rogue9607
Active Member
I've lurked on the board here for a while as I worked on a couple of projects and finally have one nearly-complete that I wanted to share.
Late last year when SW:TOR launched, my wife saw Satele Shan's lightsaber in the Hope trailer and immediately said "I want her saber, but with a Tiffany Blue blade!" Having never built a saber before, or worked with metal, I initially brushed it off as something crazy I'd never be able to do. However, like many things that sound crazy at first, it planted a seed and soon I found myself researching what went into building a saber. To my amazement, I found myself thinking I could actually do it!
I started with an order of aluminum tubing and sheet aluminum, and after many challenging hours, I managed to assemble a nearly-final product five hours before Celebration VI began. (a deadline I'd been telling myself I would make after having the project slip past my wife's birthday)
My wife has named this saber "Holly" (after "Holly Golightly" from "Breakfast at Tiffany's"). So, I'm proud to present... Holly!


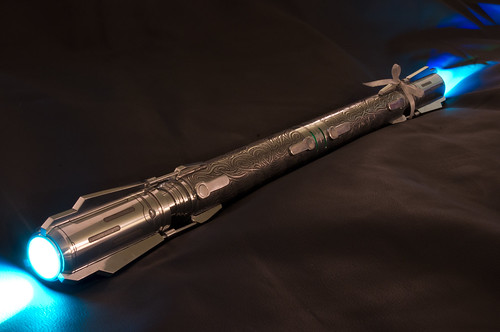
Some of the color options: Tiffany Blue, Red, Green, and Blue
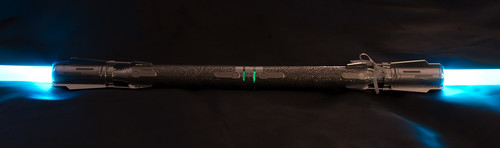
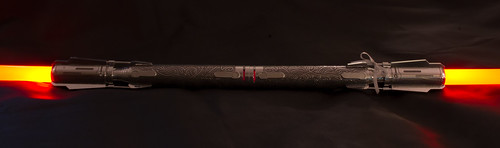
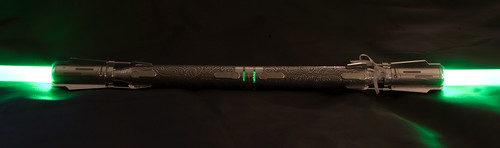
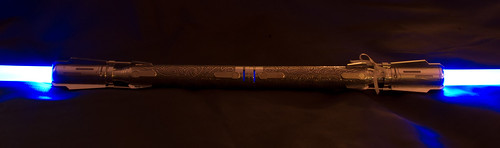
Thanks for looking!
Late last year when SW:TOR launched, my wife saw Satele Shan's lightsaber in the Hope trailer and immediately said "I want her saber, but with a Tiffany Blue blade!" Having never built a saber before, or worked with metal, I initially brushed it off as something crazy I'd never be able to do. However, like many things that sound crazy at first, it planted a seed and soon I found myself researching what went into building a saber. To my amazement, I found myself thinking I could actually do it!
I started with an order of aluminum tubing and sheet aluminum, and after many challenging hours, I managed to assemble a nearly-final product five hours before Celebration VI began. (a deadline I'd been telling myself I would make after having the project slip past my wife's birthday)
My wife has named this saber "Holly" (after "Holly Golightly" from "Breakfast at Tiffany's"). So, I'm proud to present... Holly!


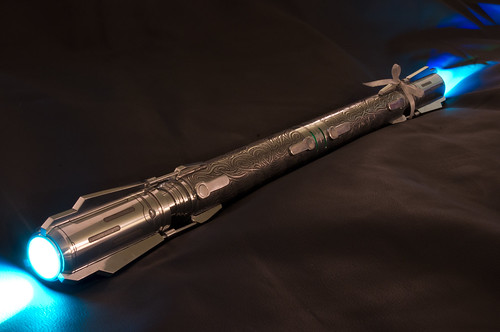
Some of the color options: Tiffany Blue, Red, Green, and Blue
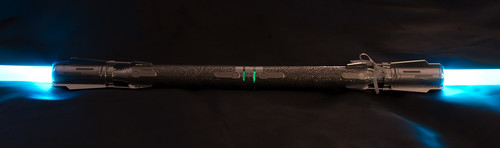
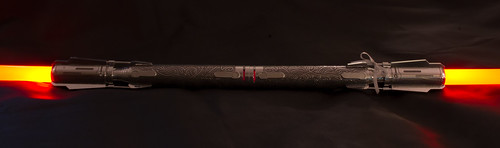
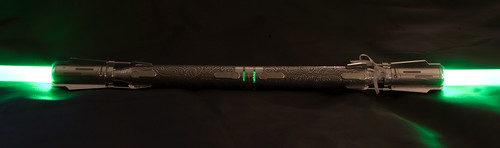
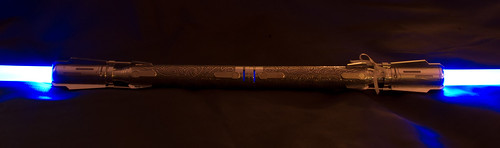
Thanks for looking!
Last edited: