DRG
Active Member
Time to resume after vacation...
Cod
I wanted the cod to be flexible, as the cod and abs are the key to my mobility and comfort factor of my build. The technique I'm using for these flex pieces is to build the individual pieces out of thinner foam (2mm in this case) and cover them with shiny fabric using contact cement, then attach all the pieces together to form the cod. The technique I learned watching Emmabellish's great Youtube video.
The fabric I'm using is a 4 way stretch vinyl, the color was 'wine'. It matches almost perfectly to the paint in the naked eye.
Here are some of the pieces laid out on the fabric. I adapted the model a bit for this purpose, and I had to leave the front 'flap' detachable for bathroom breaks.
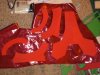
Here is work in progress (this is actually for a different piece, but the idea is the same):

Some raw pieces. Once they dry I hot glue around the inner edges, fold the flaps of fabric over the glue, and snip off the excess fabric.

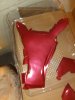
Once all the pieces were finished, I used 3mm foam to form 'joints' between the pieces on the inside (using hot glue).

Here is the opened cod. You see the front flap, which attaches to the side 'arms' via velcro. Right now the whole 'inner thigh' section is still foam/fabric. I may eventually cut away some of this and replace it with strapping for additional comfort, depending on how it ends up fitting with the thigh pieces on.

Here is the closed piece from different angles.


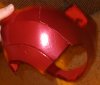
The final piece is very wearable, although the fit is weird until I get the abs completed.
I'm making the abs in a similar fashion... they will wrap around and connect at the front (sort of like a corset). The front ab 'plates' will be a separate piece that connects to the chest and covers the front of the ab wrap. The cod and ab wrap will share a common spine, and will have additional connections up front... which should help the cod stay on when I detach the front flap for bathroom breaks.
Cod
I wanted the cod to be flexible, as the cod and abs are the key to my mobility and comfort factor of my build. The technique I'm using for these flex pieces is to build the individual pieces out of thinner foam (2mm in this case) and cover them with shiny fabric using contact cement, then attach all the pieces together to form the cod. The technique I learned watching Emmabellish's great Youtube video.
The fabric I'm using is a 4 way stretch vinyl, the color was 'wine'. It matches almost perfectly to the paint in the naked eye.
Here are some of the pieces laid out on the fabric. I adapted the model a bit for this purpose, and I had to leave the front 'flap' detachable for bathroom breaks.
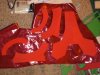
Here is work in progress (this is actually for a different piece, but the idea is the same):

Some raw pieces. Once they dry I hot glue around the inner edges, fold the flaps of fabric over the glue, and snip off the excess fabric.

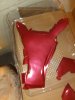
Once all the pieces were finished, I used 3mm foam to form 'joints' between the pieces on the inside (using hot glue).

Here is the opened cod. You see the front flap, which attaches to the side 'arms' via velcro. Right now the whole 'inner thigh' section is still foam/fabric. I may eventually cut away some of this and replace it with strapping for additional comfort, depending on how it ends up fitting with the thigh pieces on.

Here is the closed piece from different angles.


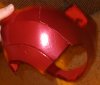
The final piece is very wearable, although the fit is weird until I get the abs completed.
I'm making the abs in a similar fashion... they will wrap around and connect at the front (sort of like a corset). The front ab 'plates' will be a separate piece that connects to the chest and covers the front of the ab wrap. The cod and ab wrap will share a common spine, and will have additional connections up front... which should help the cod stay on when I detach the front flap for bathroom breaks.