extra length to finish off at the end.
- Turn the taper. I moved the tool toward the stud to start with (away from the chuck), then switched direction for the last couple of fine passes (to avoid accidentally crashing the tool into the stud and ruining it).
- I did a 55º taper, which looked about right by eye and compared favorably to the Kilo knob. Not identical, since the faux knob looks flatter to me in photos. If I had to guess, I'd say the Kilo knob is more like 50º. Nobody's gonna walk up to me at a con and put calipers and an angle finder on it, so I'm not gonna sweat that.
- Turn down the diameter of the dial part, to around 5/8". This can be loosey-goosey on the midgrade, IMO, depending on the width of the back of the phaser.
- Finish the end of the stud down to a height of 3/32". The diameter is 7/32".
I'm going to paint the stud tonight if I remember.* I've decided to make this midgrade showroom-new, partly because everybody's doing the distressed look, and partly because the machined parts look so pretty, I just don't want to distress them.
*I did not.
2. The 9/16" rings:
Back in the day, Todd (Replicator1701) sent me a piece of tube he'd turned down for the collar that goes around the side dial. It was scored at roughly 1/4" intervals as a cutting guide. I've kept it all these years, since it turned out to be exactly the right size every time I compared it to sources. It matched the resin collar on the MM kit, it matches the collar on the Wand phaser, and it matches the diagrams and photos we've all seen. All I did was part them off, and now I have five rings plus a loose one in a box somewhere. So I think I only need to turn one or two more for a total of five heroes and one or two midgrades.
- The outside diameter of the ring is 9/16".
- The diameter of the side dial is 1/2".
- That makes the wall thickness of the ring about 1/6", minus a couple thou for fitting. Probably best done by sanding the side dial and the inside wall till you're happy with the fit.
3. The midgrade acrylic emitter:
This is basically just a taper. I grabbed some of my 3/8" stock from last year and gave it
a 4º taper, which seems to be just right. Basically, that gives me a 3/16" diameter at the tip, and 5/15" diameter at the back, across a taper length of just about an inch. Without taking calipers to the originals, I can say this looks best to my eye.
So to start, I take off material pretty aggressively, working the tool away from the chuck because I really hate it when the tool crashes into the chuck and gets destroyed. This is only around 80rpm, but at high speeds things can get kinda shrapnelly when that happens.
As I've said previously about turning acrylic, use low speeds.
And here's the proofy pudding that this lathe is now wobble-free: looky them perfect chips!
Also, the taper comes out just gorgeous. No tool chatter, no cracking or shattering, just a nice, smooth, perfect taper. Note -- it looks very clear in these two pix because it's covered in cutting oil. It's actually very frosty, which gets taken care of later.
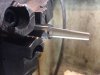
Now that I've got the taper,
I turn down the back to 5/16".
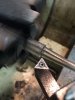
Note in the first picture how rough the shaft part looks compared to the taper. That's because when you're just hogging off material, you want to move your tool faster to save time. It's only when you're doing a finish pass that you want to go really, really slow. For brass or aluminum finish passes, I'll go as slow as 0.02"/sec. Sometimes even slower -- I think the auto feed goes down to 0.0063"/sec.
(However, there's no auto feed when you're turning the taper with the compound slide, so you have to turn that gear wheel by hand. Getting that even and consistent takes practice, but you can get really sweet results that way. And it's much easier to set up -- the other two ways require very lengthy setup with additional gear and it's not worth doing unless you're turning a lot of high-quality parts.)
So I just keep turning it down till my nozzle fits nicely. That's really the easiest way to know when to stop.
And now,
LET THE SANDING BEGIN!!!!
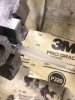
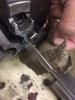
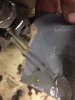
The last sheet there is 1500 grit. In the third photo, you can see I just used cutting oil for the wet sanding, and it worked very well. Also saved me walking over to the slop sink for water.
In retrospect, I shouldn't have started with 320. I wound up with an ever-so-slightly loose fit into the nozzle, meaning I took off too much material after I'd gotten my nice fit. Not a show-stopper by any means, but next time I'm starting with 400 wet. In this case, I think using epoxy to hold the emitter in the nozzle will more than compensate for any looseness.
In any case, I stopped sanding when I was just shy of perfectly clear. No 2000 grit, no polishing with jeweler's rouge. To my eye, that comes closest to matching the photos of the originals:
Finally, it's time for Romeo and Juliet --
parting is such sweet sorrow. Not really appropriate, but I get to show off my Shakespeare quotes.
Uh... anyway, here's me doing the cutty-offy thingy.
So there's one more item off the punch list! I cut it very long in the back to give myself a choice in how far out to let it protrude from the nozzle. I can go from just the tapered part (1") all the way out to ridiculous (a little over 1 1/2").
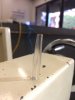
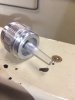
Yay!!
4. The midgrade brass release pin:
Not a big deal, but I'm not happy with my results here. I started with exactly 3/16" stock, because I was too tired to turn it down from anything bigger.
I've found that it's much easier to turn thin items down from fat stock, which seems counterintuitive -- after all, if your stock is already the right diameter, it's less work to finish, right? Nope. If it's a really narrow piece, say, less than 3/4", then you just can't stick it out very far from the end of the chuck, and that makes dancing your tool around it much harder.
Please, tell me more about this dancing tool of yours.
The formula for allowable length from the end of the chuck gives you
4x the diameter of the stock piece without support on the other end, and sticking a live center on the end of such a tiny piece makes things more difficult. If you stick the workpiece out any farther without support, the high speed rotation starts to distort the shape of the stock, and you can end up with anything from garbage to serious injury.
For the emitter piece above, I could stick out much farther than 4x the diameter because (1) the taper removes material from the end, making it lighter than the rest of the stock and thus safer to turn farther out; and (2) I was going at relatively low speeds -- 80rpm or so for the taper, and 230rpm or so for the sanding.
So tonight, I'm going to turn it down from some 5/8" rod stock I have on hand, and I'm sure I'll have a much better time with it. As it is, the parting tool just kept ruining my piece, so I had to saw it off. It'll do just fine since only the last 3/16" or so sticks out from the pistol body, but I'm gonna turn a couple more in case I make other midgrades or for trades.
So that wraps up the wrapup! Here's the result of my last two days' labors:
Not bad if I do say so myself! And I do. Because massive ego.
