I started my first project before I found and joined this site. I guess I am about 30-40% complete so far and am trying to finish before September 18th, 2015(Columbus Wizard World) without sacrificing quality. This is my first ever costume/my first ever forum so go easy but by all means if you have ideas criticism let me know!
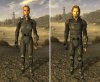
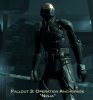
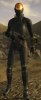
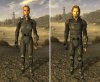
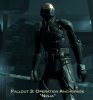
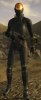
Last edited: