The cannons between the rear engine box and the front gun box changes dimension about 10 times over 3-1/2 feet. Each transition is a separately made combination of plywood frames and styrofoam bulk support rings. The fastest and most accurate way for us to cut these plywood frame is on the CNC router table. Hand routering or jig sawing them would work but would be much less precise. We tested the first piece on a left over piece of the 12mm plywood before committing a full sheet to the machine.
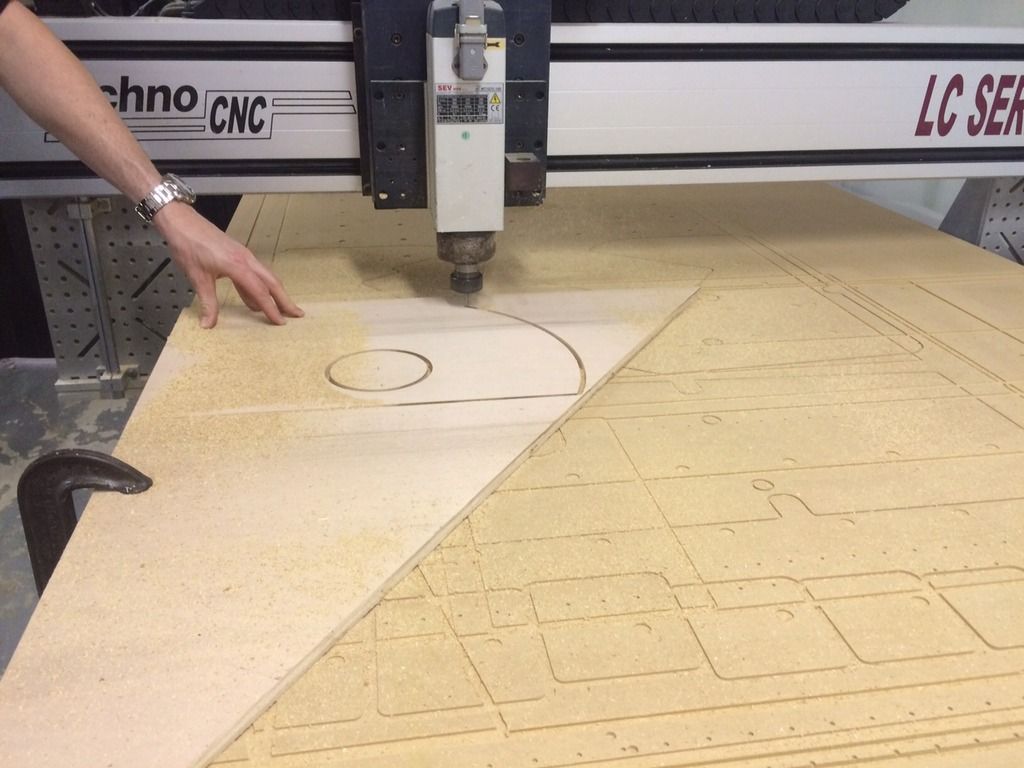
With a test front and rear frame, we glued and nailed three 9" long spacers in place. The rest of the open void will be filled in with foam to support the .090" thick fiberglass skin that will get wrapped around the frames.
