onewithnopaper
New Member
This is my first foray into posting a chronicle of a sculpt, so please correct me if I make any posting faux pas. (EDIT: reposted here, the correct forum. After my initial mis-posting)
I've been working on this model on and off for the past month or so. I'm completely new to a bunch of the materials and processes I'm using, so I'm certain to have made -and continue to make- mistakes. There's few photos of parts of the build. I kept forgetting to document, since it's not something I've ever done before.
On with the progress so far!
Hope you enjoy.
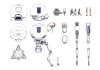
I started out with drawing up some rough plans for the model. Well, initially I just wanted a technical drawing of a Mr Handy, but during the process of gathering reference I slowly decided to build a model too.
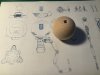
I found a 50mm wooden ball as a base to work from. I didn't trust my sculpey skills to make a perfect sphere, and this was roughly the right size. My guesstimations make Mr Handy floating at about 150cm, so this makes the scale about 1/8th.
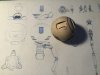
I used a dremel to cut into the wood where needed. Turns out those things are pretty tough.
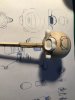
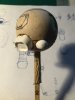
I sculpted the vents and stabilisers from primo sculpey, which I do not have much experience with. This is only my second project using it, and it's a bit softer than I'd like before cooking. It does the job, though, and takes a really nice finish. The extra bits were baked and stuck to the body with epoxy.
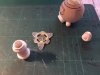
The main thruster and camera/eye were made from the same sculpey. The support ring/waist is mostly clear styrene I had left over from another project, and a little bit of epoxy putty for some of the curves.
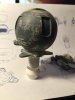
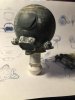
The main stack isn't glued yet here, just press fitting some pins and sockets from epoxy. Priming and sanding on the main body has begun. The interior of the eye cutaways is filled with epoxy putty to cover the dremel gouges. Mr Handy has much more interior detail (the concept art is amazing reference for this), and I did start sculpting some of those. It just didn't look right, however, so I tried again with some kitbashing, which also didn't look great. In the end I decided to leave it smooth so as not to distract from the exterior details. Since I'm planning on roto-casting the main body in resin, I can always add an entire naked Mr Handy core inside later.
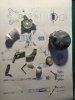
I entirely forgot to document the process of making the legs and hand attachments. They're entirely sculpey and styrene, though. A good portion of the round parts are made from scavenged model kit sprues, including the joint details.
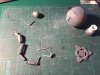
All the parts laid out just before the final prime, sand and finish.
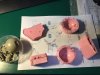
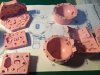
Once all the parts had a nice finish, I made some silicone moulds. Not only was this my first time using silicone, it was my first time making a mould at all. I thought this would be easier than making three identical sets of camera/eyes and legs, and if I were moulding them I may as well make a full set. Perhaps I will generate my own Mr Handy army.
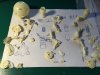
Along with my first time using silicone, or moulding anything, this is my first time working with resin. So these are the mistakes. The set on the left was the first attempt. Not a single usable part came out, but I did kinda expect that. For the middle set I cut some air channels, widened the pour gates and got my timing and angles a bit better. One or two usable pieces came out of that set. On the right is the set I just pulled a few hours ago after cutting more air channels. Again, there are a lot of bubble and blockage problems, but its definitely improving. The resin I'm using has a very short pot-life, only about 2 minutes before it has gelled too much to flow through the thinner parts. It may have been an unwise beginner casting project to choose something with so many tiny details. The advantage, I guess, is that I'm not wasting much resin with each failed attempt.
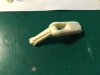
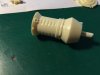
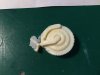
I do have a few usable parts with just a few bubbles to fill and a little flashing to trim. All is not lost.
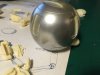
The one success so far is the second rotocast of the body. I couldn't wait to get a glimpse of the final model. Perhaps to counter the repeated failures of the tiny parts. Without even priming or prepping the surface in any way (I didn't even clean it) I slapped some rub'nbuff on the front. It makes me feel much more hopeful.
That's where I am so far!
I've ordered more silicone, since I was just playing with a 250gm sample kit. I'll need to remake at least one of the moulds. I ripped the waist mould while separating the second part from the master. Obviously I missed a spot with the release. It was just unlucky it was at a detail critical spot otherwise it might be repairable. I might remake a few others to deal with bubbles and blockages a since now I'm a tiny bit wiser. The stuff is expensive, though. I expect I'll want to play with it more for other projects anyway.
Thanks for reading through all of my many and varied ineptitudes.
More to come as the situation develops...
I've been working on this model on and off for the past month or so. I'm completely new to a bunch of the materials and processes I'm using, so I'm certain to have made -and continue to make- mistakes. There's few photos of parts of the build. I kept forgetting to document, since it's not something I've ever done before.
On with the progress so far!
Hope you enjoy.
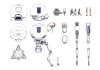
I started out with drawing up some rough plans for the model. Well, initially I just wanted a technical drawing of a Mr Handy, but during the process of gathering reference I slowly decided to build a model too.
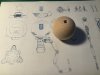
I found a 50mm wooden ball as a base to work from. I didn't trust my sculpey skills to make a perfect sphere, and this was roughly the right size. My guesstimations make Mr Handy floating at about 150cm, so this makes the scale about 1/8th.
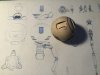
I used a dremel to cut into the wood where needed. Turns out those things are pretty tough.
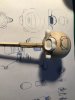
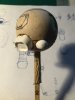
I sculpted the vents and stabilisers from primo sculpey, which I do not have much experience with. This is only my second project using it, and it's a bit softer than I'd like before cooking. It does the job, though, and takes a really nice finish. The extra bits were baked and stuck to the body with epoxy.
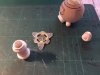
The main thruster and camera/eye were made from the same sculpey. The support ring/waist is mostly clear styrene I had left over from another project, and a little bit of epoxy putty for some of the curves.
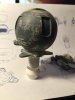
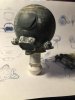
The main stack isn't glued yet here, just press fitting some pins and sockets from epoxy. Priming and sanding on the main body has begun. The interior of the eye cutaways is filled with epoxy putty to cover the dremel gouges. Mr Handy has much more interior detail (the concept art is amazing reference for this), and I did start sculpting some of those. It just didn't look right, however, so I tried again with some kitbashing, which also didn't look great. In the end I decided to leave it smooth so as not to distract from the exterior details. Since I'm planning on roto-casting the main body in resin, I can always add an entire naked Mr Handy core inside later.
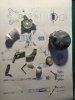
I entirely forgot to document the process of making the legs and hand attachments. They're entirely sculpey and styrene, though. A good portion of the round parts are made from scavenged model kit sprues, including the joint details.
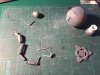
All the parts laid out just before the final prime, sand and finish.
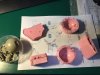
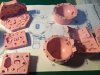
Once all the parts had a nice finish, I made some silicone moulds. Not only was this my first time using silicone, it was my first time making a mould at all. I thought this would be easier than making three identical sets of camera/eyes and legs, and if I were moulding them I may as well make a full set. Perhaps I will generate my own Mr Handy army.
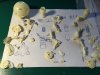
Along with my first time using silicone, or moulding anything, this is my first time working with resin. So these are the mistakes. The set on the left was the first attempt. Not a single usable part came out, but I did kinda expect that. For the middle set I cut some air channels, widened the pour gates and got my timing and angles a bit better. One or two usable pieces came out of that set. On the right is the set I just pulled a few hours ago after cutting more air channels. Again, there are a lot of bubble and blockage problems, but its definitely improving. The resin I'm using has a very short pot-life, only about 2 minutes before it has gelled too much to flow through the thinner parts. It may have been an unwise beginner casting project to choose something with so many tiny details. The advantage, I guess, is that I'm not wasting much resin with each failed attempt.
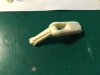
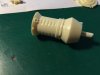
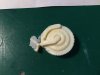
I do have a few usable parts with just a few bubbles to fill and a little flashing to trim. All is not lost.
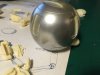
The one success so far is the second rotocast of the body. I couldn't wait to get a glimpse of the final model. Perhaps to counter the repeated failures of the tiny parts. Without even priming or prepping the surface in any way (I didn't even clean it) I slapped some rub'nbuff on the front. It makes me feel much more hopeful.
That's where I am so far!
I've ordered more silicone, since I was just playing with a 250gm sample kit. I'll need to remake at least one of the moulds. I ripped the waist mould while separating the second part from the master. Obviously I missed a spot with the release. It was just unlucky it was at a detail critical spot otherwise it might be repairable. I might remake a few others to deal with bubbles and blockages a since now I'm a tiny bit wiser. The stuff is expensive, though. I expect I'll want to play with it more for other projects anyway.
Thanks for reading through all of my many and varied ineptitudes.
More to come as the situation develops...
Last edited: