madmanmick
New Member
Hi all,
This is my first time posting on the RPF. Over the last year I've taken somewhat of a liking to sculpting props and cosplay pieces. My first finished piece was a Halo 4 Masterchief helmet in resin, which worked out fairly well. I also got about 90% of the way through a Halo 4 Locus helmet sculpt, but scrapped it so I could work on the Stormrooper helmet.
I've decided that I want to have a new Ep 7 Stormtrooper helmet for when the movie debuts in December here in Australia, so I've taken it upon myself to sculpt the helmet from scratch. I'm using Monster Clay, around 3 buckets worth in this sculpt.
I've attached some pictures so you can see where I'm up to so far. I'm basically happy to accept this as the initial sculpt in clay, and move on to molding and casting in resin, however I would seek some constructive criticism on things I may be able to improve or make more accurate. I have based this design off the multitude of photos available online, but predominantly the photos that have been put up from Celebration 7 of both the ANOVOS replicas and the screen used models. I would be interested in doing a few small casts for people locally if they like the final result.
One particular part I am having trouble scultping cleanly is the fine dimpled effect in the mouth cut. Does anyone know if there is a foam material or other material that could be, or was used, to achieve this effect? I don't think I'll ever get it 100% using clay tools. All the photos I have taken on my Ipad.
Thanks for the help,
Michael.
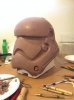
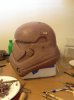
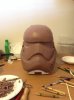
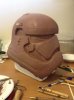
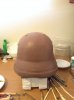
This is my first time posting on the RPF. Over the last year I've taken somewhat of a liking to sculpting props and cosplay pieces. My first finished piece was a Halo 4 Masterchief helmet in resin, which worked out fairly well. I also got about 90% of the way through a Halo 4 Locus helmet sculpt, but scrapped it so I could work on the Stormrooper helmet.
I've decided that I want to have a new Ep 7 Stormtrooper helmet for when the movie debuts in December here in Australia, so I've taken it upon myself to sculpt the helmet from scratch. I'm using Monster Clay, around 3 buckets worth in this sculpt.
I've attached some pictures so you can see where I'm up to so far. I'm basically happy to accept this as the initial sculpt in clay, and move on to molding and casting in resin, however I would seek some constructive criticism on things I may be able to improve or make more accurate. I have based this design off the multitude of photos available online, but predominantly the photos that have been put up from Celebration 7 of both the ANOVOS replicas and the screen used models. I would be interested in doing a few small casts for people locally if they like the final result.
One particular part I am having trouble scultping cleanly is the fine dimpled effect in the mouth cut. Does anyone know if there is a foam material or other material that could be, or was used, to achieve this effect? I don't think I'll ever get it 100% using clay tools. All the photos I have taken on my Ipad.
Thanks for the help,
Michael.
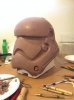
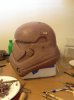
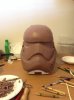
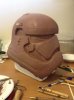
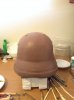