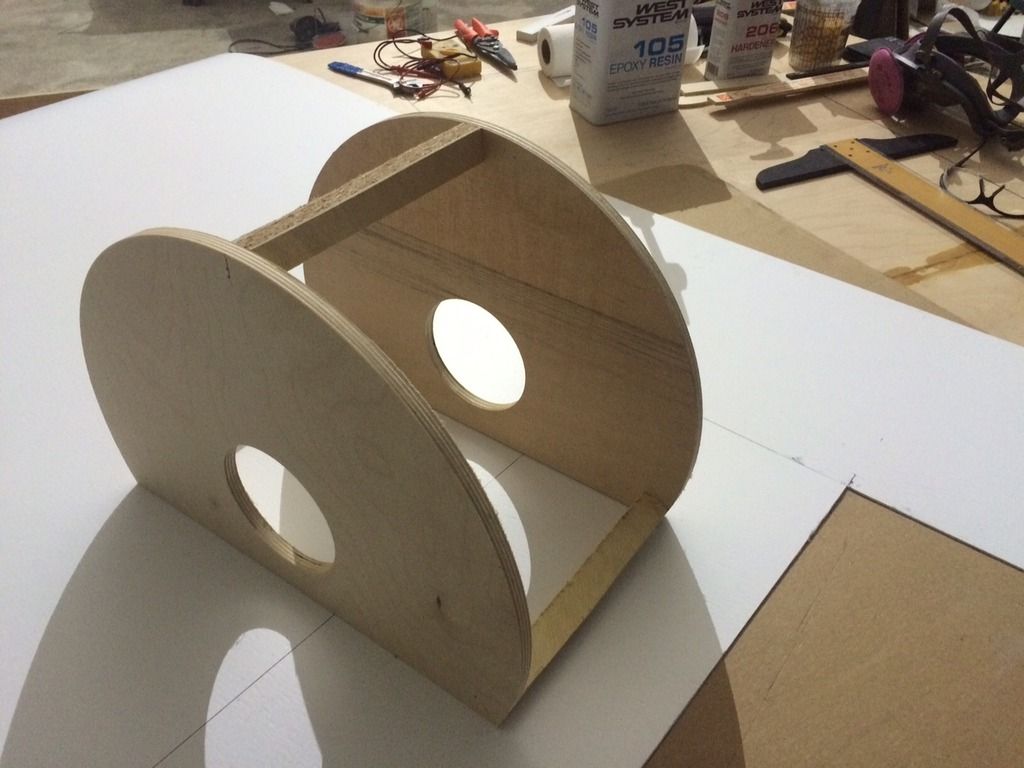
Once satisfied of the fit, we cut the next batch. Inside and concentric to the O.D., each frame has a 4.560" hole cut that is center-line positioned 3-1/2 inches off the flat bottom wing deck.

This center hole is what will perfectly align each section on a center support alignment tube that allows the 12 foot long aluminum gun barrel to slide inside and run to the rear anchor point. The support tube is a 4" I.D. schedule 80 PVC pipe. The problem is, a perfect 4" outside diameter (O.D.) aluminum tube can't fit inside of a perfect 4" inside diameter (I.D.) PVC tube. The tolerances are just too tight, and we need to be able to remove the aluminum gun barrel for transportation and repair work. The solution was to split the PVC tube down its length using the rotary saw. We pried open this cut line and glued in 1/4" wide wood shims. This opened the I.D. about .030" and made the two fits very snug, but removable. So far we have been using Gorilla clue for the foam and wood work. This is our first time using this water activated urethane glue and we are very impressed with its versatility.
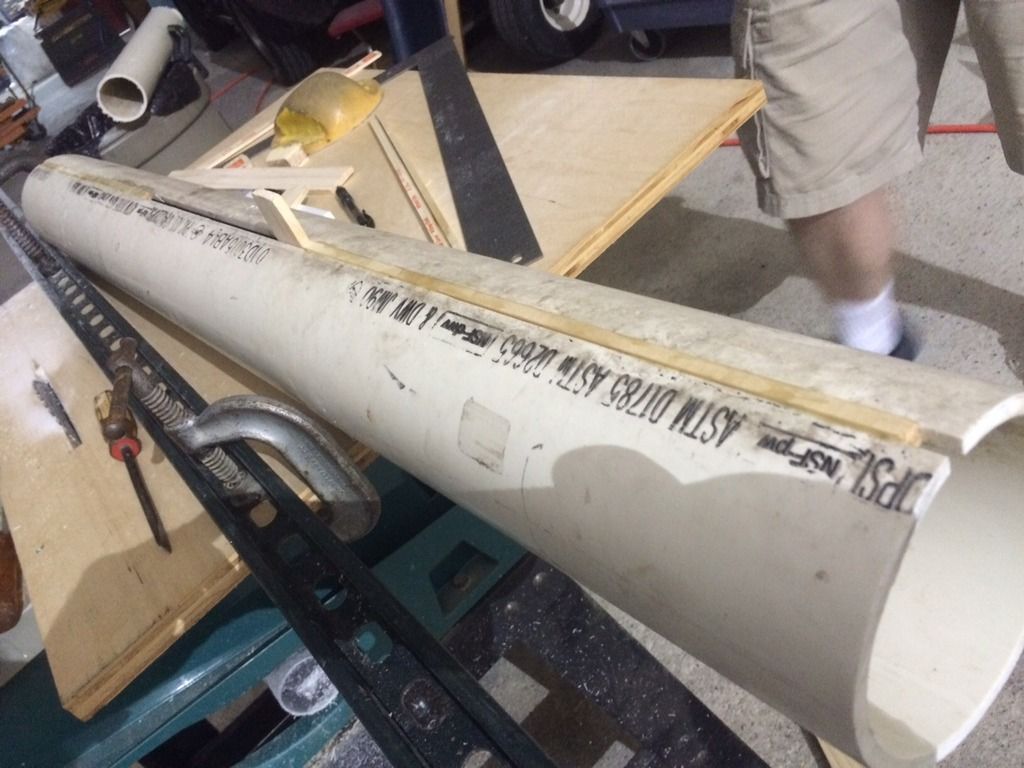
The foaming bubbles that are at the edge of the wood and the fiberglass skin is the Gorilla glue after it has activated and expanded. It's great for filling loose fitting joints or gaps in the foam support frames. After it dries, it is easily sanded or razor blade scraped off. Less expensive than epoxy, and quicker to work with since there is no measuring and mixing of A & B parts.
This is the largest drum diameter of the cannon body. 17.375" diameter by 10" long. The drum is glued into place on the PVC alignment tube. We'll start building the other diameters and assembling them the same manor. The blue tie down straps keep tension on the skin while the glue sets up over a 30 to 60 minute period.
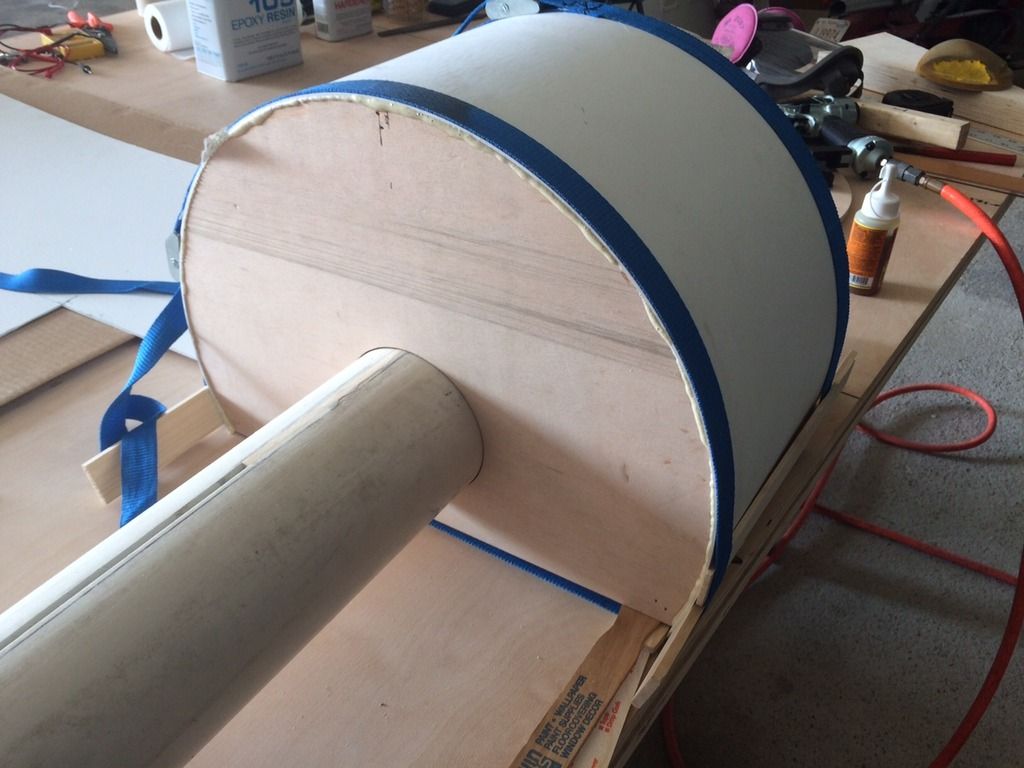
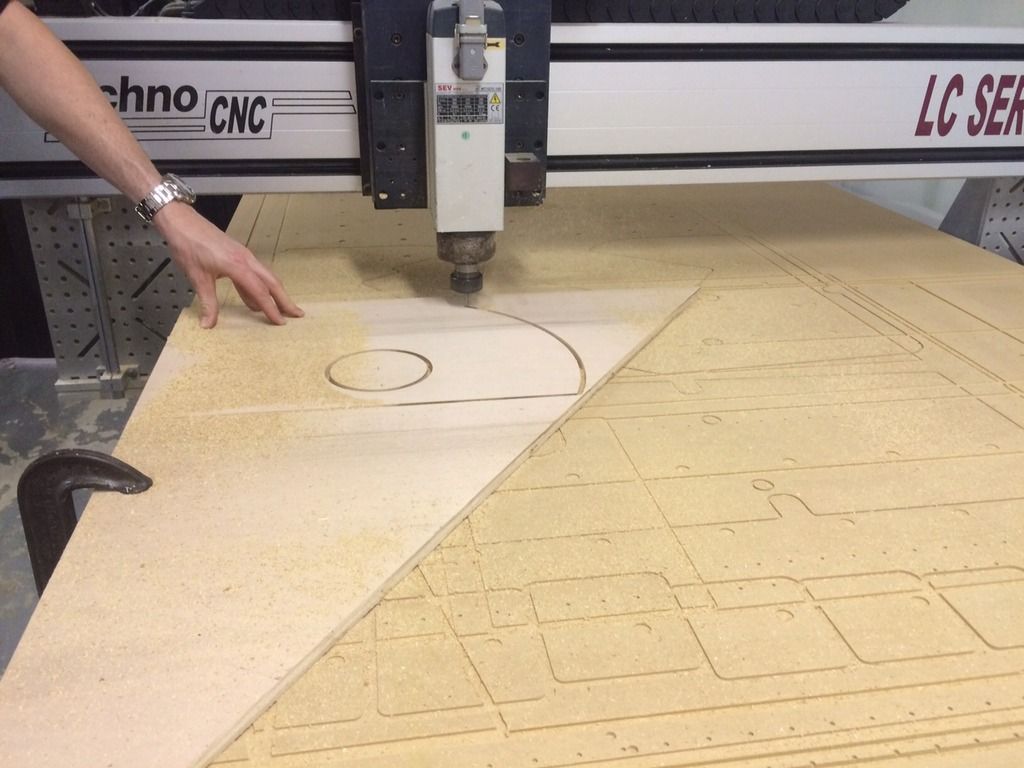
With a test front and rear frame, we glued and nailed three 9" long spacers in place. The rest of the open void will be filled in with foam to support the .090" thick fiberglass skin that will get wrapped around the frames.
