Starside Armory
New Member
Hello! This is my build of the MIDA Multitool scout rifle from Destiny. It is predominately layered MDF, then molded and cast in resin. This is my second serious gun build, so I was learning a lot as I went.
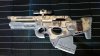
The scout rifle grip design appears to be based on an FN P90, a gun that I happened to have lying around from airsofting, ages ago. I drew a template in InkScape.
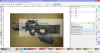
I cut the main body from MDF - one layer each of 3/4", 1/2" and 1/4". I cut the P90 grip as close as I could - luckily the gun has some plating that covers most of this seam. The plating and everything white is 2mm Celtec.
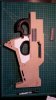
I don't have a lathe, so I used a drill press, a rubber expansion plug and the P90's brass barrel to turn the piece of 1" conduit that makes up the bolt. I used large hand files to carve the grooves. Less than ideal, but it came out alright.
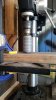
More misuse of the press to drill the connecting pin shaft. This worked, but I don't recommend it.
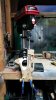
First time using a table-mounted router for the foregrip grooves. Somehow that test piece came out better than my subsequent passes.
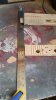
Here are some detail pictures of the nearly completed master.
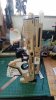
The flippy display folds in on a 1/8" steel rod. The rail is another part from the P90. I was happy to recycle my first airsoft gun in this way! The open scope is PVC conduit turned on the makeshift lathe and an inexpensive but solid ring mount.
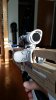
This LED torch is gently compression fit and toggled by pressing on the lens. The lens is covered with some adhesive laminate advertised as headlight tint. I hope to never encounter this tint on the road.
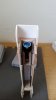
Final primer coat. This modular design was not only to make building and molding it easier. It also lets me build front ends from different scout rifles, which all share a similar receiver design.
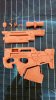
Claying feels like the most time consuming step. It was only near the end that I thought of this strip method to easily create a uniform surface. The silicone plug between the carrying handles worked well, except for that little circular part hanging off one corner. That was very thin and did not work at all.
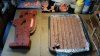
I tried to avoid claying for this part. It worked, but the thin shroud over the LED didn't cast well and I had to rebuild it from scratch on each copy. What I feel does not work is the traditional cone/dimple shaped registration key. In the future I plan to use marbles for more "puzzle piece" shaped reg keys. This should not only align the mold halves, but discourage them from shifting and separating as well.
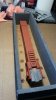
Despite the block mold shape in the image above, I didn't want to buy anything solid to make the walls out of and instead went with fiberglass mothermolds over Rebound 25 silicone rubber. I prefer Plastipaste for the ease of use, but I thought it would be too expensive and heavy for this gun. This was my first experience with fiberglass. I found that 10 mil cloth is too stiff for any contours. The 6 mil seemed alright. I also learned a lot about how to better shape the molds - I thought undercuts and weird angles on the keys would help keep the mother mold in a very specific position, but it turns out that just makes it really annoying to stick the mold back in it.

I was pleasantly surprised that this all-in-one accessory mold worked so well.
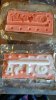
Unwrapping these presents is either extremely rewarding and relieving, or incredibly aggravating. I didn't think to photo the aggravating ones, but I did end up selling some of them. The big pieces are rotocast with Smoothcast 300, and the smaller pieces are just, um, regular old stationary cast.
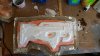
After many failed casts, it was somewhat therapeutic to restore the meticulously crafted detail of the master. This is my entire dusty/hazmat workspace, so in most cases I can't work on different stages simultaneously.
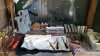
Is there an easier way to mask a bunch of details? The only other thing I could think of was Plastidip, but that seemed much harder to clean up.
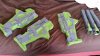
I used two layers of the vaseline technique for the extremely worn paint job.
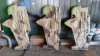
Fast forward a little (characteristic of last-minute-panic work), and here is the completed gun. Steps I didn't photograph include simple wiring for the ammo display, brown and black acrylic washes, leather cord and pouches sewn by my girlfriend (we both learned how to use my sewing machine for those), and remaking each scope from scratch because of an ill-conceived mold.
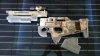
The ammo display is a pre-wired white LED behind clear acrylic, an SPST switch, and a 9V battery. The display graphics are vinyl decals printed at Kinko's. The switch protrudes up from the battery compartment, beneath the scope. The charging handle is affixed with a a snippet of clothes hangar rod and is a simple fix if it were to be broken off.
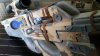
The magazine has a 2" x 3/4" storage compartment (actually I just wanted to pour less resin). The dovetail holds the magazine in place on its own, but the magnet ensures it stays put.
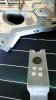
The front end and receiver interlock around a wooden dowel, secured by post fasteners. This is also how the battery compartment is accessed.
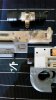
The trigger was a huge gamble because I didn't verify that my design would actually work until I had finished every other step. This is only because I didn't have the guts to experiment by drilling holes in the master. Components are a 1/8" steel rod with washers on each side and a 5/16" OD spring. Luckily it worked, although I wish I had made the recessed area larger so that I could hide the spring up there. An unintended side effect of this design is that the spring makes a satisfying clicking noise when it compresses into the hole it rests in.
That's it! Here are the three I could get ready in time for Comic Con Honolulu. This was my first con as an artist, and it was a lot of fun even though I only sold a couple of second rate raw casts!
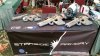
Beach photoshoot and con album: http://imgur.com/a/YkjZe
Despite a lot of headaches in the casting stage, I'm very happy with the finished product. Thanks for checking it out!
