Grinn3r
New Member
I'm new here and I've finally gotten my homemade vaccum forming machine set up... or at least, that's what I thought.
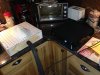
My setup uses an electric griddle (14" x 14"), a wooden box with perforated board as the top (14" x 14" x 2"), two metal frames that I clip together (12" x 12"), and an old shopvac.
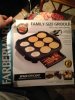
In addition, I bought two sets of plastic: clear Polycarbonate (12" x 12" .01") and black ABS (12" x 12" x 1/16")
My intention with the thicker plastic is to make masks and other props with, but preferably with the smooth side up.
The thin stuff was more of a flub on my part thinking it would be thick enough...
So I hooked this all up and put the form I was going to test the plastic I bought with. A simple plaster face mold.
Alas, neither of the plastics I bought worked.
First I heated a sheet of the ABS on the griddle at the recommended temperature of 325-350 F, but just when I thought it was ready, I pressed it down over the form and got... this:
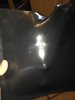
So, of course, this made me decide to try again with the thinner plastic instead to test and see if I could get it. Its heating temperature is higher, 360-400 F, so I assumed it would be more forgiving..
But... even though it became transparent and sagged some, it was as if it lost all added heat after I took it off the griddle and refused to take ANY of the form.
Then I decided to tape off the majority of the holes outside the direct area surrounding the plaster face in hopes that it would make the uncovered holes pull stronger.
I attempted to add the use of my grandfather's new heatgun to heat the top of the plastic more to temperature. Which may have been because of my impatience or frustration, but I was met with no success then either.
For anyone that knows a lot (or at least more) about this, could you give me some pointers?
I really want to know what all I'm doing wrong.
What temperature should I set these to?
How long do I wait until these are heated sufficiently?
What strength does my vaccum need to be to make this work?
How much time do I have to get the plastic off the heating element and onto the form?
Any immediate response would be greatly appreciated, my project deadline is a few months away, but I just really want to get this solved as soon as possible.
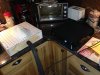
My setup uses an electric griddle (14" x 14"), a wooden box with perforated board as the top (14" x 14" x 2"), two metal frames that I clip together (12" x 12"), and an old shopvac.
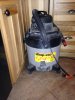
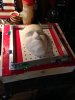
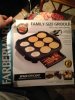
In addition, I bought two sets of plastic: clear Polycarbonate (12" x 12" .01") and black ABS (12" x 12" x 1/16")
My intention with the thicker plastic is to make masks and other props with, but preferably with the smooth side up.
The thin stuff was more of a flub on my part thinking it would be thick enough...
So I hooked this all up and put the form I was going to test the plastic I bought with. A simple plaster face mold.
Alas, neither of the plastics I bought worked.
First I heated a sheet of the ABS on the griddle at the recommended temperature of 325-350 F, but just when I thought it was ready, I pressed it down over the form and got... this:
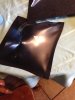
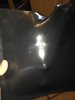
So, of course, this made me decide to try again with the thinner plastic instead to test and see if I could get it. Its heating temperature is higher, 360-400 F, so I assumed it would be more forgiving..
But... even though it became transparent and sagged some, it was as if it lost all added heat after I took it off the griddle and refused to take ANY of the form.
Then I decided to tape off the majority of the holes outside the direct area surrounding the plaster face in hopes that it would make the uncovered holes pull stronger.
I attempted to add the use of my grandfather's new heatgun to heat the top of the plastic more to temperature. Which may have been because of my impatience or frustration, but I was met with no success then either.
For anyone that knows a lot (or at least more) about this, could you give me some pointers?
I really want to know what all I'm doing wrong.
What temperature should I set these to?
How long do I wait until these are heated sufficiently?
What strength does my vaccum need to be to make this work?
How much time do I have to get the plastic off the heating element and onto the form?
Any immediate response would be greatly appreciated, my project deadline is a few months away, but I just really want to get this solved as soon as possible.
Last edited: