01binary
Active Member
It's still very early in the game, but after reading & following some advice I got the next jump in quality:
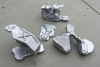
- Keep metal cooler. The hotter the metal is at the time of pouring, the more it will bind with air & water in the atmosphere to create hydrogen inclusions, which results in a horrible looking surface.
- Keep metal from getting too cool. Wrap the crucible and/or the ceramic mold into a ceramic blanket to curb heat loss on transfer.
- Pour slowly (just like with wax) to let gasses escape from the vents while metal is going into the sprues.
- Maintain a large thermal mass of metal just above the mold, to increase the force pushing the metal inside the mold. This is a low-tech alternative to vacuum casting or spinning centrifuge. The result is improved fills on thin and intricate mold cavities.
- Carefully degass with tablets just before the pour
- Fire ceramic molds as long as possible (but not higher than 500 F) to remove all water. Any remaining water will convert into hydrogen upon contact with molten metal and result in gas entrapment.
Wax casts prepared for box molding:
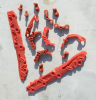
Another batch: parts attached inside respective boxes for pouring UltraVest investment:
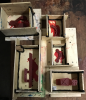
Removing from boxes after investment solidified overnight:
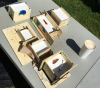
Wax burnt out and investment de-watered:

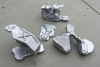
- Keep metal cooler. The hotter the metal is at the time of pouring, the more it will bind with air & water in the atmosphere to create hydrogen inclusions, which results in a horrible looking surface.
- Keep metal from getting too cool. Wrap the crucible and/or the ceramic mold into a ceramic blanket to curb heat loss on transfer.
- Pour slowly (just like with wax) to let gasses escape from the vents while metal is going into the sprues.
- Maintain a large thermal mass of metal just above the mold, to increase the force pushing the metal inside the mold. This is a low-tech alternative to vacuum casting or spinning centrifuge. The result is improved fills on thin and intricate mold cavities.
- Carefully degass with tablets just before the pour
- Fire ceramic molds as long as possible (but not higher than 500 F) to remove all water. Any remaining water will convert into hydrogen upon contact with molten metal and result in gas entrapment.
Wax casts prepared for box molding:
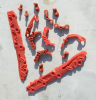
Another batch: parts attached inside respective boxes for pouring UltraVest investment:
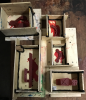
Removing from boxes after investment solidified overnight:
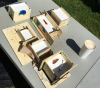
Wax burnt out and investment de-watered:

Last edited by a moderator: