drjag
Well-Known Member
For my End Of Year show and my final term of studying my extended BTEC diploma (before going off to university), our assignment is to produce any piece (or pieces) of work to present for a public and private exhibition that will be hosted near our college, that demonstrates your best abilities as an "artist" and to promote your own work, so I thought what better than to document it on TheRPF!
The plan for my end of year work is to make a Daft Punk Tron era Guy helmet as my main piece, alongside other props I will make throughout the term. I know these Daft Punk helmets have been done to death on this forum and other forum sites so to counter that, I'm doing my own twist on the helmet. This helmet won't include lighting as I'm not skilled in the electronics department, but I will be installing headphones and lining it to fit my head perfectly, as I have always wanted to make a Daft Punk helmet that can play internal music.
At this stage I have already done a lot of the main steps, so I'll be posting in sections, alongside the other work and changes as well. And with that, lets go!
With the time frame I have and the limitations of budget and materials, I had to go the Pepakura route with this one; I used JTM's Tron Guy helmet file as I found this model suited my needs more than other available models. Although I would of loved to have approached the MDF/foam method to make my master, this would have taken much longer and required more materials.
Total time of Pepakura assembly: 16-17 hours.
Scale: Ear to ear, 7 inches | Front chin to back panel, 11 inches | Base to top, 10 inches.
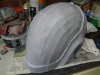
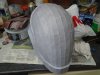
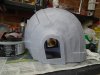
If you have noticed that the "ears" are missing, it's because I wanted to tackle this with a different approach other then Pepakura; I knew it would take far more effort to get the ears right in Pepakura so I'll make 'em another way. Next step is resining/fiberglassing. I did 2 coats of resin on the outside, 1 layer of fiberglass on the inside and 2 coats of body filler/resin mix on the inside for extra rigidity.
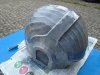

Like all pep helmets, body filler comes after fiberglass; I also used Milliput (Epoxy Putty) to widen the rim of the visor boarder to thicken and even out the distance.
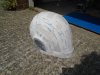
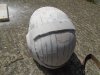
Refinement:
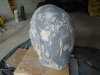
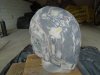
Many hours of sanding, priming and filling got me to this stage:
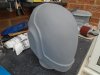
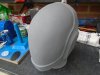
During the process of making the master, I ended up "simplifying" the overall shape by blending everything together; this was both a feature I wanted to differentiate from other DP helmets, plus it meant I could work quicker. The next stage is the molding process which will include the main mold and the mother mold so stay tuned!
The plan for my end of year work is to make a Daft Punk Tron era Guy helmet as my main piece, alongside other props I will make throughout the term. I know these Daft Punk helmets have been done to death on this forum and other forum sites so to counter that, I'm doing my own twist on the helmet. This helmet won't include lighting as I'm not skilled in the electronics department, but I will be installing headphones and lining it to fit my head perfectly, as I have always wanted to make a Daft Punk helmet that can play internal music.
At this stage I have already done a lot of the main steps, so I'll be posting in sections, alongside the other work and changes as well. And with that, lets go!
With the time frame I have and the limitations of budget and materials, I had to go the Pepakura route with this one; I used JTM's Tron Guy helmet file as I found this model suited my needs more than other available models. Although I would of loved to have approached the MDF/foam method to make my master, this would have taken much longer and required more materials.
Total time of Pepakura assembly: 16-17 hours.
Scale: Ear to ear, 7 inches | Front chin to back panel, 11 inches | Base to top, 10 inches.
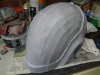
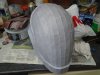
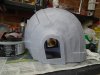
If you have noticed that the "ears" are missing, it's because I wanted to tackle this with a different approach other then Pepakura; I knew it would take far more effort to get the ears right in Pepakura so I'll make 'em another way. Next step is resining/fiberglassing. I did 2 coats of resin on the outside, 1 layer of fiberglass on the inside and 2 coats of body filler/resin mix on the inside for extra rigidity.
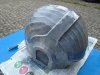

Like all pep helmets, body filler comes after fiberglass; I also used Milliput (Epoxy Putty) to widen the rim of the visor boarder to thicken and even out the distance.
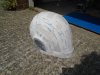
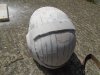
Refinement:
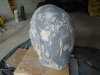
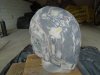
Many hours of sanding, priming and filling got me to this stage:
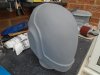
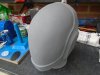
During the process of making the master, I ended up "simplifying" the overall shape by blending everything together; this was both a feature I wanted to differentiate from other DP helmets, plus it meant I could work quicker. The next stage is the molding process which will include the main mold and the mother mold so stay tuned!
Last edited: