Weapioneer
Active Member
Greetings,
I am building a couple of katanas for a cosplay, just a regular plain set of katanas out of plywood. I am just going to cut it out, shave it down to a blunt edge and make a tsuba out of pvc. Problem is, i want the katana to have a good finish, so it looks like a real or atleast close katana. I have spray paint, but the effect it produces is somewhat like this -->
rather than more metallic. I was thinking of using this as a base coat, then applying aluminum foil on the top of it like-->
But when I did a test run, i could not get it nearly as smooth as this guy did, always leaving streaks no matter what i tried. Can someone either suggest a better way to achieve a realistic katana with a hamon or way to get the foil this smooth?
Thanks.
I am building a couple of katanas for a cosplay, just a regular plain set of katanas out of plywood. I am just going to cut it out, shave it down to a blunt edge and make a tsuba out of pvc. Problem is, i want the katana to have a good finish, so it looks like a real or atleast close katana. I have spray paint, but the effect it produces is somewhat like this -->
rather than more metallic. I was thinking of using this as a base coat, then applying aluminum foil on the top of it like-->
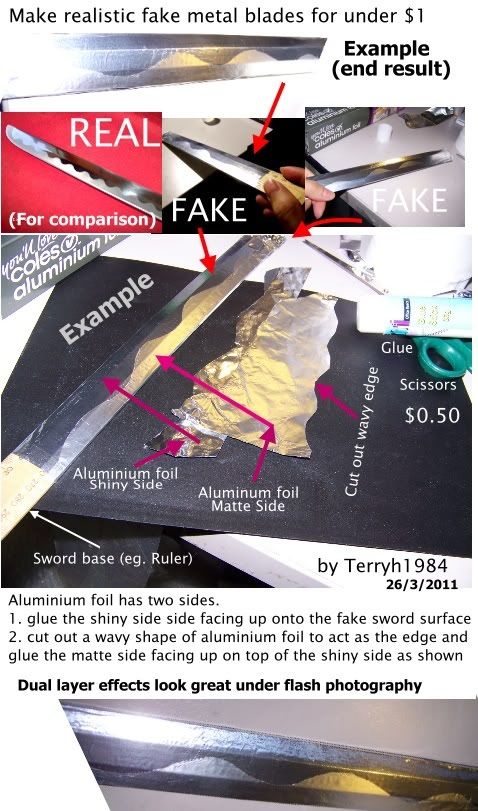
But when I did a test run, i could not get it nearly as smooth as this guy did, always leaving streaks no matter what i tried. Can someone either suggest a better way to achieve a realistic katana with a hamon or way to get the foil this smooth?
Thanks.