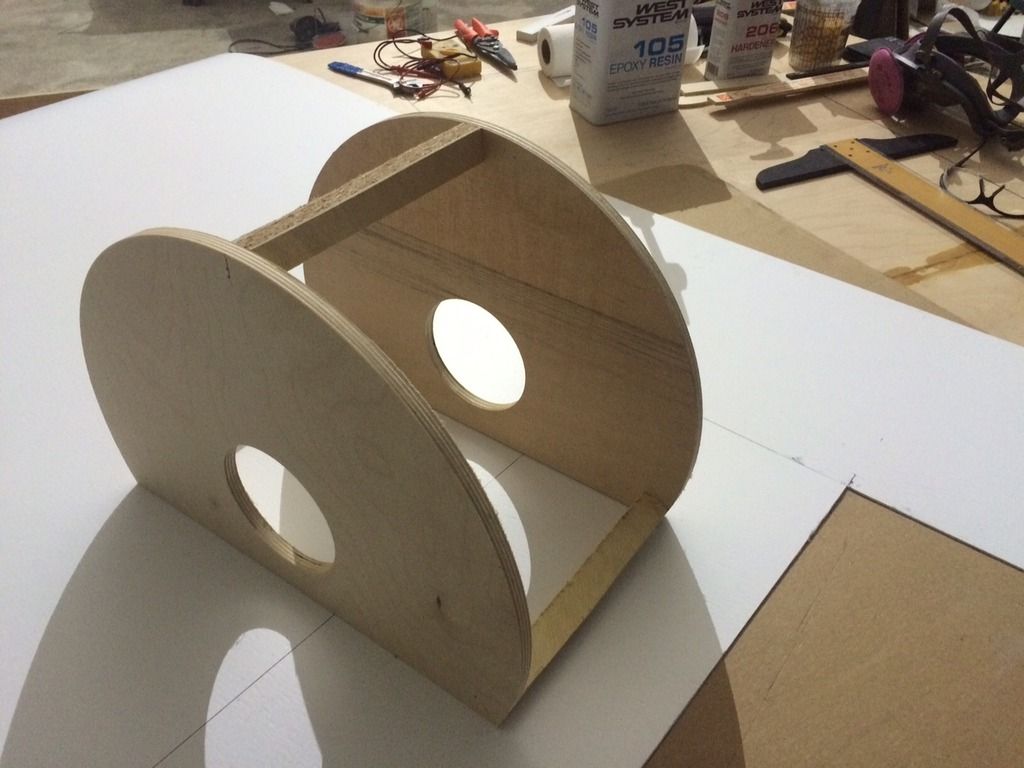
Once satisfied of the fit, we cut the next batch. Inside and concentric to the O.D., each frame has a 4.560" hole cut that is center-line positioned 3-1/2 inches off the flat bottom wing deck.

This center hole is what will perfectly align each section on a center support alignment tube that allows the 12 foot long aluminum gun barrel to slide inside and run to the rear anchor point. The support tube is a 4" I.D. schedule 80 PVC pipe. The problem is, a perfect 4" outside diameter (O.D.) aluminum tube can't fit inside of a perfect 4" inside diameter (I.D.) PVC tube. The tolerances are just too tight, and we need to be able to remove the aluminum gun barrel for transportation and repair work. The solution was to split the PVC tube down its length using the rotary saw. We pried open this cut line and glued in 1/4" wide wood shims. This opened the I.D. about .030" and made the two fits very snug, but removable. So far we have been using Gorilla clue for the foam and wood work. This is our first time using this water activated urethane glue and we are very impressed with its versatility.
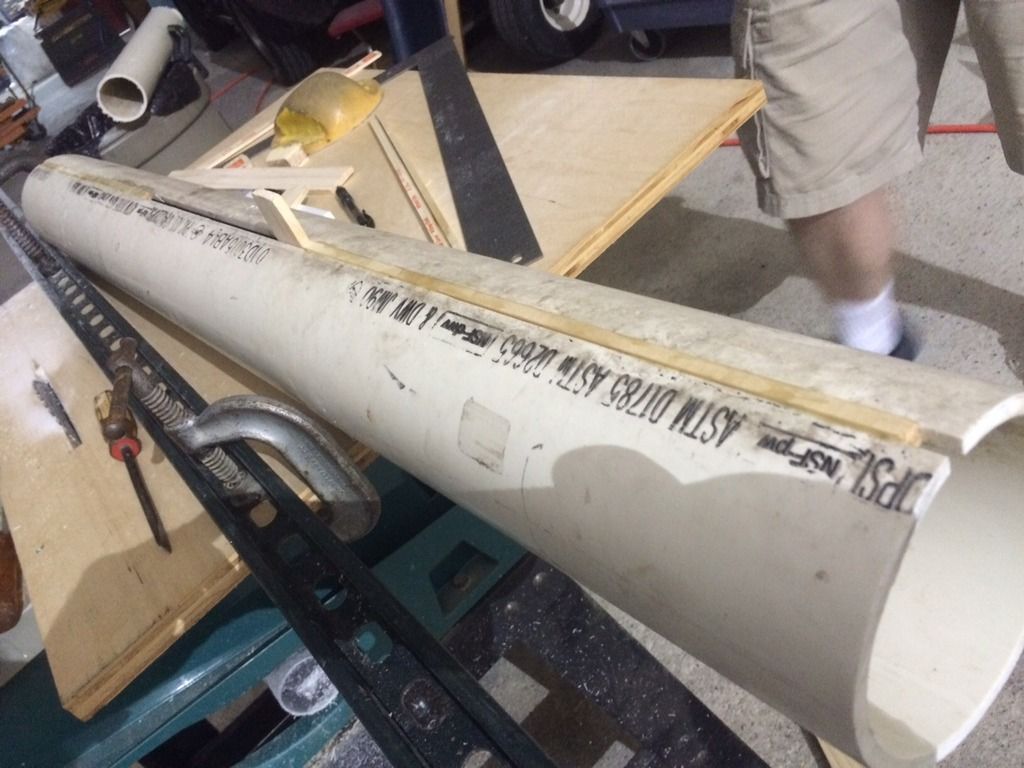
The foaming bubbles that are at the edge of the wood and the fiberglass skin is the Gorilla glue after it has activated and expanded. It's great for filling loose fitting joints or gaps in the foam support frames. After it dries, it is easily sanded or razor blade scraped off. Less expensive than epoxy, and quicker to work with since there is no measuring and mixing of A & B parts.
This is the largest drum diameter of the cannon body. 17.375" diameter by 10" long. The drum is glued into place on the PVC alignment tube. We'll start building the other diameters and assembling them the same manor. The blue tie down straps keep tension on the skin while the glue sets up over a 30 to 60 minute period.
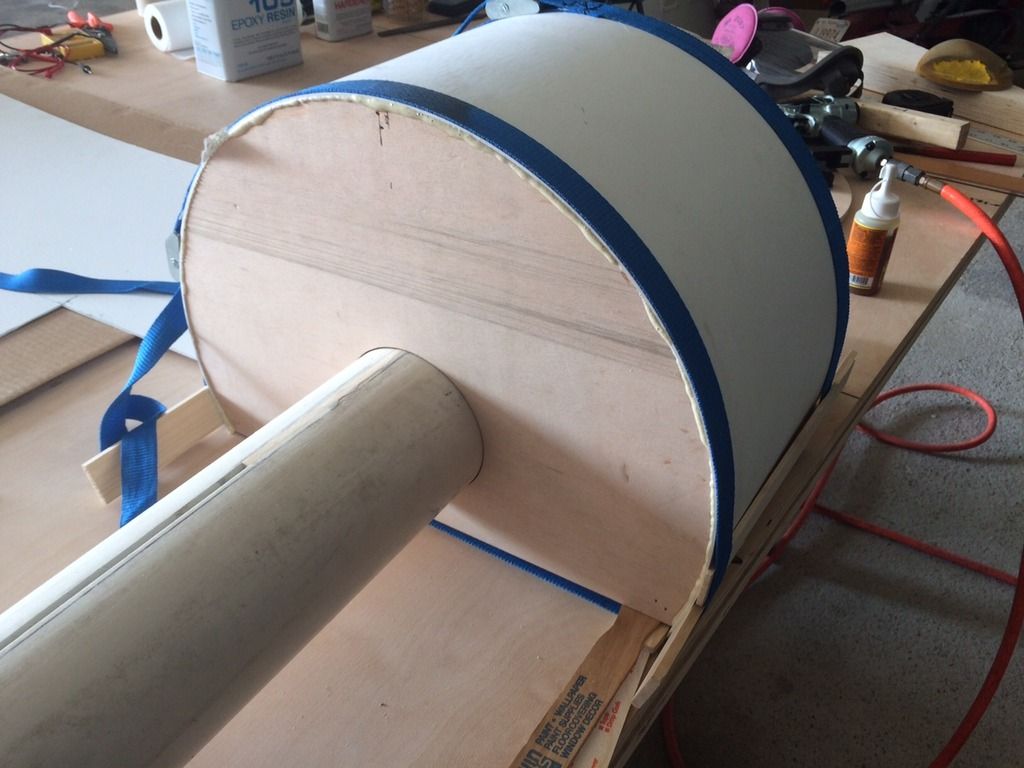
Last edited: