The Museum Collection swords from United Cutlery are famously hella expensive. I managed to get one of the later serial numbers. Apparently they were unable to sell the later ones and some places bought them up for cheap. I got this from an online toy store for between 200-300 dollars: Oiled and set in styrofoam, with no glass case or accessories. I had to double check with them via email because I didn’t believe it.
I think this was around 2017… anyway it is absolutely stunning. Unlike the normal Sting, this is much thinner, much more sharply machined and feels like an actual weapon. Well balanced and pretty.
Unfortunately the light chemical weathering did not age well. Since, even with wax it’s been darkening like the Roman’s empire MPP chrome thing. Also the vinyl decal on the handle has been peeling
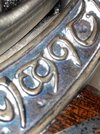
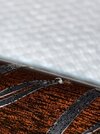
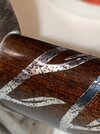
So I’ve been mildly anxious about losing the detail. What do I do if it peels off or rips? Is my sword just going to get darker and more yellow/black?
Some might know me in the Star Wars section, I’m a bit of a monster. My collection honestly is meant to be handled and I have long term goals of keeping the awesome fantasy alive. I’d hate to look at this in 20 years and see it degraded.
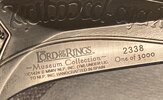
What follows may make collectors cringe. I apologize in advance, and this is your warning to avert your eyes if you need to.
I have a very robust set of skills in the workshop so I first tried to polish off the dark tarnish. Unfortunately it looks like it’s a plating or heavy coat and I slipped and marred some of the handle. **** up #1
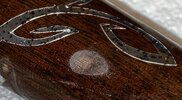
Can’t really go back from that so I’ve been staring at this on my wall (I made a casual wall mount for myself) and thinking.. what to do. Ever since more of the handle decal has started to peel more and I thought… okay I need a plan.
Looking at this, which I got for 1/3 the price I remembered that I’ve built a carbon steel sword already. I’ve done machining and turning and repairs all over my collection and my house. So I decided to do two things:
1) re-finish the handle. Stain and clear hard coat, it will look beautiful. But what about the decal?! I’m going to make a template, engrave and inlay silver solder into the handle, the way the original design was intended. Weta couldn’t pull that off in 1999 and they do it now with their special collectibles they sell. Of course, they CNC the inlay, I’m just going to do it the best I can, possibly soldering the leaves to the main spiral.
2) I’m going to finish polishing the handle hardware. I was going at weird angles because the handle was still attached. Any issues with re-installation I can machine and fix myself. I’ll use the luthier Fish Glue I use for guitars and pianos that can take high tension, or epoxy where need-be.
This is going to be a beautiful sword when I’m done, and the actual materials are stunning. This is my own unique decision and I’m not suggesting anyone else try this.
For educational purposes, if anyone else has an accident, I will include pictures of the structure inside the sword.
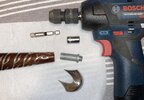
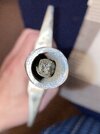
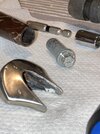
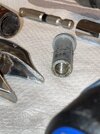
The end is epoxied on. There is a steel threaded insert with a hex head supporting the end of the tang, which ends about where the last leaf, pointing down, lays. I did need a hammer drill to undo the insert.
I think this was around 2017… anyway it is absolutely stunning. Unlike the normal Sting, this is much thinner, much more sharply machined and feels like an actual weapon. Well balanced and pretty.
Unfortunately the light chemical weathering did not age well. Since, even with wax it’s been darkening like the Roman’s empire MPP chrome thing. Also the vinyl decal on the handle has been peeling
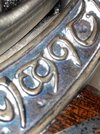
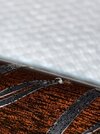
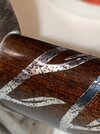
So I’ve been mildly anxious about losing the detail. What do I do if it peels off or rips? Is my sword just going to get darker and more yellow/black?
Some might know me in the Star Wars section, I’m a bit of a monster. My collection honestly is meant to be handled and I have long term goals of keeping the awesome fantasy alive. I’d hate to look at this in 20 years and see it degraded.
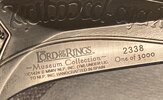
What follows may make collectors cringe. I apologize in advance, and this is your warning to avert your eyes if you need to.
I have a very robust set of skills in the workshop so I first tried to polish off the dark tarnish. Unfortunately it looks like it’s a plating or heavy coat and I slipped and marred some of the handle. **** up #1
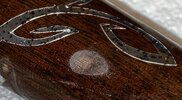
Can’t really go back from that so I’ve been staring at this on my wall (I made a casual wall mount for myself) and thinking.. what to do. Ever since more of the handle decal has started to peel more and I thought… okay I need a plan.
Looking at this, which I got for 1/3 the price I remembered that I’ve built a carbon steel sword already. I’ve done machining and turning and repairs all over my collection and my house. So I decided to do two things:
1) re-finish the handle. Stain and clear hard coat, it will look beautiful. But what about the decal?! I’m going to make a template, engrave and inlay silver solder into the handle, the way the original design was intended. Weta couldn’t pull that off in 1999 and they do it now with their special collectibles they sell. Of course, they CNC the inlay, I’m just going to do it the best I can, possibly soldering the leaves to the main spiral.
2) I’m going to finish polishing the handle hardware. I was going at weird angles because the handle was still attached. Any issues with re-installation I can machine and fix myself. I’ll use the luthier Fish Glue I use for guitars and pianos that can take high tension, or epoxy where need-be.
This is going to be a beautiful sword when I’m done, and the actual materials are stunning. This is my own unique decision and I’m not suggesting anyone else try this.
For educational purposes, if anyone else has an accident, I will include pictures of the structure inside the sword.
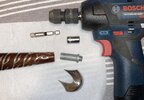
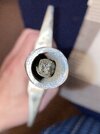
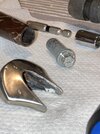
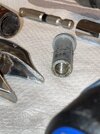
The end is epoxied on. There is a steel threaded insert with a hex head supporting the end of the tang, which ends about where the last leaf, pointing down, lays. I did need a hammer drill to undo the insert.