Some quick updates:
I've decided on Worbla for my armor, primarily because of 1) the need for engraved details in my armor pieces, which would be easier with Worbla than Sintra, 2) I don't have a vacuform or molds (I know sintra can be shaped without these, but those *seem* to be recommended for Sintra), and 3) Sintra seems to be much stiffer than Worbla... since I have some pieces which will be wrapping most of the way around my body (the belt, the armband, the bracelets), some flexibility will be necessary to get them on and of. So, Worbla it is!
I made a first attempt at my Worbla pieces which... didn't go so well. Ha.

You can see the breastplate, my first attempt, is rather lumpy looking below. I think this is due to both 1) me never having worked with Worbla before and not really being familiar with how it heats and handles and 2) the fact that I attempted to merely coat the craft foam underlayer with one layer of Worbla on top... I've heard of people using this method rather than the 'sandwich" method with a piece of Worbla both on top and bottom of your craft foam core, but upon seeing some more videos of people using the sandwich method, I think this helps keep the surface looking a bit smoother than the 1-layer of Worbla method I used, due to the 1 layer needing a lot of hand shaping and pulling around the edges of the Worbla. I THINK this is what made it a bit more lumpy and uneven. So, I'm going to be re-doing these and the remainder of my armor pieces using the sandwich method.
As you can also see below, my second attempt, the tiara, looks a little better than the breastplate, but still more lumpy than I'd like. So I will be attempting that again, using the sandwich method this time.
I also started on getting a pattern for Wonder Woman's chevron corset design. A couple quick notes on this: because the pattern lines cross across where multiple boning channels for the corset would be, and because no bones/boning channels are visible in her corset, this needs to be made as a "floating cover" over a real corset core. Essentially, you make the core layer corset, which is complete except for the grommets at the back and no binding around the edges, then you make a separate floating "cover" in your design (in this case, chevrons), lay it on top of your "core" layer, and sew them together at the back/grommet edges, and the top and bottom edges. THEN you add in grommets and bind the edges (I'll be using a fairly standard binding method of double fold bias tape).
So, I have the pattern I'll be using for my corset "core." In order to get a floating layer which will match up exactly to my core, in order to avoid wrinkling, gapping, etc, I have to use this same pattern, just with different seam lines. To do that, I made a "mockup" of my basic corset pattern, then, while wearing it, had my friend draw chevron lines starting from equidistant points in the center front (we made them 1" wide, but that's really just personal aesthetics, you could make them thicker or thinner). The picture below shows the resulting lines. I also numbered them in order to keep them organized once they're all cut out.
The next step is cutting along these chevron lines, then using these pieces as my new pattern pieces for my floating cover. I'll transfer them to a butcher paper roll I have, and then use those pattern pieces to cut out the red leather I'm using for her corset cover. Remember that you'll need to add seam allowance to these pieces as well!
Tomorrow's updates should include pics of my Worbla battle 2.0 and/or the leather chevron cutting madness!
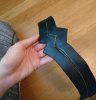

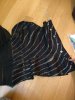