Sunday, April 12, 2015 - Day 9:
After church and before Sunday night dinner with the family, we were able to put in 3 hours to transfer the patterns to 12mm fine grain plywood. We stacked and fastened 4 rough cut panels together and commenced to sawing the top and bottom parallel edges on the table saw. We tried using the angel slide rail, but the 4 panels weight caused too much friction and made us afraid we'd get an uneven cut if we forced it. So we went with our proven method of sawing by hand with a set fence guide. All 4 side panels of the front pair of gun support boxes are now perfect mirror images of each other.

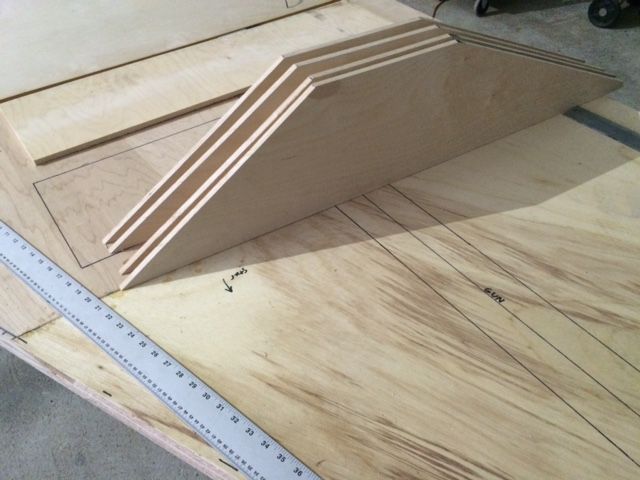
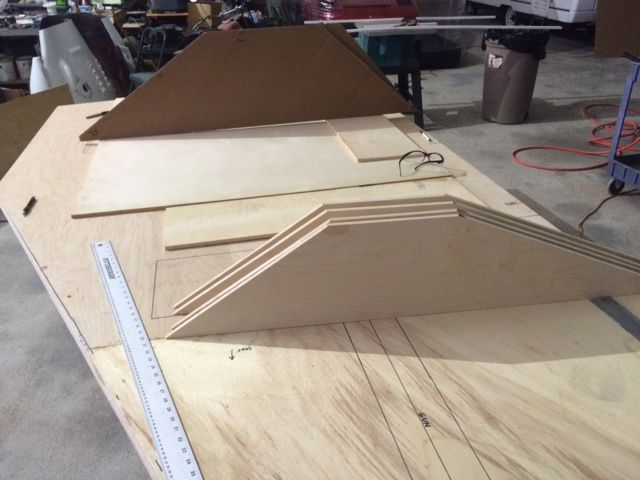
On the table saw, we cut the top 3 flat panels for each box with miter cuts for the adjoining joints. Multiple stacking rough cut panels and sawing a single time to guarantee exact copies. Tightbond III wood glue and airgun nails are holding it all together sturdily while the glue dries. We will epoxy fillet and fiberglass all of the interior joints with 4" wide 45 degree axis tape, after we have built all 4 boxes. Right now each gun-box weighs a hefty 11 pounds. These wings are well on their way to their estimated target weight of 200 pounds each. We are really creating a monster that I know we are going to regret moving around this summer. This speeder will be built like a tank and just about bullet proof. I'm seriously considering my original idea of putting a hovercraft skirt on the bottom to inflate when moving the ship around once completed.
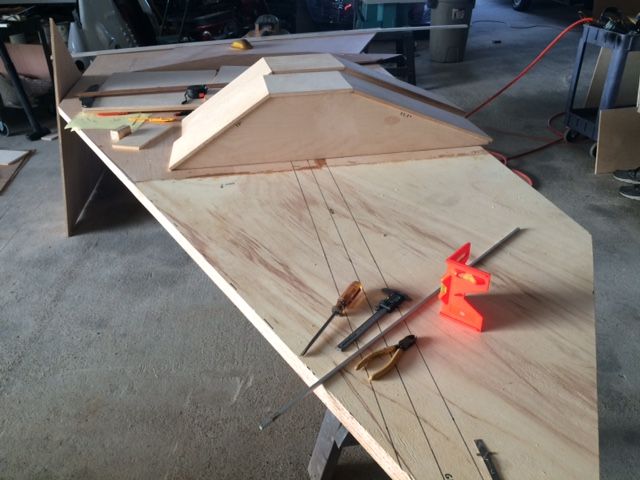
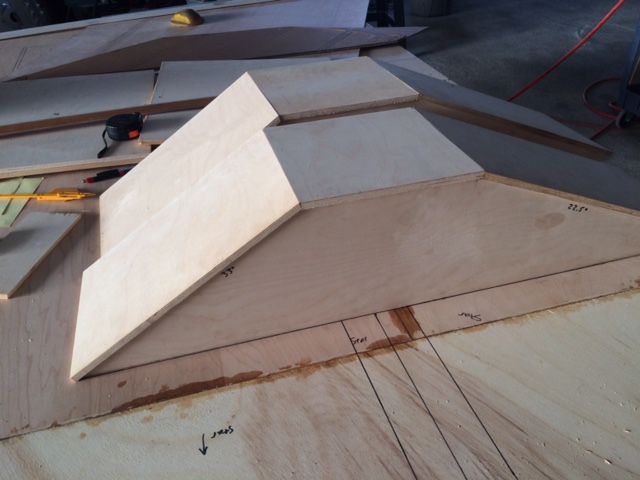
After church and before Sunday night dinner with the family, we were able to put in 3 hours to transfer the patterns to 12mm fine grain plywood. We stacked and fastened 4 rough cut panels together and commenced to sawing the top and bottom parallel edges on the table saw. We tried using the angel slide rail, but the 4 panels weight caused too much friction and made us afraid we'd get an uneven cut if we forced it. So we went with our proven method of sawing by hand with a set fence guide. All 4 side panels of the front pair of gun support boxes are now perfect mirror images of each other.

