Shaw
Well-Known Member
This is my second attempt at a two-thirds scale version of the 33 inch Enterprise. As such it is most likely best to start out with a brief history of the first attempt before going over the second attempt.
First Attempt
I had always loved the 33 inch model of the Enterprise, even before I was aware that it differed greatly from the 11 foot model, I had always wanted my finished models of the Enterprise to look (feel) like the model we saw sitting on the table in Requiem for Methuselah. While both of my last two models of the Enterprise (both AMT kits, a 1992 rebuild and 1994 build) were quite nice, they fell short on that feel that I had wanted.
Fast forward to 2007 when a number of people were inquiring about aspects of the 33 inch model for their own attempts. People were collecting data but it was generally thought that a set of plans wouldn't be possible without access to the original model (which had been lost), and there seemed to be very few photos of it remaining. Between the photos and some key dimensions of the model I realized that I could reverse engineer plans and had finished a set by the end of that summer.
Honestly, I didn't believe I had the skills to do the build myself and hoped that someone with more talent than I would use the plans for an attempt. On an off chance I printed out a copy of those plans at 66.6% and compared them with a cutaway Enterprise kit that I had sitting around. There was enough resemblance between the overall shape of the secondary hull and nacelles that I figured it my be a good starting point for a modest attempt.
Worried about my lack of recent experience I bought a second kit for backup parts before I started disassembling the parts I needed from the first one (just in case I really screwed up). But throughout all that I had no idea how I was going to fabricate the dorsal and primary hull (both of which I would need to scratch build). As the kit parts started coming together I still needed to do test assemblies to see if I was on the right track, so I built foamcore board stand-ins for the dorsal and primary hull. After I finished what I could at the time, I set aside everything until I could figure out how I was going to make the most important aspects of the model.
After more than a year, I couldn't come up with a cost effective way (I have no disposable income) to make those parts. So I decided to try hand sculpting them starting with the stand-in pieces I had made. I filled the stair steps of them with AMACO Sculptamold (a cellulose-based paper maché) and molded them to the approximate shapes.
This was a learning experience for me and one of the things I had learned was that over time the Sculptamold becomes harder. I had originally believe that I would be able to easily reduce the material to the final shape (even if I walked away from it for a period of time). It took months of fighting the Sculptamold to get the shapes to a reasonable copy of the original model. The top turned out pretty good, the bottom wasn't as good as I had hoped.
Still, even unfinished during test assemblies, I could see that this was far closer in over all feel than any of my previous models. So I was inspired to forge ahead even with those set backs.
Because this model was more than I had previously attempted and hadn't done anything in nearly 15 years, I decided to reduce the load on myself by using third party parts from Don's Light & Magic. I knew these were intended for a replica of the 11 foot model and wouldn't be a perfect match for the 33 inch model, but back when I started I was worried about even finishing and was looking for anything that would make the task less daunting.
In the end I was quite happy with the results (specially given my inexperience), and I find the model to be... a surprise each time it catches my eye (which is more than I could have asked for).
As I hadn't used the parts from the other kit I built it up as a practice model of the Constellation (a mostly stock build of the kit) while working on the Enterprise. It still isn't finished, but here is a comparison between it and my first Enterprise shortly before I finished the Enterprise.
And a couple shots of the finished Enterprise...
And the model as it sits today being used as a reference for my second attempt...
First Attempt
I had always loved the 33 inch model of the Enterprise, even before I was aware that it differed greatly from the 11 foot model, I had always wanted my finished models of the Enterprise to look (feel) like the model we saw sitting on the table in Requiem for Methuselah. While both of my last two models of the Enterprise (both AMT kits, a 1992 rebuild and 1994 build) were quite nice, they fell short on that feel that I had wanted.
Fast forward to 2007 when a number of people were inquiring about aspects of the 33 inch model for their own attempts. People were collecting data but it was generally thought that a set of plans wouldn't be possible without access to the original model (which had been lost), and there seemed to be very few photos of it remaining. Between the photos and some key dimensions of the model I realized that I could reverse engineer plans and had finished a set by the end of that summer.
Honestly, I didn't believe I had the skills to do the build myself and hoped that someone with more talent than I would use the plans for an attempt. On an off chance I printed out a copy of those plans at 66.6% and compared them with a cutaway Enterprise kit that I had sitting around. There was enough resemblance between the overall shape of the secondary hull and nacelles that I figured it my be a good starting point for a modest attempt.
Worried about my lack of recent experience I bought a second kit for backup parts before I started disassembling the parts I needed from the first one (just in case I really screwed up). But throughout all that I had no idea how I was going to fabricate the dorsal and primary hull (both of which I would need to scratch build). As the kit parts started coming together I still needed to do test assemblies to see if I was on the right track, so I built foamcore board stand-ins for the dorsal and primary hull. After I finished what I could at the time, I set aside everything until I could figure out how I was going to make the most important aspects of the model.
After more than a year, I couldn't come up with a cost effective way (I have no disposable income) to make those parts. So I decided to try hand sculpting them starting with the stand-in pieces I had made. I filled the stair steps of them with AMACO Sculptamold (a cellulose-based paper maché) and molded them to the approximate shapes.
