Reference photos:
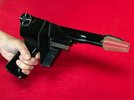
(Screen used from "The Golden Man" episode.)
(Used briefly in Battlestar Galactica)
Here's the kit:
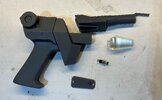
While waiting on my other Buck Rogers blaster to dry, I figured I would start work on this one.
I went through a bunch of reference photos but unfortunately, I couldn't find a good one of Gil Gerard holding this particular prop, so I'll have to go through my Blu-Rays. From what I've seen of the other versions, I think this one is my favorite. Oddly enough, it was used briefly in Battlestar Galactica, probably by a security guard or "bad guy".
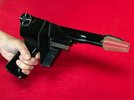
(Screen used from "The Golden Man" episode.)
(Used briefly in Battlestar Galactica)
Here's the kit:
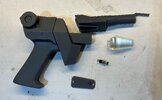
While waiting on my other Buck Rogers blaster to dry, I figured I would start work on this one.
I went through a bunch of reference photos but unfortunately, I couldn't find a good one of Gil Gerard holding this particular prop, so I'll have to go through my Blu-Rays. From what I've seen of the other versions, I think this one is my favorite. Oddly enough, it was used briefly in Battlestar Galactica, probably by a security guard or "bad guy".
Last edited: