Immobliss
New Member
Hello everyone!
Over the past two months I have been building a set of Volstagg armor for my very first client. It was an ambitious endeavor and their were pitfalls along the way but it taught me a lot about foam smithing and what materials work best for certain designs. Let's get started!
I began this endeavor with reference art. Volstagg actually doesn't have a lot of imagery to go off of. There are some fan art piece, some movie art pieces and a few shots from the first Thor movie to go off of but other than that...it was slim pickings for reference material. I had a lot of guess work to do but I did not mind as I was given creative licenses for this build by my client. Here are the designs I settled on as my reference...
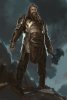
With reference in hand I gathered my client and wrapped him up in duct tape! Since I did not have the budget to create a full cast of him the duct tape dummy method worked out well (granted, the dummy lost an arm because I apparently lack the ability to tape two arms back up normally after cutting someone out of the duct tape mold). For advice on how to create a good duct tape dummy check out this tutorial video by The Woodland Elf: https://www.youtube.com/watch?v=5i7YhYMwpbc. NOTE: I would suggest cutting off/tearing off strips of tape and applying them to your model. The wrapping method actually reduces the size of the mannequin and creates fitting problems for armor builds.
Once the dummy/mannequin was created I began patterning. I used pattern ease ( a pattern fabric) and wrapped it around the mannequin...
![20150704_111601[1].jpg 20150704_111601[1].jpg](https://therpf-f28a.kxcdn.com/forums/data/attachments/242/242068-ff93566906c93d1eec1c8cb0a51feaba.jpg)
After securing the wrap with some masking tape I used my reference art, my own schematic drawings and some sharpies to draft out the patterns....
![20150704_113813[1].jpg 20150704_113813[1].jpg](https://therpf-f28a.kxcdn.com/forums/data/attachments/242/242072-c6e0b0781b2d7833c7053e117231f078.jpg)
When I was comfortable with the draft I cut out the patterns and laid them out for review...
For the armor I used a mix of materials:
3/4, 1/4 and 1/8 inch Closed Cell Foam (L200)
Insulation Foam (for more rigid items)
Faux Leather
Vinyl
I started with the chest piece as that seemed a goof place to begin and I felt most comfortable with the pattern for that item. Once all of the little pieces were cut (I used a VERY sharp utility knife - be prepared to go through LOTS of them OR have a sharpener as foam dulls knives quickly) I placed them together to test the fit then began gluing them with contact cement. NOTE: Contact Cement is TOXIC - wear gloves, a respirator and be sure to ventilate the room your are in. I used Weld Wood Contact Cement for this project (you can buy small and large containers of this at about any hardware store).
The next step in this process was applying detail to the 3/4 foam chest plate. I used 1/4 inch foam cut into strips (a trick to get straight cuts: lay masking tape down on the foam first and use it as a guide for cutting - it's MUCH easier than trying to hold a yard stick down or following a sharpie/pen line) then applied them in layers using contact cement.
![20150803_180301[1].jpg 20150803_180301[1].jpg](https://therpf-f28a.kxcdn.com/forums/data/attachments/242/242083-8720188bb3b53e7a4dbac667b0dd9114.jpg)
Now that I had the chest plate complete I filled the cracks with Mod Podge and moved on to Volstagg's belt. The belt was VERY quick. I used an exacto blade to cut detail lines into the foam where Volstagg had intricate line work and use a Heat Gun on its low setting to separate the lines and create more depth. (NOTE: DO NOT GET TOO CLOSE TO THE FOAM - keep at least 6-10 inches away when expanding your details lines or your foam will bubble). Here are some progress shots for the belt...
![20150808_074506[1].jpg 20150808_074506[1].jpg](https://therpf-f28a.kxcdn.com/forums/data/attachments/242/242085-206046ea1cc363ac9f8f833283439b81.jpg)
Next were the pauldron's and bracers. I have made these using Worbla before so I had pre-existing patterns that I was able to modify and move forward with. If you struggle with armor patterns check out Kamui Cosplay: She has armor pattern books for beginners that include male and female patterns.
With the base pieces done I quickly put together a Tunic for Volstagg then hired a friend to make a knitted hauberk as knitting and I DO NOT get along.
