TheSt.LouisKid
Sr Member
I forget what thread it was where someone asked to see this.
I lot of people make a mold where you pour the resin in through the top and it fills up like a glass of water. I am sure everyone has noticed that bubbles can churn around in a glass of water as you are pouring. As we know bubbles are bad. :unsure
This process reduces bubbles. With a syringe shoot the resin in where it flows through a runner that comes around under the part. Note how the gate is attached at the bottom. The arrows indicate where the resin flows. The mold fills and air makes it way out without churning. I have had many times where there are no bubbles at all depending on the shape of the part. The funnel shaped cut at the exit is a reservoir that will flow back if the resin has shrinkage. The finished part you see came from this mold. The part has a heat sink quality to the shape and the air made it's way out.
So if you are feeling ambitious give this process a try.
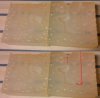
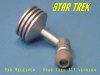
I lot of people make a mold where you pour the resin in through the top and it fills up like a glass of water. I am sure everyone has noticed that bubbles can churn around in a glass of water as you are pouring. As we know bubbles are bad. :unsure
This process reduces bubbles. With a syringe shoot the resin in where it flows through a runner that comes around under the part. Note how the gate is attached at the bottom. The arrows indicate where the resin flows. The mold fills and air makes it way out without churning. I have had many times where there are no bubbles at all depending on the shape of the part. The funnel shaped cut at the exit is a reservoir that will flow back if the resin has shrinkage. The finished part you see came from this mold. The part has a heat sink quality to the shape and the air made it's way out.
So if you are feeling ambitious give this process a try.
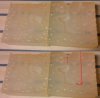
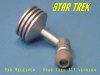