This was a learning experience for me and one of the things I had learned was that over time the Sculptamold becomes harder. I had originally believe that I would be able to easily reduce the material to the final shape (even if I walked away from it for a period of time). It took months of fighting the Sculptamold to get the shapes to a reasonable copy of the original model. The top turned out pretty good, the bottom wasn't as good as I had hoped.
Still, even unfinished during test assemblies, I could see that this was far closer in over all feel than any of my previous models. So I was inspired to forge ahead even with those set backs.
Because this model was more than I had previously attempted and hadn't done anything in nearly 15 years, I decided to reduce the load on myself by using third party parts from Don's Light & Magic. I knew these were intended for a replica of the 11 foot model and wouldn't be a perfect match for the 33 inch model, but back when I started I was worried about even finishing and was looking for anything that would make the task less daunting.
In the end I was quite happy with the results (specially given my inexperience), and I find the model to be... a surprise each time it catches my eye (which is more than I could have asked for).
As I hadn't used the parts from the other kit I built it up as a practice model of the Constellation (a mostly stock build of the kit) while working on the Enterprise. It still isn't finished, but here is a comparison between it and my first Enterprise shortly before I finished the Enterprise.
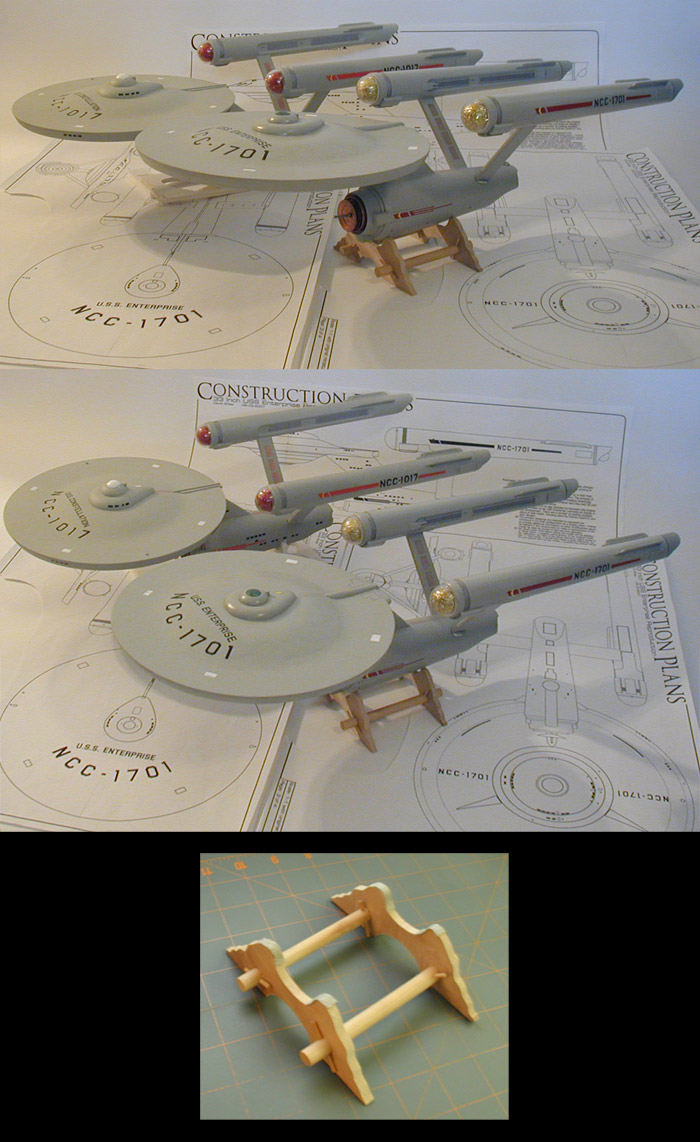
And a couple shots of the finished Enterprise...
And the model as it sits today being used as a reference for my second attempt...
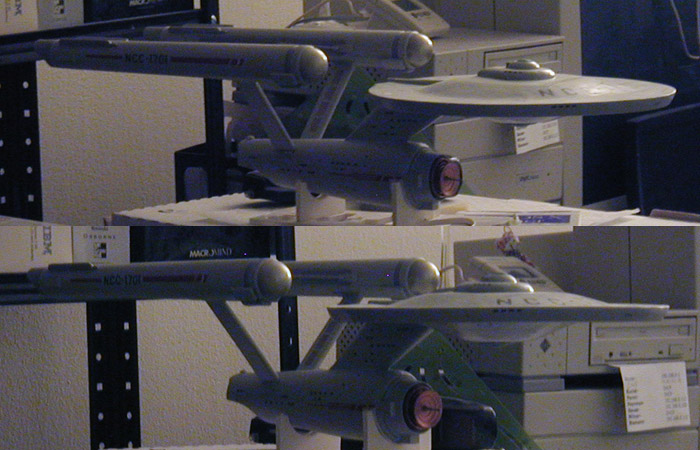