Eventually, I'd like to do a Spider-Girl suit— however, the options are kind of limited on that front, so for the moment I decided to try working on the web shooters. My thoughts are to do them as bracers, using Sintra as the base, with molded plastic (such as InstaMorph) for the 'cartridge' pieces.
Since I'll have to wait for the actual supplies to arrive, I decided to play around with cardboard and card stock in the meantime, to make a mock up and work out the sizing.
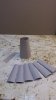
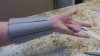
The edges (on wrist and forearm) weren't trimmed because I'm more concerned with width and spacing right now. The wider end of the cartridge pieces came out a little too wide, but otherwise I think it looks promising. Next thing I'll probably fiddle with while I'm waiting is a design for the trigger mechanism. What do you guys think?
Since I'll have to wait for the actual supplies to arrive, I decided to play around with cardboard and card stock in the meantime, to make a mock up and work out the sizing.
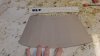
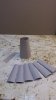
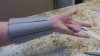
The edges (on wrist and forearm) weren't trimmed because I'm more concerned with width and spacing right now. The wider end of the cartridge pieces came out a little too wide, but otherwise I think it looks promising. Next thing I'll probably fiddle with while I'm waiting is a design for the trigger mechanism. What do you guys think?