these are the handle parts of my fifth element glove/hand kit, probably the biggest reason for not redoing the kit before now was the casting up of these parts which i found to be a complete PITA.
the main issue is the amount of ridges and corners to trap air.
so before i start to mold these parts up again and go through the slog of trying to get decent casts how would you do it?
there is no other equipment apart from a pair of hands, fast cast resin and some silicone.
please help to make my molding / casting life a bit easier :thumbsup
-z
the main issue is the amount of ridges and corners to trap air.
so before i start to mold these parts up again and go through the slog of trying to get decent casts how would you do it?
there is no other equipment apart from a pair of hands, fast cast resin and some silicone.
please help to make my molding / casting life a bit easier :thumbsup

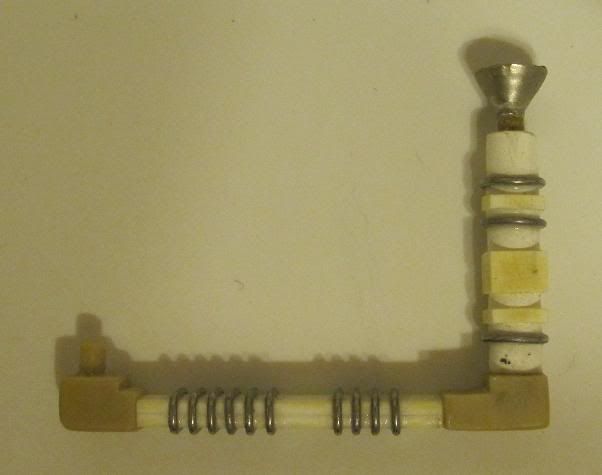
-z