Re: John Long Phaser 1 Kit Buildup plus MM P2 Restoration
So now we bend the brass. You do it just like the little old Cuban in the cigar shop.
What?
You're NOT Cuban? Crap.
OK, first of all, **** you for not being Cuban. Seriously. There's only maybe 11 million of us, so you're not helping by being something else.
Anyway, roll it up like... no... that only works if you remember the 80s... um... AHA! Like a newspaper you're going to swat a fly with. Nice and tight, because that fly is really pissing you off and you want him to know it. Just a minute to roll it full of your holy wrath, and 157 misses before you give up and get the spray.
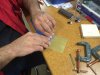
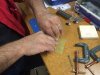
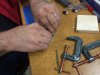
You have to do it in one continuous effort, keep the wood form pressed hard against the table, and roll. Then clamp the unholy crap out of it.
It'll need to stay like this for as long as possible, but as always I have lots to work on while I wait for a process. Sitting and waiting is very annoying, and I like to keep moving when I'm in the shop. In the industry, whether you're in a shop or on set, sitting around and waiting is only permissible when there is literally nothing for you to do. And if you're a PA, you'd better make you some worky-worky riki-tik, lest the AD spear you and mount you in his butterfly collection. So I got conditioned to work hard, fast, and smart at an early age.
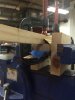
See that edge sticking up? That's the 1/4" of extra slop laughing at me. And after all I've done for it. *******.
I trimmed some of that off with a bench metal shear (DO NOT use tin snips for this --
you have been warned!!), and I may be able to trim it all the way down, in which case I'll still use this piece - apart from the slop, it came out great.
The other issue is, even though it's only 0.010" thick (and MUCH easier to bend than even 0.015, trust me), I may want to anneal it. If I mess that up (I've never annealed anything this size before), I'm going to have to start over.
Here's a video on annealing. Brass is very, very springy. Springier than spring steel, and that even has the word "spring" right in the name. So when you want to bend it, it fights back. If you're curling it around a form, it fights back even worse. So you grab a blowtorch and heat it till it glows red, then let it cool. After it cools, it no longer fights back. You've broken its spirit, trashed its vinyl record collection, and told it several abusive yo mama jokes. Hence, no fight left. It stays where you bend it.
Of course, it's weaker now, so you have to be more careful, and I don't know yet if annealing it may affect its strength as a handle. Or, it could be the original was annealed, and that's why the handle on GJ's phaser has so many dents. Plus, the cylindrical shape, the popsicle sticks, the end plug, and the Hubbel connector at the top may be all the reinforcement it needs. We'll see. When I anneal it, I'll definitely shoot pictures and probably video. No sense only one of us learning if this goes t!ts-up on me.
So now we're onto the end plate. Not 100% thrilled with the ultimate result here, but most of the method is solid and most mistakes are worth sharing...
I started with the phaser 1 screw (the one that holds the door in place) since from the photos, it looks about the right diameter and it's also a flathead. And the eyeball test results are very good.
So that's what I'll use to gauge my progress. Now, I have to find the right bit to start the pilot hole for it. Something very tiny....
Zathras correct. Not the one.
Took me like 30 minutes to find the drill bits. They were in the machine cabinet, right where they were supposed to be, laughing at me. Come to think of it, there was a lot of laughing at me last night. I probably shouldn't have told anyone I was wearing a thong...
Anyway, I may be doing something wrong, but the drill presses at the shop vibrate like a SCUD missile with diarrhea.
So I use the knee mill for drilling as well as milling.
It's orders of magnitude more precise, which is important because things like off-center holes really jump out at you. Usually not critical for camera, but obvious to the eye. Plus, I want a lot more time on the milling machine than on the drill press. It's more useful, more versatile, easier to use, and easier to set up your work-holding, plus I get a real Tim Allen rush when I use it.
Without one, get a decent bench drill press (but check it out before you buy it), or a milling head for your lathe, or a Dremel press,
or you can make your own drill press for cheap.
On with the show:
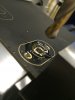
I drilled out the holes with a sacrificial piece of aluminum scrap underneath to avoid bending the brass, starting with a tiny screw and working my way up to the proper diameter. The great thing about a milling machine is the precision table movement. If you need a perfectly straight row of holes, you're in business. Just turn one crank, and you move in a straight line on only one axis. And for R-L movement, it has a variable speed auto-feed, which makes milling straight lines a breeze.
And this is where Fonzie jumps the shark. After this, I was very tired (the hour, as Dylan and Hendrix say, was getting late), and that's when you start screwing up. Don't work tired. You get stupid, and it's actually dangerous around heavy machinery. I won't even look at the lathe if I'm not fresh. And don't try to rush.
There is no rush in a machine shop, ever.
So back to me making a sow's ear out of a silk purse:
I figured I'd just do the countersink for the screws and the butterfly-shaped cutout with my Dremel, either grinder or burr bits. I see you shaking your head. I was tired, ok?
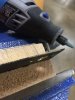
Made a mess, ruined a couple of grinder bits, and it turns out burr bits REALLY chatter and mess up your work when you use them on metal, and I never got close to completely countersinking the screw. Don't think I can't hear you chuckle. I'm onto you,
buddy.
So that was about the time I remembered we had countersinks in the machine shop. Like I said, tired.
You don't need them as heavy-duty as these if you're not a machinist, but they certainly do the job. You can probably get pretty good ones at Home Depot or Lowe's.
To find the right countersink for your screw, just drill a line of holes in a block of scrap wood big enough for the screw, then try different countersinks till you find the right one by making the countersink and dropping in your screw. I lucked out on the first try.
Way more better! Nice, smooth countersinks, perfectly centered... to each other... more on that wee problem later.
Now that the holes are cut and there's only final shaping left, I roughed out the cut on the metal bandsaw. The blade worked much better on the thicker brass, but I didn't take any chances with the curves. I wanted to file those.
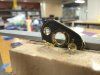
You'll notice the paint is all scratched off after the bandsaw. I certainly did.
Again, file only in one direction away from the handle and away from yourself. With patience, you'll pick it up in no time.
I put it against the MM handle, and traced around it with a red Sharpie. Just file away the red part.
And for the straight sides, use a square against only ONE of the wood blocks to get the piece perpendicular to
that block. If you rest it on both blocks, you'll probably be out of square. You can square up your file against that same block of wood. Use gentle, deliberate strokes, lightly pressing the file against the work piece, not down onto the wood. Otherwise you'll file into the wood and go out of square again.
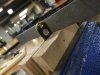
Now, remember, this is a one-off project. I would not go trying to outfit phasers for a landing party with these techniques. I'd do 90% of the work on the CNC mill, probably stacking the brass sheets to do them all in one pass. If I ever have a chance to do that, I'll certainly put up a thread. For this, though, filing after the bandsaw is fine.
I've hit that 24-file wall, so onto the next post - tomorrow. I'm pooped. Just a quick wrap-up of this session remaining, plus what I was talking about when I mentioned my countersinks only being in line with each other.
