Nako
New Member
Hi everyone! 
I'm Fernando from Argentina, I've been lurking the forums for more than a year now, i've first visited 405th and became very interested in their costumes. Then someone linked to this forum and my adventure began. I got amazed since the beginning and started searching and researching everything i could, went from left to right and looked at every corner of the forum, I found threads from all kinds, all nations and all tastes, read them and learned everything i could, I was inspired by some of the best artist I've seen, skillful and precise, delicate and patient above all. All that said, i'll start my thread.
Iron Man Mark VII
I chosen the Mark VII because when I started this project it was near the first avengers premiere, and I also liked it a lot, but the time passed, i got out of the project and delayed it more and more untill i dropped it completely, some months later a very good friend of mine made me a proposal. Wo could get some money with the costume, as a tourist attraction, We would finish it together, as a team, and then work together at least 1 season. It was pretty cool for me, I got to work in something I like, and make some money in the process. So the building began.
It's sensible to clarify that we are on a budget, a tight budget x(, so we have to find cheaper alternatives for anything we could.
First of all I needed the raw materials and tools. I started with repairing my old and battled Epson C45, that lacks some of it parts but still works (kinda, you need to watch it close so it does't destroy the paper), got pepakura viewer, and... paper. Oh wait no, I didn't, because just so happens that I live in what seems like the middle of the desert (metaforically), because I searched my entire town and found nothing. One library sent me to another, and another, and it never ended. I was directed to some major paper factories outside of the town just to get the paper. Or I could buy it online, but that means paying the delivery, and waiting up to 2 weeks (yep, that's what it takes here to deliver a package), and the handling and transportations costs me more than the paper itself. And that's just the beggining, because finding about anything here was the same trouble. Finally after days of searching I found a store that had one stored from archaic ages, and luckily the price was fair. So, I started with the printing.
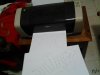
The printing part was no major problem except for the fact that I needed to take care of every single paper separately because the printer would get stuck a lot.
At first I used a cutter, but the blades got blunt just too quick, after 5 / 6 pages actually, and the only use left was cutting the inner lines. I started to search for a X-acto knife everywhere, but I couldn't find any, there were just crappy knockoffs that wont even cut warm butter. So I decided to make one, I bought some blades from art stores and libraryes, found and old and dry marker in a drawer, and got a tweezer from the bathroom (an old and discarded one).
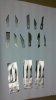
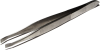
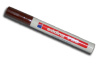
First i grabbed the blade with the tweezer and taped it with paper tape (very tight and lots of tape). then I emptied the marker and removed the tip. Then inserted the tweezer with the blade inside, very strongly (please be careful here or you could end up harmed) until the tweezer was no longer visible, and taped that to the marker. And voilá, X-acto knife ready for action.
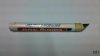
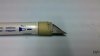
Note: The knife is now with an old blade that has been sharpened with a grinding stone.
Ok, then I started the cutting process. I used small transparent plastic bags to separate each piece of the armor, and wrote in it wich piece was inside with a permanent marker (not the one I used to make the knife though
). After a while I went to the dentist, and he sent me to buy some stuff from a dentist specialized store, and there I found cutting heaven. In the counter there were surgical blades, I bought the ones that looked like the best suited for paper, I selected mainly two:
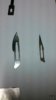
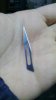
The left one is perfect for flaps, and the right one is perfect for cutting, over 15 pages and it wont blunt at all, and after that you can just cut the top of the knife (always carefully) and the blade thats left will cut like a new one. Also don't try to sharpen it with sanding paper or grinding stone for cutting, or you will just mess the blade. Here's some working on the paper.
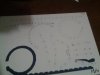
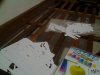
Now that I had the paper cut and ready I started the gluing process, as you can imagine, you can't glue out of air, so I needed a hot glue gun. I bought a very cheap one at first (chinese of course), it worked for a while but one day it short-circuited and melted from the inside, also it blown off my house's electricity and had to change a fuse, so you've been warned. I bought a new and more expensive one, and it works like a charm even today.
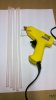
One of the first thing I've make was the scaling helmet...
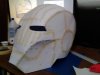
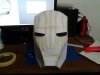
Note: Sorry for the bad quality of the pictures.
It was too large, so I scaled it down a bit to fit my head, and ended up with a perfect fit. Then I made the real one.
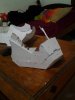
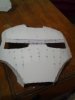
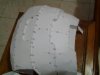
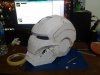
The final pep helm was a complete success, so there we go with some of the rest of the pieces.