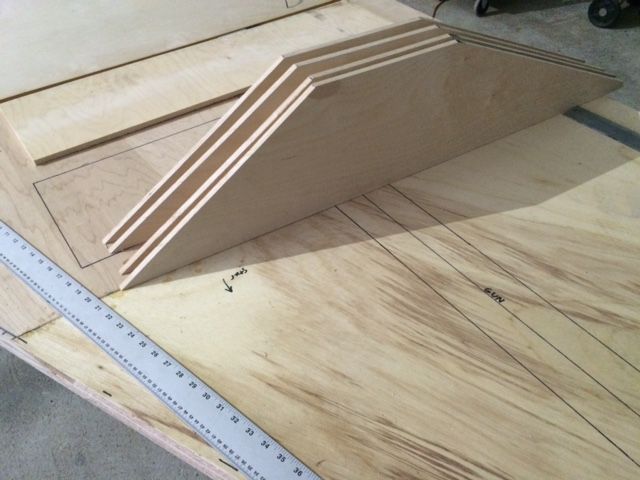
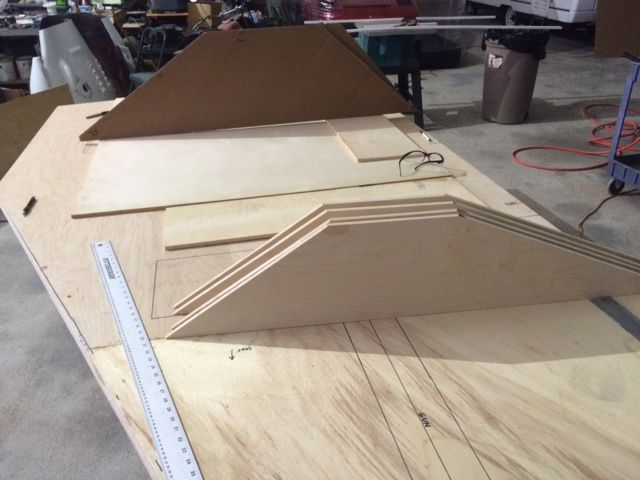
On the table saw, we cut the top 3 flat panels for each box with miter cuts for the adjoining joints. Multiple stacking rough cut panels and sawing a single time to guarantee exact copies. Tightbond III wood glue and airgun nails are holding it all together sturdily while the glue dries. We will epoxy fillet and fiberglass all of the interior joints with 4" wide 45 degree axis tape, after we have built all 4 boxes. Right now each gun-box weighs a hefty 11 pounds. These wings are well on their way to their estimated target weight of 200 pounds each. We are really creating a monster that I know we are going to regret moving around this summer. This speeder will be built like a tank and just about bullet proof. I'm seriously considering my original idea of putting a hovercraft skirt on the bottom to inflate when moving the ship around once completed.
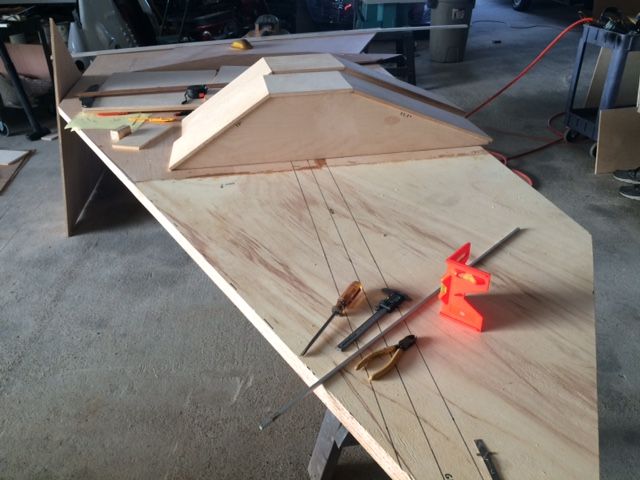
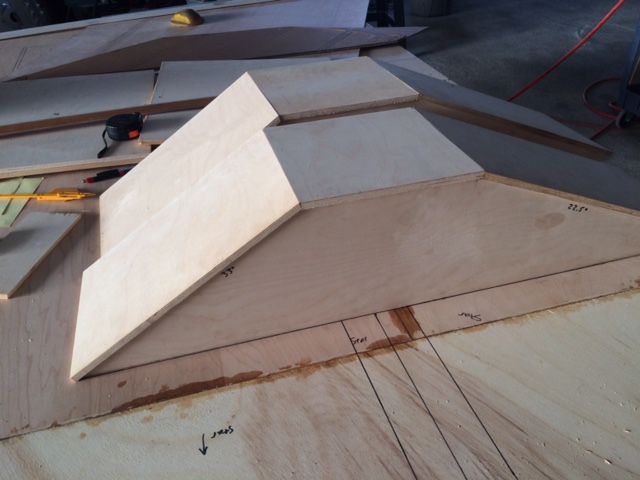
Attachments
Last edited: