Radioman
Active Member
I was reading a thread on The RPF where users were giving their advice on how to begin making props. The best advice of that whole thread was "Just start". So I took that to heart and decide to dip my toes into pepakura.
Here's my first attempt. I have had this Magneto file for several months and I don't know who to credit for it so I apologize for that.
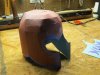
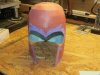
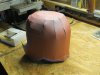
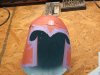
This file contained only 9 sheets so it's not a very hires pep, as evident by the slight buckling on the curves on the upper back. I picked it because it was the smallest and easiest looking file I could find. Again, this is a project to dip my toes into the water.
This took me roughly five hours to get to that point. Just turn on the TV or music and get into the zone.
I didn't do the bridge of the nose detail because on the printed pep, it was really kind of a confusing mess. I might do a hybrid comic / X-Men First Class (ending) since that bridge is cool, while not as spindly.
My next step, from what I see, is Fiberglass resin. Heading out to Lowe's this morning to get that. I need to figure out a way to set the "jaws" of the helmet in place before I resin. Any advice there would be much appreciated.
Here's a question. My thought is to to a coat of resin inside and out and then loading the inside with the fiberglass mesh and another layer of resin. I've been following the YouTube series by boochieboy814 so that seems like a good method.
However, I'd like to perhaps to a clay build on the edges and front "flare" on the Magneto helmet, like the in First Class. Question #1: Once I resin, can I build the clay, then resin again to seal in the clay prior to moving to the bondo stage?
Of course, if I'm screwing up any of this, or if my pep build is crap, anyone can point that out to me as well.
Thanks for reading and any help, in advance.
Mark
Here's my first attempt. I have had this Magneto file for several months and I don't know who to credit for it so I apologize for that.
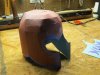
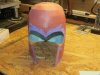
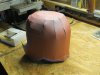
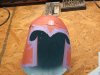
This file contained only 9 sheets so it's not a very hires pep, as evident by the slight buckling on the curves on the upper back. I picked it because it was the smallest and easiest looking file I could find. Again, this is a project to dip my toes into the water.
This took me roughly five hours to get to that point. Just turn on the TV or music and get into the zone.
My next step, from what I see, is Fiberglass resin. Heading out to Lowe's this morning to get that. I need to figure out a way to set the "jaws" of the helmet in place before I resin. Any advice there would be much appreciated.
Here's a question. My thought is to to a coat of resin inside and out and then loading the inside with the fiberglass mesh and another layer of resin. I've been following the YouTube series by boochieboy814 so that seems like a good method.
However, I'd like to perhaps to a clay build on the edges and front "flare" on the Magneto helmet, like the in First Class. Question #1: Once I resin, can I build the clay, then resin again to seal in the clay prior to moving to the bondo stage?
Of course, if I'm screwing up any of this, or if my pep build is crap, anyone can point that out to me as well.
Thanks for reading and any help, in advance.
Mark