-Curtis
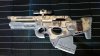
The scout rifle grip design appears to be based on an FN P90, a gun that I happened to have lying around from airsofting, ages ago. I drew a template in InkScape.
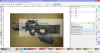
I cut the main body from MDF - one layer each of 3/4", 1/2" and 1/4". I cut the P90 grip as close as I could - luckily the gun has some plating that covers most of this seam. The plating and everything white is 2mm Celtec.
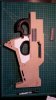
I don't have a lathe, so I used a drill press, a rubber expansion plug and the P90's brass barrel to turn the piece of 1" conduit that makes up the bolt. I used large hand files to carve the grooves. Less than ideal, but it came out alright.
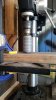
More misuse of the press to drill the connecting pin shaft. This worked, but I don't recommend it.
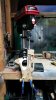
First time using a table-mounted router for the foregrip grooves. Somehow that test piece came out better than my subsequent passes.
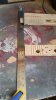
Here are some detail pictures of the nearly completed master.
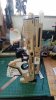
The flippy display folds in on a 1/8" steel rod. The rail is another part from the P90. I was happy to recycle my first airsoft gun in this way! The open scope is PVC conduit turned on the makeshift lathe and an inexpensive but solid ring mount.
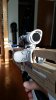
This LED torch is gently compression fit and toggled by pressing on the lens. The lens is covered with some adhesive laminate advertised as headlight tint. I hope to never encounter this tint on the road.
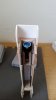
Final primer coat. This modular design was not only to make building and molding it easier. It also lets me build front ends from different scout rifles, which all share a similar receiver design.
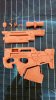
Claying feels like the most time consuming step. It was only near the end that I thought of this strip method to easily create a uniform surface. The silicone plug between the carrying handles worked well, except for that little circular part hanging off one corner. That was very thin and did not work at all.
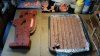
I tried to avoid claying for this part. It worked, but the thin shroud over the LED didn't cast well and I had to rebuild it from scratch on each copy. What I feel does not work is the traditional cone/dimple shaped registration key. In the future I plan to use marbles for more "puzzle piece" shaped reg keys. This should not only align the mold halves, but discourage them from shifting and separating as well.
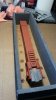
Despite the block mold shape in the image above, I didn't want to buy anything solid to make the walls out of and instead went with fiberglass mothermolds over Rebound 25 silicone rubber. I prefer Plastipaste for the ease of use, but I thought it would be too expensive and heavy for this gun. This was my first experience with fiberglass. I found that 10 mil cloth is too stiff for any contours. The 6 mil seemed alright. I also learned a lot about how to better shape the molds - I thought undercuts and weird angles on the keys would help keep the mother mold in a very specific position, but it turns out that just makes it really annoying to stick the mold back in it.

I was pleasantly surprised that this all-in-one accessory mold worked so well.
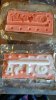
Unwrapping these presents is either extremely rewarding and relieving, or incredibly aggravating. I didn't think to photo the aggravating ones, but I did end up selling some of them. The big pieces are rotocast with Smoothcast 300, and the smaller pieces are just, um, regular old stationary cast.
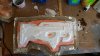
After many failed casts, it was somewhat therapeutic to restore the meticulously crafted detail of the master. This is my entire dusty/hazmat workspace, so in most cases I can't work on different stages simultaneously.
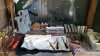
Is there an easier way to mask a bunch of details? The only other thing I could think of was Plastidip, but that seemed much harder to clean up.
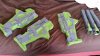
I used two layers of the vaseline technique for the extremely worn paint job.
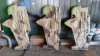
Fast forward a little (characteristic of last-minute-panic work), and here is the completed gun. Steps I didn't photograph include simple wiring for the ammo display, brown and black acrylic washes, leather cord and pouches sewn by my girlfriend (we both learned how to use my sewing machine for those), and remaking each scope from scratch because of an ill-conceived mold.
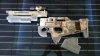
The ammo display is a pre-wired white LED behind clear acrylic, an SPST switch, and a 9V battery. The display graphics are vinyl decals printed at Kinko's. The switch protrudes up from the battery compartment, beneath the scope. The charging handle is affixed with a a snippet of clothes hangar rod and is a simple fix if it were to be broken off.
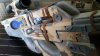
The magazine has a 2" x 3/4" storage compartment (actually I just wanted to pour less resin). The dovetail holds the magazine in place on its own, but the magnet ensures it stays put.
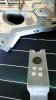
The front end and receiver interlock around a wooden dowel, secured by post fasteners. This is also how the battery compartment is accessed.
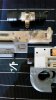
The trigger was a huge gamble because I didn't verify that my design would actually work until I had finished every other step. This is only because I didn't have the guts to experiment by drilling holes in the master. Components are a 1/8" steel rod with washers on each side and a 5/16" OD spring. Luckily it worked, although I wish I had made the recessed area larger so that I could hide the spring up there. An unintended side effect of this design is that the spring makes a satisfying clicking noise when it compresses into the hole it rests in.
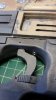
That's it! Here are the three I could get ready in time for Comic Con Honolulu. This was my first con as an artist, and it was a lot of fun even though I only sold a couple of second rate raw casts!
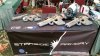
Beach photoshoot and con album: http://imgur.com/a/YkjZe
Despite a lot of headaches in the casting stage, I'm very happy with the finished product. Thanks for checking it out!
-Curtis
Last edited: