reaton89
Active Member
My name is Ryan, and I've been sculpting in my free time for couple of years. I spend a lot of time lurking on sites like the RPF, trying to soak up the information that's available. There are a ton of talented artists out there sharing their techniques so people like me (who have no idea what they're doing) can figure this stuff out. So to show my appreciation for the great (free) education, I'm paying it forward.
I haven't seen many V masks that weren't mass-produced, so I gave it a shot. I wanted to capture the squinty eyes, the pointy chin, and make the overall size slightly smaller than the ones sold in Halloween stores. I also wanted to do a half mask for my first mold and cast. That way if I screwed it up, I wouldn't have wasted as much material.
10 or 15 hours in. I sculpted this over another project that I wasn't happy with, but I should have started on a horizontal plane.
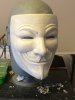
So, face/off... I'll get the hang of it.
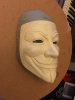
Final sculpt (around 40-50 hours). I built a retaining base to conserve molding materials, and to make slush-casting a bit more efficient.
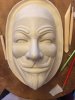
Decided to add some keys to keep the mother mold in place.

Clear-coated with acrylic. Molding station ready to go.
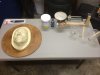
First coat of Smooth-On Mold Max XLSII
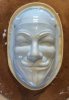
Third coat. I added some Thi-Vex to the 2nd and 3rd coats, and 3 seemed sufficient. Next time, I'll add additional keys to the silicone because the clay keys were almost completely lost in the silicone.
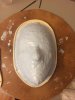
Applying the plaster bandage mother mold. I did three layers, going opposite directions on each layer. Then I added an ovular band around the base for reinforcement.
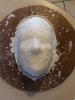
The mold came off clean! For someone who has never done this before, seeing the negative mold was a huge checkpoint. I sprayed some Ease Release 200 before casting.
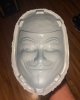
First coat of Smooth Cast 65d. I did a total of 4, but I used small quantities in thin layers. I learned slush-casting is an art form in itself, and very time-sensitive.
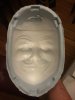
The first pull
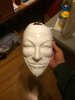
2 more, and started trimming the holes and edges. Castings were better each time.
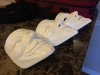
Here's a comparison shot with the "collector's edition" mask.
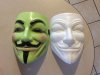
Now I just have to get painting supplies and learn how to use them... Here we go again...
Thanks for looking!
-Ryan
I haven't seen many V masks that weren't mass-produced, so I gave it a shot. I wanted to capture the squinty eyes, the pointy chin, and make the overall size slightly smaller than the ones sold in Halloween stores. I also wanted to do a half mask for my first mold and cast. That way if I screwed it up, I wouldn't have wasted as much material.
10 or 15 hours in. I sculpted this over another project that I wasn't happy with, but I should have started on a horizontal plane.
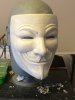
So, face/off... I'll get the hang of it.
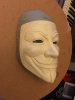
Final sculpt (around 40-50 hours). I built a retaining base to conserve molding materials, and to make slush-casting a bit more efficient.
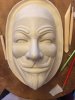
Decided to add some keys to keep the mother mold in place.

Clear-coated with acrylic. Molding station ready to go.
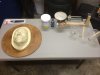
First coat of Smooth-On Mold Max XLSII
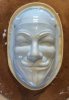
Third coat. I added some Thi-Vex to the 2nd and 3rd coats, and 3 seemed sufficient. Next time, I'll add additional keys to the silicone because the clay keys were almost completely lost in the silicone.
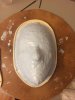
Applying the plaster bandage mother mold. I did three layers, going opposite directions on each layer. Then I added an ovular band around the base for reinforcement.
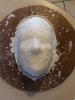
The mold came off clean! For someone who has never done this before, seeing the negative mold was a huge checkpoint. I sprayed some Ease Release 200 before casting.
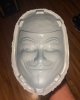
First coat of Smooth Cast 65d. I did a total of 4, but I used small quantities in thin layers. I learned slush-casting is an art form in itself, and very time-sensitive.
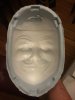
The first pull
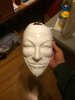
2 more, and started trimming the holes and edges. Castings were better each time.
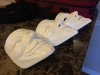
Here's a comparison shot with the "collector's edition" mask.
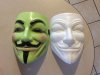
Now I just have to get painting supplies and learn how to use them... Here we go again...
Thanks for looking!
-Ryan