![20150806_201410[1].jpg 20150806_201410[1].jpg](https://therpf-f28a.kxcdn.com/forums/data/attachments/242/242091-b8bf46f71f00cc310a0f1735b6d9bb9c.jpg)
Now it was on to the Axe...that took ALOT of work. I started out with L200 but discovered it was not rigid enough and the design just did not satisfy my creative side. So I moved on to Insulation foam (1") and I was NOT disappointed. It was perfect...except that it took me FOUR tries before I figured out how to cut, shave and sculpt the foam without knicking it too much. Once I had the axe cut out I attached it to a piece of PVC pipe then sealed it together with Hot Glue and L200 foam. I then wrapped the Pipe in EVA foam, painted the axe and wrapped the handle again in leather. Here are a few photos of the axe in its multiple iterations...
And Here was the final Result
Volstagg Photo
I am looking forward to taking more professional photos. For more images related to this build visit my gallery HERE.
Over the past two months I have been building a set of Volstagg armor for my very first client. It was an ambitious endeavor and their were pitfalls along the way but it taught me a lot about foam smithing and what materials work best for certain designs. Let's get started!
I began this endeavor with reference art. Volstagg actually doesn't have a lot of imagery to go off of. There are some fan art piece, some movie art pieces and a few shots from the first Thor movie to go off of but other than that...it was slim pickings for reference material. I had a lot of guess work to do but I did not mind as I was given creative licenses for this build by my client. Here are the designs I settled on as my reference...
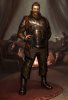
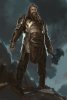
With reference in hand I gathered my client and wrapped him up in duct tape! Since I did not have the budget to create a full cast of him the duct tape dummy method worked out well (granted, the dummy lost an arm because I apparently lack the ability to tape two arms back up normally after cutting someone out of the duct tape mold). For advice on how to create a good duct tape dummy check out this tutorial video by The Woodland Elf: https://www.youtube.com/watch?v=5i7YhYMwpbc. NOTE: I would suggest cutting off/tearing off strips of tape and applying them to your model. The wrapping method actually reduces the size of the mannequin and creates fitting problems for armor builds.
Once the dummy/mannequin was created I began patterning. I used pattern ease ( a pattern fabric) and wrapped it around the mannequin...
![20150704_111601[1].jpg 20150704_111601[1].jpg](https://therpf-f28a.kxcdn.com/forums/data/attachments/242/242068-ff93566906c93d1eec1c8cb0a51feaba.jpg)
After securing the wrap with some masking tape I used my reference art, my own schematic drawings and some sharpies to draft out the patterns....
![20150704_111610[1].jpg 20150704_111610[1].jpg](https://therpf-f28a.kxcdn.com/forums/data/attachments/242/242069-82aa34963028a36b531bd4a2d453e787.jpg)
![20150704_113813[1].jpg 20150704_113813[1].jpg](https://therpf-f28a.kxcdn.com/forums/data/attachments/242/242072-c6e0b0781b2d7833c7053e117231f078.jpg)
When I was comfortable with the draft I cut out the patterns and laid them out for review...
![20150704_115448[1].jpg 20150704_115448[1].jpg](https://therpf-f28a.kxcdn.com/forums/data/attachments/242/242073-c6a7ca3d55654c125dcb3f406d6a338c.jpg)
For the armor I used a mix of materials:
3/4, 1/4 and 1/8 inch Closed Cell Foam (L200)
Insulation Foam (for more rigid items)
Faux Leather
Vinyl
I started with the chest piece as that seemed a goof place to begin and I felt most comfortable with the pattern for that item. Once all of the little pieces were cut (I used a VERY sharp utility knife - be prepared to go through LOTS of them OR have a sharpener as foam dulls knives quickly) I placed them together to test the fit then began gluing them with contact cement. NOTE: Contact Cement is TOXIC - wear gloves, a respirator and be sure to ventilate the room your are in. I used Weld Wood Contact Cement for this project (you can buy small and large containers of this at about any hardware store).
![20150706_185938[1].jpg 20150706_185938[1].jpg](https://therpf-f28a.kxcdn.com/forums/data/attachments/242/242077-a8ac3d9724927d136921fcc746cc75fc.jpg)
![20150706_190003[1].jpg 20150706_190003[1].jpg](https://therpf-f28a.kxcdn.com/forums/data/attachments/242/242078-6d528b02cc6fda430bd78fe3e1e9a69d.jpg)
The next step in this process was applying detail to the 3/4 foam chest plate. I used 1/4 inch foam cut into strips (a trick to get straight cuts: lay masking tape down on the foam first and use it as a guide for cutting - it's MUCH easier than trying to hold a yard stick down or following a sharpie/pen line) then applied them in layers using contact cement.
![20150801_144813[1].jpg 20150801_144813[1].jpg](https://therpf-f28a.kxcdn.com/forums/data/attachments/242/242082-ad3eaf2d1b33c29d4c9d839eefe18bec.jpg)
![20150803_180301[1].jpg 20150803_180301[1].jpg](https://therpf-f28a.kxcdn.com/forums/data/attachments/242/242083-8720188bb3b53e7a4dbac667b0dd9114.jpg)
Now that I had the chest plate complete I filled the cracks with Mod Podge and moved on to Volstagg's belt. The belt was VERY quick. I used an exacto blade to cut detail lines into the foam where Volstagg had intricate line work and use a Heat Gun on its low setting to separate the lines and create more depth. (NOTE: DO NOT GET TOO CLOSE TO THE FOAM - keep at least 6-10 inches away when expanding your details lines or your foam will bubble). Here are some progress shots for the belt...
![20150803_180312[1].jpg 20150803_180312[1].jpg](https://therpf-f28a.kxcdn.com/forums/data/attachments/242/242084-eb0810c7a83c9911f1e56ac3a128fca9.jpg)
![20150808_074506[1].jpg 20150808_074506[1].jpg](https://therpf-f28a.kxcdn.com/forums/data/attachments/242/242085-206046ea1cc363ac9f8f833283439b81.jpg)
Next were the pauldron's and bracers. I have made these using Worbla before so I had pre-existing patterns that I was able to modify and move forward with. If you struggle with armor patterns check out Kamui Cosplay: She has armor pattern books for beginners that include male and female patterns.
![20150706_191153[1].jpg 20150706_191153[1].jpg](https://therpf-f28a.kxcdn.com/forums/data/attachments/242/242087-65b869d696c9776a46f2e45a9ca50755.jpg)
![20150806_201330[1].jpg 20150806_201330[1].jpg](https://therpf-f28a.kxcdn.com/forums/data/attachments/242/242088-58cdf6c4c1958acad36f8795b4cdcc03.jpg)
With the base pieces done I quickly put together a Tunic for Volstagg then hired a friend to make a knitted hauberk as knitting and I DO NOT get along.
![20150729_184924[1].jpg 20150729_184924[1].jpg](https://therpf-f28a.kxcdn.com/forums/data/attachments/242/242090-fbe03e1834f3962f8b45107a9dcbe9a7.jpg)
![20150806_201410[1].jpg 20150806_201410[1].jpg](https://therpf-f28a.kxcdn.com/forums/data/attachments/242/242091-b8bf46f71f00cc310a0f1735b6d9bb9c.jpg)
Now it was on to the Axe...that took ALOT of work. I started out with L200 but discovered it was not rigid enough and the design just did not satisfy my creative side. So I moved on to Insulation foam (1") and I was NOT disappointed. It was perfect...except that it took me FOUR tries before I figured out how to cut, shave and sculpt the foam without knicking it too much. Once I had the axe cut out I attached it to a piece of PVC pipe then sealed it together with Hot Glue and L200 foam. I then wrapped the Pipe in EVA foam, painted the axe and wrapped the handle again in leather. Here are a few photos of the axe in its multiple iterations...
![20150713_144437[1].jpg 20150713_144437[1].jpg](https://therpf-f28a.kxcdn.com/forums/data/attachments/242/242099-5f171f1ac54ad3632032643866f0def3.jpg)
![20150713_160326[1].jpg 20150713_160326[1].jpg](https://therpf-f28a.kxcdn.com/forums/data/attachments/242/242100-7f7ec0c60495a2602dbb04eddd928a2a.jpg)
And Here was the final Result
Volstagg Photo
I am looking forward to taking more professional photos. For more images related to this build visit my gallery HERE.
Attachments
Last edited: