Shapeshifter
New Member
Hello all,
I'm new to the forum. Glad to be here and great to see the threads are active. Lots of great work and tons of talent!
I'm new to sculpting and casting. I'm getting close to wrapping up a piece that I want to cast in resin and I'm looking for some insight on molding. My apologies for the length of this thread, I want to ensure I'm getting all the details out there so my questions make sense.
This piece has a lot of fine detail and nooks and crannies and I'm not certain on how to approach the casting process. This is my biomechanical homage to HR Giger - the head, tail, and two smaller heads all detach.
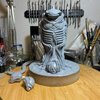
My initial thought was to do a brush on mold for the body with Rebound 25 and a support shell using free-form air. My thought was due to the small details and nooks, brushing in the silicone would be best so details were not missed, and bubbles were avoided, as well as saving a ton of silicone.
The head - was thinking a box mold, or potentially a two piece mold. The two piece mold may be overkill - I'm not certain - but I also wanted to have some practice at doing one. I thought I might be able to run the seam line along the base of the jaw and up along the midline raised rail. The two smaller heads and tail - box molds.
I have a vacuum chamber and a pressure pot. I was thinking the pressure pot would be perfect for curing the resin in the mold due to all of the detail and potential for bubbles, but I've read you should have your silicone mold made under pressure as well to avoid micro bubbles/impressions on your piece when curing. If I do a brush on mold, this doesn't seem possible.
I see this piece as having a hundred different ways to capture bubbles, and have never seen anyone run vents on a brush on mold, so maybe box mold would be best.
My questions:
I'm new to the forum. Glad to be here and great to see the threads are active. Lots of great work and tons of talent!
I'm new to sculpting and casting. I'm getting close to wrapping up a piece that I want to cast in resin and I'm looking for some insight on molding. My apologies for the length of this thread, I want to ensure I'm getting all the details out there so my questions make sense.
This piece has a lot of fine detail and nooks and crannies and I'm not certain on how to approach the casting process. This is my biomechanical homage to HR Giger - the head, tail, and two smaller heads all detach.
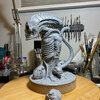
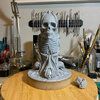
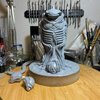
My initial thought was to do a brush on mold for the body with Rebound 25 and a support shell using free-form air. My thought was due to the small details and nooks, brushing in the silicone would be best so details were not missed, and bubbles were avoided, as well as saving a ton of silicone.
The head - was thinking a box mold, or potentially a two piece mold. The two piece mold may be overkill - I'm not certain - but I also wanted to have some practice at doing one. I thought I might be able to run the seam line along the base of the jaw and up along the midline raised rail. The two smaller heads and tail - box molds.
I have a vacuum chamber and a pressure pot. I was thinking the pressure pot would be perfect for curing the resin in the mold due to all of the detail and potential for bubbles, but I've read you should have your silicone mold made under pressure as well to avoid micro bubbles/impressions on your piece when curing. If I do a brush on mold, this doesn't seem possible.
I see this piece as having a hundred different ways to capture bubbles, and have never seen anyone run vents on a brush on mold, so maybe box mold would be best.
My questions:
- Would I be better off doing the body in a box mold, allowing for as many flues as needed, as well as putting the silicone under pressure when making the mold?
- When putting a sculpt under pressure while making the silicone mold: do I run the risk of the sculpture collapsing under the pressure (this is sculpted in Monster clay medium)? I haven't seen anyone remark on this, and cannot find anything about it.
- the nooks, crannies, etc. - are they going to post significant problems? I thought the brush mold approach might overcome this due to being able to apply thick silicone to any undercuts.