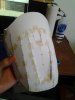
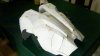
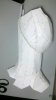
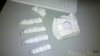

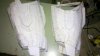
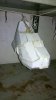
To be continued...
I'm Fernando from Argentina, I've been lurking the forums for more than a year now, i've first visited 405th and became very interested in their costumes. Then someone linked to this forum and my adventure began. I got amazed since the beginning and started searching and researching everything i could, went from left to right and looked at every corner of the forum, I found threads from all kinds, all nations and all tastes, read them and learned everything i could, I was inspired by some of the best artist I've seen, skillful and precise, delicate and patient above all. All that said, i'll start my thread.
Iron Man Mark VII
I chosen the Mark VII because when I started this project it was near the first avengers premiere, and I also liked it a lot, but the time passed, i got out of the project and delayed it more and more untill i dropped it completely, some months later a very good friend of mine made me a proposal. Wo could get some money with the costume, as a tourist attraction, We would finish it together, as a team, and then work together at least 1 season. It was pretty cool for me, I got to work in something I like, and make some money in the process. So the building began.
It's sensible to clarify that we are on a budget, a tight budget x(, so we have to find cheaper alternatives for anything we could.
First of all I needed the raw materials and tools. I started with repairing my old and battled Epson C45, that lacks some of it parts but still works (kinda, you need to watch it close so it does't destroy the paper), got pepakura viewer, and... paper. Oh wait no, I didn't, because just so happens that I live in what seems like the middle of the desert (metaforically), because I searched my entire town and found nothing. One library sent me to another, and another, and it never ended. I was directed to some major paper factories outside of the town just to get the paper. Or I could buy it online, but that means paying the delivery, and waiting up to 2 weeks (yep, that's what it takes here to deliver a package), and the handling and transportations costs me more than the paper itself. And that's just the beggining, because finding about anything here was the same trouble. Finally after days of searching I found a store that had one stored from archaic ages, and luckily the price was fair. So, I started with the printing.
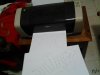
The printing part was no major problem except for the fact that I needed to take care of every single paper separately because the printer would get stuck a lot.
At first I used a cutter, but the blades got blunt just too quick, after 5 / 6 pages actually, and the only use left was cutting the inner lines. I started to search for a X-acto knife everywhere, but I couldn't find any, there were just crappy knockoffs that wont even cut warm butter. So I decided to make one, I bought some blades from art stores and libraryes, found and old and dry marker in a drawer, and got a tweezer from the bathroom (an old and discarded one).
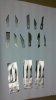
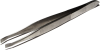
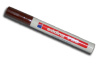
First i grabbed the blade with the tweezer and taped it with paper tape (very tight and lots of tape). then I emptied the marker and removed the tip. Then inserted the tweezer with the blade inside, very strongly (please be careful here or you could end up harmed) until the tweezer was no longer visible, and taped that to the marker. And voilá, X-acto knife ready for action.
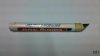
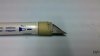
Note: The knife is now with an old blade that has been sharpened with a grinding stone.
Ok, then I started the cutting process. I used small transparent plastic bags to separate each piece of the armor, and wrote in it wich piece was inside with a permanent marker (not the one I used to make the knife though
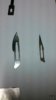
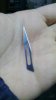
The left one is perfect for flaps, and the right one is perfect for cutting, over 15 pages and it wont blunt at all, and after that you can just cut the top of the knife (always carefully) and the blade thats left will cut like a new one. Also don't try to sharpen it with sanding paper or grinding stone for cutting, or you will just mess the blade. Here's some working on the paper.
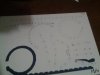
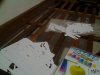
Now that I had the paper cut and ready I started the gluing process, as you can imagine, you can't glue out of air, so I needed a hot glue gun. I bought a very cheap one at first (chinese of course), it worked for a while but one day it short-circuited and melted from the inside, also it blown off my house's electricity and had to change a fuse, so you've been warned. I bought a new and more expensive one, and it works like a charm even today.
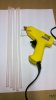
One of the first thing I've make was the scaling helmet...
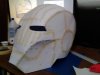
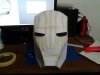
Note: Sorry for the bad quality of the pictures.
It was too large, so I scaled it down a bit to fit my head, and ended up with a perfect fit. Then I made the real one.
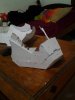
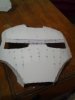
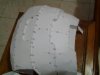
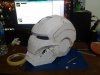
The final pep helm was a complete success, so there we go with some of the rest of the pieces.
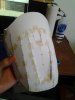
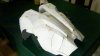
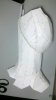
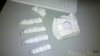

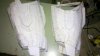
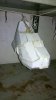
To be continued...