Just finished with a modified base helmet. I made it larger, extended the jawline down a little more, and pulled it under the chin a little.
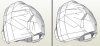
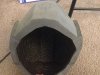
I'm really hating the smoothed look of heat gunned foam when I do it, so I built this new one without any heat gun.

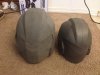
I tried a couple different things. The one I like the most was bringing the hard angles from the crest down into the visor portion. The thing I liked least was that I made it too large this time. It's almost comparable to a motorcycle helmet now and I want it to fit a little more snug than that.
On the bright side, it gives me a couple of pieces that I can test paint. I have a sample set of Smooth-On's 45D that I want to harden the helmet with. I'm going to try documenting that process as detailed as possible, because I know a lot of people, including myself, still have some questions about the results you can get with it.
I think I'm going to build another one slightly smaller than the bigger one I just finished. I'm comfortable enough with some of the trial and error that I'm going to start adding detail to the model and foam them out. Unfortunately, instead of "measure twice, cut once", I'm the type of person that measures 5 times and cuts 5 times. So it's always just a slow methodical process, with a whole lot of thinking and pondering when I do something like this. Pretty fun though.
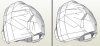
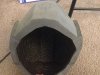
I'm really hating the smoothed look of heat gunned foam when I do it, so I built this new one without any heat gun.

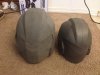
I tried a couple different things. The one I like the most was bringing the hard angles from the crest down into the visor portion. The thing I liked least was that I made it too large this time. It's almost comparable to a motorcycle helmet now and I want it to fit a little more snug than that.
On the bright side, it gives me a couple of pieces that I can test paint. I have a sample set of Smooth-On's 45D that I want to harden the helmet with. I'm going to try documenting that process as detailed as possible, because I know a lot of people, including myself, still have some questions about the results you can get with it.
I think I'm going to build another one slightly smaller than the bigger one I just finished. I'm comfortable enough with some of the trial and error that I'm going to start adding detail to the model and foam them out. Unfortunately, instead of "measure twice, cut once", I'm the type of person that measures 5 times and cuts 5 times. So it's always just a slow methodical process, with a whole lot of thinking and pondering when I do something like this. Pretty fun though.