This is another one of those projects that I had to put a hold on due to all of the events surrounding the SW prequel films, not to mention a host of other prop projects which included a Viper Pilot helmet.
I picked up this Cylon helmet around 2001 right here on the rpf. The member selling these had an original stunt helmet which he had molded and then did fiberglass pulls from. If memory serves, it was a short run that was only done once, so I jumped on it not really knowing what I was getting into. After about 20 years inside a box, sitting in the garage, the fiberglass smell finally went away.
When I finally had a chance to setup an office in my current residence, I was able to take the helmet out and display it with some other BSG goodies:
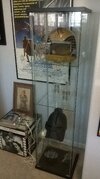
The first thing I did a few years ago was get it cleaned up. I started with a Dremel and some fiberglass wheel attachments, then moved on to a lot of sanding. Here's how it looked afterward:
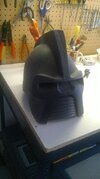
Because a two part mold was used, there was a good size molding line right across both sides of the helmet, so this required a good deal of clean up:
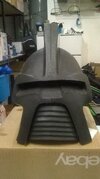
One the inside, the visor area needed some clean up:
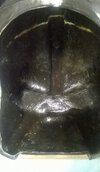
At some point I washed the helmet in soapy water and let it dry.
Later I did a little putty and sanding in specific areas:
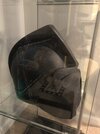
I picked up this Cylon helmet around 2001 right here on the rpf. The member selling these had an original stunt helmet which he had molded and then did fiberglass pulls from. If memory serves, it was a short run that was only done once, so I jumped on it not really knowing what I was getting into. After about 20 years inside a box, sitting in the garage, the fiberglass smell finally went away.
When I finally had a chance to setup an office in my current residence, I was able to take the helmet out and display it with some other BSG goodies:
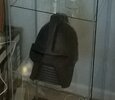
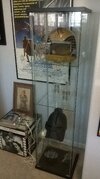
The first thing I did a few years ago was get it cleaned up. I started with a Dremel and some fiberglass wheel attachments, then moved on to a lot of sanding. Here's how it looked afterward:
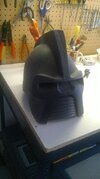
Because a two part mold was used, there was a good size molding line right across both sides of the helmet, so this required a good deal of clean up:
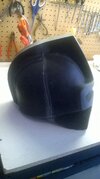
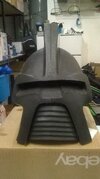
One the inside, the visor area needed some clean up:
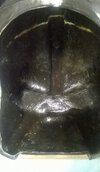
At some point I washed the helmet in soapy water and let it dry.
Later I did a little putty and sanding in specific areas:
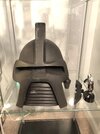
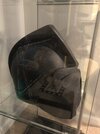
Last edited: