Daegurth
New Member
This project has been a while in the works- I collected the reference back in April, but due to other project commitments, shop reorganisation, material acquisition, etc. I didn't actually start until October. I'm now getting close enough to finishing up at a reasonable level of quality to start thinking about actually showing it! Unfortunately, I've been more focused on getting it done than recording every step (unusual for me!) so there are definitely missing parts here and there. On the other hand, I'm planning on a second build because I already have most of the materials still around to do it, which will get more thoroughly recorded. Anyway, on with the show.
First up, the design phase, back in April/May:
First thing to do was gather all the reference I could find; on the RPF, by personally screenshotting video, buying the Visual Dictionary, etc, and build a folder to work from for both direct reference and scaling:
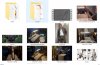
Then I used the best angles as direct 3D build reference as a camera background image in Blender. Not much worrying about scaling, just make sure it's proportional to itself for now:
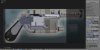
(I deleted the original camera, apparently, but you get the idea). The important aspects here were to try to match the lens distortions and camera angles as closely as possible. Then, once I built it (and providing I paid attention to parallax, perspective obscuring, etc), it would naturally straighten itself out as soon as I exited the camera. Theoretically.
Once that was done, I had to try to scale the thing before I could use it. I tried playing around doing this kind of thing...
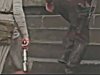
...But in the end what sold it was that if you assume the builder, having the laziness (err... Efficiency?
) inherent to industry professionals rather than the obsessiveness of fans, just buffed up some 30mm pipe for the barrel and used M3 security Torx machine screws, the scale all fell into place on its own. Length came out at 278mm, a number pretty close to what I'd heard thrown around online and seemed much more reasonable for a female hand than the ~320mm range that I'd also been seeing.
So, in the end, I had my model at what I was assuming was the correct size:
https://www.instagram.com/p/BEgQhyrNkHi/?taken-by=robtaylorcase (video, won't embed for me here)
Then it was simply a case of cranking through every part and rebuilding it parametrically, then blueprinting it, in Fusion 360:
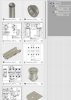
Why blueprinting? Well, a) I don't have any CNC machining capability, this whole project is manual, and b) I've been planning on putting together the blueprints into a collection, with build notes, into an eBook once I'm done. So it can be made by anyone in any material at roughly a similar accuracy level. So I'm making notes and adjustments as I go along:
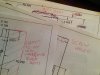
Quite the project already, but at last, I could print out a grip in 1:1 scale and test the sizing...
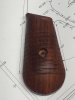
...Perfect! Now begins the real work.
First up, the design phase, back in April/May:
First thing to do was gather all the reference I could find; on the RPF, by personally screenshotting video, buying the Visual Dictionary, etc, and build a folder to work from for both direct reference and scaling:
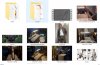
Then I used the best angles as direct 3D build reference as a camera background image in Blender. Not much worrying about scaling, just make sure it's proportional to itself for now:
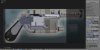
(I deleted the original camera, apparently, but you get the idea). The important aspects here were to try to match the lens distortions and camera angles as closely as possible. Then, once I built it (and providing I paid attention to parallax, perspective obscuring, etc), it would naturally straighten itself out as soon as I exited the camera. Theoretically.
Once that was done, I had to try to scale the thing before I could use it. I tried playing around doing this kind of thing...
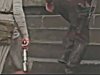
...But in the end what sold it was that if you assume the builder, having the laziness (err... Efficiency?
So, in the end, I had my model at what I was assuming was the correct size:
https://www.instagram.com/p/BEgQhyrNkHi/?taken-by=robtaylorcase (video, won't embed for me here)
Then it was simply a case of cranking through every part and rebuilding it parametrically, then blueprinting it, in Fusion 360:
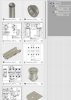
Why blueprinting? Well, a) I don't have any CNC machining capability, this whole project is manual, and b) I've been planning on putting together the blueprints into a collection, with build notes, into an eBook once I'm done. So it can be made by anyone in any material at roughly a similar accuracy level. So I'm making notes and adjustments as I go along:
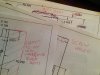
Quite the project already, but at last, I could print out a grip in 1:1 scale and test the sizing...
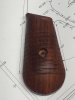
...Perfect! Now begins the real work.