SciFiPropFreak
Active Member
Hello there!
I'd like to share some pics and info about this commission I did for a friend of mine early this year:
The Ma'Tok staff, or Goa'uld Staff Weapon from the SG-1 series.
I'm a huge Stargate fan myself, so I couldn't really say no to this...:rolleyes
Planning and scaling: My friend is a little shorter in comparison with Mr. Christopher Judge (imdb says he's 6' 2" (1,88 m)). From my research I got that the actual prop was/is 2,13m long in total.
Scaled to my friends size its pretty much exactly 2m (I have also been told that there are sometimes restrictions at - german - events limiting the maximum length of objects/props you can bring in to 2m, so I'm on the safe side there, too :behave)
From that info and the obvious web search for reference pics, I photoshopped a 3 side view and modeled a rough 3d version in Maya.
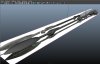
Then I exported it as 3 STL files and used 123D Make to slice it in 3.85mm increments (the average thickness I measured from regular 4mm poplar plywood...not absolutely correct, as it turned out later...)
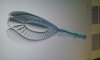
I'd like to share some pics and info about this commission I did for a friend of mine early this year:
The Ma'Tok staff, or Goa'uld Staff Weapon from the SG-1 series.
I'm a huge Stargate fan myself, so I couldn't really say no to this...:rolleyes
Planning and scaling: My friend is a little shorter in comparison with Mr. Christopher Judge (imdb says he's 6' 2" (1,88 m)). From my research I got that the actual prop was/is 2,13m long in total.
Scaled to my friends size its pretty much exactly 2m (I have also been told that there are sometimes restrictions at - german - events limiting the maximum length of objects/props you can bring in to 2m, so I'm on the safe side there, too :behave)
From that info and the obvious web search for reference pics, I photoshopped a 3 side view and modeled a rough 3d version in Maya.
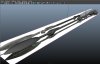
Then I exported it as 3 STL files and used 123D Make to slice it in 3.85mm increments (the average thickness I measured from regular 4mm poplar plywood...not absolutely correct, as it turned out later...)
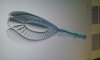
Last edited by a moderator: