shadowhunter23
New Member
I decided to create one of my favorite weapon designs in Destiny, the Mida-Multi Tool. It's a simplistic design with a cool looking sensor screen on the side. I decided to 3d print the gun, but I was not able extract the 3d files from the game. So I used Blender 3D to create the gun.
This is one of my reference photos I used.
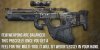
Using Blender I started with the base parts.
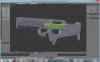
After 40 hours, I was able to finish the details.
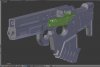
I then sliced up the model to fit the pieces on my MakerBot Replicator 2x.
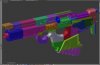
The part I printed. But after printing 4 parts, I realized it was slightly smaller than I needed. I adjusted the scale to print 10% larger and it was a better size.
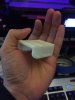
1/3 of parts printed
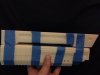
2/3 finished print
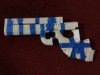
all parts printed.
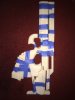
I was really happy with the size. It came out at a little over 2 feet long.
This is one of my reference photos I used.
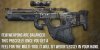
Using Blender I started with the base parts.
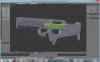
After 40 hours, I was able to finish the details.
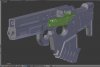
I then sliced up the model to fit the pieces on my MakerBot Replicator 2x.
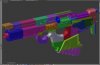
The part I printed. But after printing 4 parts, I realized it was slightly smaller than I needed. I adjusted the scale to print 10% larger and it was a better size.
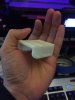
1/3 of parts printed
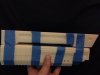
2/3 finished print
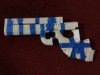
all parts printed.
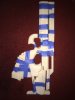
I was really happy with the size. It came out at a little over 2 feet long.
Last edited: