CheesyGrin
Active Member
Greetings!
For the past 5 months I've been working to recreate the ED-209 stop motion puppet. In those 5 months I've studied pictures, read and re-read "Stop Motion Armature Machining", taken hundreds of screenshots from the movie, built a small machine shop in my garage, and have taught myself basic machining skills. Whew! Lot's of planning, thinking, and buying. :wacko
This project has been SO MUCH work and I get SO LITTLE time to build. I always feel intense pressure to post regular updates! But I'm ready to include others in the build. I could use the power of more brains (and a little encouragement too). The talent in this group is unmatched, imho. I'll do my best to contribute value. Please don't hesitate to offer feedback, criticism, or a kind word. Your input is much appreciated!
Here we go:
Design
I reverse engineered the armature design from two sources: (1) 2 grainy, black and white Cinefex photos and (2) the Horizon vinyl ED-209 kit. I created a 1:1 3D model in SketchUp. I've been using the 3D model to guide the build. SketchUp does not [easily] provide shop drawings automatically from the 3D model. I manually create orthogonal views with dimensions and build details. Here are a few pics of the 3D model, current revision:
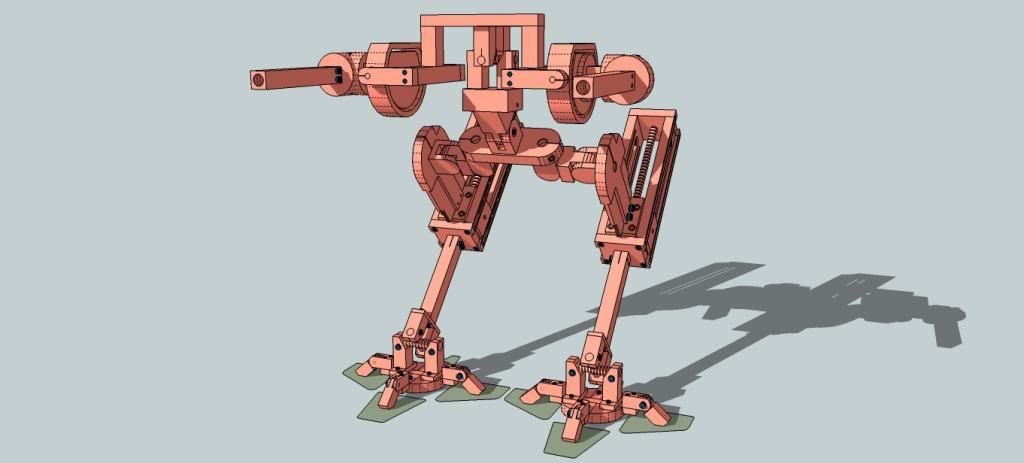


Feedback welcomed!
For the past 5 months I've been working to recreate the ED-209 stop motion puppet. In those 5 months I've studied pictures, read and re-read "Stop Motion Armature Machining", taken hundreds of screenshots from the movie, built a small machine shop in my garage, and have taught myself basic machining skills. Whew! Lot's of planning, thinking, and buying. :wacko
This project has been SO MUCH work and I get SO LITTLE time to build. I always feel intense pressure to post regular updates! But I'm ready to include others in the build. I could use the power of more brains (and a little encouragement too). The talent in this group is unmatched, imho. I'll do my best to contribute value. Please don't hesitate to offer feedback, criticism, or a kind word. Your input is much appreciated!
Here we go:
Design
I reverse engineered the armature design from two sources: (1) 2 grainy, black and white Cinefex photos and (2) the Horizon vinyl ED-209 kit. I created a 1:1 3D model in SketchUp. I've been using the 3D model to guide the build. SketchUp does not [easily] provide shop drawings automatically from the 3D model. I manually create orthogonal views with dimensions and build details. Here are a few pics of the 3D model, current revision:
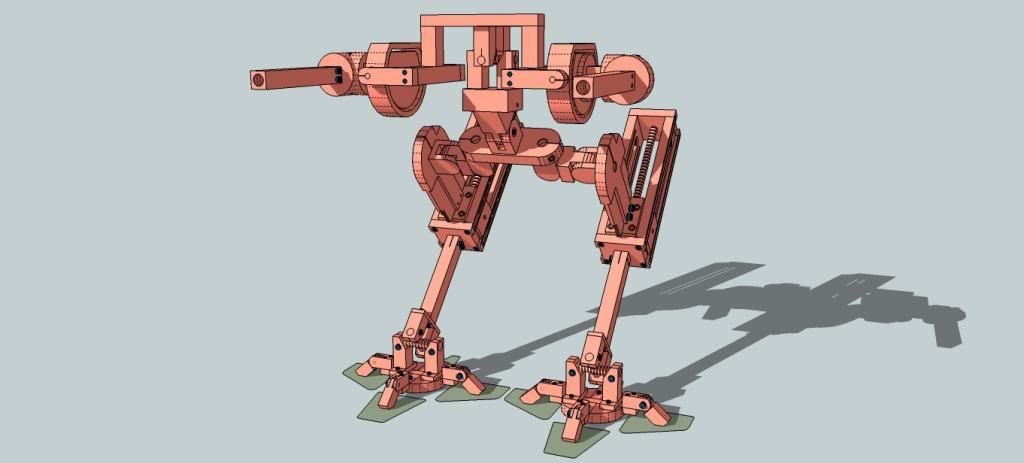


Feedback welcomed!