SuperSnarf400
New Member
Ladies and Gentlemen,
This is my first post here on RPF but I've been lurking around for a few months. I've taken my first steps into a larger world, and decided I want to build/install my first lightsaber! I admit I probably picked a difficult one to start off with but hey it's my favorite hilt!
I currently have my hilt (beautiful) and a Rudy Pando CC (also awesome), and my next step is getting my chassis. I've settled on the ShtokCustomWorx Chassis from Shapeways, and planning on using a Proffie board.
In doing my research, I understand that the Rudy Pando has changed a little over the years. I'm fairly confident that mine is the most recent rev. If so, there should be a "speaker holder" already built into the CC, correct? If that is the case, do I still need to order the speaker holder from Shapeways (R-CC Chassis PART 4 28mm Flat Speaker Holder)?
www.shapeways.com
I don't want to order parts I don't need if I can help it, and also don't want to realize I need a part after I got everything else. I understand I need Parts 1 (which is a few pieces), 2, 3, and the Clamp Switches Holder.
Any insight is helpful. I tried looking around for the answer on RPF, so if this has already been answered my apologies. MTFBWY!
This is my first post here on RPF but I've been lurking around for a few months. I've taken my first steps into a larger world, and decided I want to build/install my first lightsaber! I admit I probably picked a difficult one to start off with but hey it's my favorite hilt!
I currently have my hilt (beautiful) and a Rudy Pando CC (also awesome), and my next step is getting my chassis. I've settled on the ShtokCustomWorx Chassis from Shapeways, and planning on using a Proffie board.
In doing my research, I understand that the Rudy Pando has changed a little over the years. I'm fairly confident that mine is the most recent rev. If so, there should be a "speaker holder" already built into the CC, correct? If that is the case, do I still need to order the speaker holder from Shapeways (R-CC Chassis PART 4 28mm Flat Speaker Holder)?
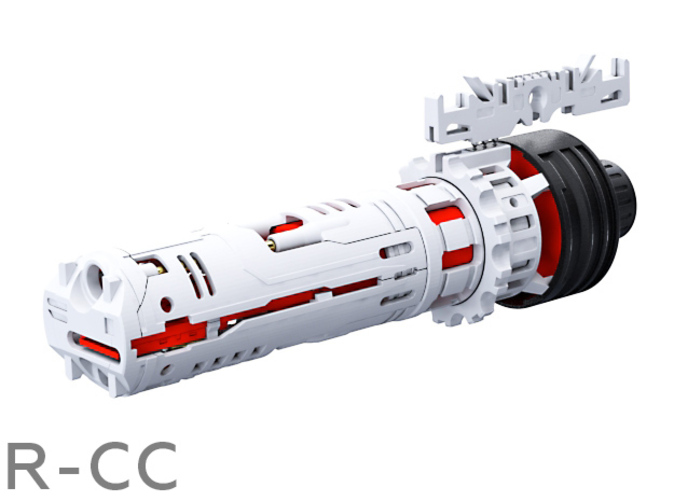
R-CC Chassis PART 4 28mm Flat Speaker Holder by ShtokCustomWorx on Shapeways
Check out R-CC Chassis PART 4 28mm Flat Speaker Holder by ShtokCustomWorx on Shapeways and discover more 3D printed products in Maker/DIY.
I don't want to order parts I don't need if I can help it, and also don't want to realize I need a part after I got everything else. I understand I need Parts 1 (which is a few pieces), 2, 3, and the Clamp Switches Holder.
Any insight is helpful. I tried looking around for the answer on RPF, so if this has already been answered my apologies. MTFBWY!