JessTheMullet
New Member
I have the electronics soldered together, and I've tested it out. The switch isn't going to fit where I'd originally planned, which is disappointing. However, it's really easy to pop it open to turn it on/off and close it again, thanks to the magnets.
I've got some light tubing that I'll put in the holes of the body, and I'll stick the LEDs so they shine through it. If I want it a little brighter, I might stick some foil to the back of the tubing. They're pretty bright, though, and that shouldn't be an issue.
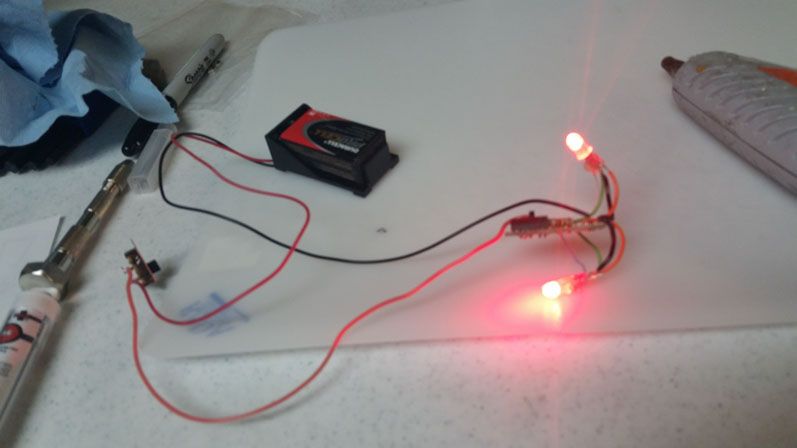
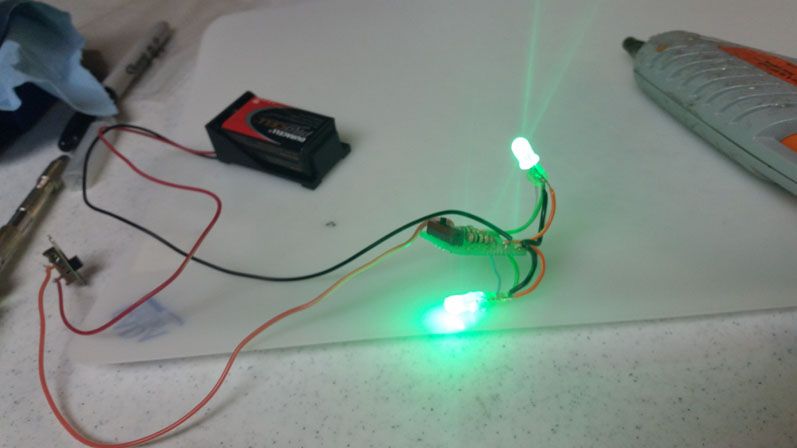

I've got some light tubing that I'll put in the holes of the body, and I'll stick the LEDs so they shine through it. If I want it a little brighter, I might stick some foil to the back of the tubing. They're pretty bright, though, and that shouldn't be an issue.