DRG
Active Member
So I'm working on a foam Mark VII armor for Halloween. But after having issues with my Gears of War build last year in terms of 'ease of wearing', I knew I needed to change things up a bit with my Iron Man.
These were my needs going in:
-----
The ability to suit up and take it off without assistance
The ability to climb stairs
The ability to pee with (relative) ease without completely de-suiting
Decent arm mobility for taking photos with my camera/posing/drinking/etc.
Faceplate that opens
Helmet that fits over my glasses
I also knew this would be a bit of a challenge, as Iron Man is a full body suit versus my Gears build... so expecting to make it *more* wearable sounds a bit crazy. To try and pull this off I'm creating what I *think* are a few new approaches, combined with many great ideas I've found in this forum.
Legs
The legs are based on JTM's original model using elements from both Gaiatron & JF Custom's foam adaptations of JTM's model.
I originally built two sets of legs, scaled for 'thickness' versus length. Well, I recently realized they were just too long. The thigh and shin and boots were all colliding into each other in a unpleasant way when I tried to walk, and trying to connect the thigh and shin with a hinge proved to be completely unworkable (it would have pushed the bottom of the shin about four inches below my foot).
My goal here was to make all the leg pieces individually attachable/detachable without having to remove the boots or any other pieces. I realized with my first set of shins that I had a difficult time attaching the velcro on the boots while the shin was on. So ideally I want to be suiting up my lower body in this order: boots-shins-cod-thighs.
So my solution was to create splits on the inner seams of each piece where they won't be as noticeable. In the thigh this was fairly easy to pull off.


But the shins didn't lend themselves to an obvious straight seam anywhere, especially if I wanted to retain the shape. So I created a weird L-shaped seam as such.


The bonus with this approach is that the shins fit like a glove. I'm saving the knees and shin flaps for later as I have a few ideas I want to try with those.

Also, I didn't line the velcro up perfectly in these pics. The velcro was starting to detach from the foam in a few spots when I took these pics so I didn't want to monkey around with it too much. I had to reglue these with a stronger glue after I took the pics. But it does line up fairly nicely if I get it right, to the point where the seams are barely noticeable.
A few more:

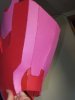
These were my needs going in:
-----
The ability to suit up and take it off without assistance
The ability to climb stairs
The ability to pee with (relative) ease without completely de-suiting
Decent arm mobility for taking photos with my camera/posing/drinking/etc.
Faceplate that opens
Helmet that fits over my glasses
I also knew this would be a bit of a challenge, as Iron Man is a full body suit versus my Gears build... so expecting to make it *more* wearable sounds a bit crazy. To try and pull this off I'm creating what I *think* are a few new approaches, combined with many great ideas I've found in this forum.
Legs
The legs are based on JTM's original model using elements from both Gaiatron & JF Custom's foam adaptations of JTM's model.
I originally built two sets of legs, scaled for 'thickness' versus length. Well, I recently realized they were just too long. The thigh and shin and boots were all colliding into each other in a unpleasant way when I tried to walk, and trying to connect the thigh and shin with a hinge proved to be completely unworkable (it would have pushed the bottom of the shin about four inches below my foot).
My goal here was to make all the leg pieces individually attachable/detachable without having to remove the boots or any other pieces. I realized with my first set of shins that I had a difficult time attaching the velcro on the boots while the shin was on. So ideally I want to be suiting up my lower body in this order: boots-shins-cod-thighs.
So my solution was to create splits on the inner seams of each piece where they won't be as noticeable. In the thigh this was fairly easy to pull off.


But the shins didn't lend themselves to an obvious straight seam anywhere, especially if I wanted to retain the shape. So I created a weird L-shaped seam as such.


The bonus with this approach is that the shins fit like a glove. I'm saving the knees and shin flaps for later as I have a few ideas I want to try with those.

Also, I didn't line the velcro up perfectly in these pics. The velcro was starting to detach from the foam in a few spots when I took these pics so I didn't want to monkey around with it too much. I had to reglue these with a stronger glue after I took the pics. But it does line up fairly nicely if I get it right, to the point where the seams are barely noticeable.
A few more:

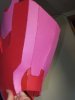